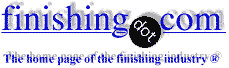
-----
Passivation of 17-7PH stainless steel: Type II or Type VIII?
Q. I've been asked to investigate the differences between type II and type VIII passivation of 17-7PH SS. Net searches aren't much help with 17-7PH, but did produce some hits for 316. Some of these hits say that the temperature is the driving factor and others say that the nitric acid concentration is the driving factor. Can the difference be specific to the steel type?
My guess is that bath temperature AND concentration of nitric acid are both contributing to the passivation; therefore, higher temp and concentration is the way to go. Anyway of backing up my guess?
Thanks!
- San Antonio, Texas
2006
A. Types II and VIII are both listed as suitable for 17-7 PH. A Carpenter Stainless Steel handbook says "The addition of sodium dichromate or use of 50% nitric acid increases the 'passivation potential' of the bath so that undesirable local attack is less likely."
The solutions' oxidation potentials could probably be measured as ORP. But, what matters is any difference in the resulting passivation layer. You could measure its thickness, electrical resistance, time for electrochemical dissolution under controlled conditions, or do humidity or salt spray tests.
Let us know any findings, please.
- Goleta, California

Rest in peace, Ken. Thank you for your hard work which the finishing world, and we at finishing.com, continue to benefit from.
2006
A. Jesse, what is it you want to investigate? Both passivation processes have been shown to work with 17-7 stainless steel. They will also both not work if you do them wrong. If you have a choice, you'd be wise to realize that by not having to muck about with sodium dichromate, you make your formulation, your maintenance, and your disposal easier. We switched from Type II to Type VIII several years ago, and won't go back.

Lee Gearhart
metallurgist - E. Aurora, New York
2006
A. The details on the various Nitric bath Types are readily available in ASTM A967 or even in the now defunct QQ-P-35C (canceled) [link is to free spec at Defense Logistics Agency, dla.mil]. citric acid based passivation can also be used.
adv.
Let us know if we can help.
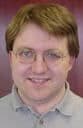
Ray Kremer
Stellar Solutions, Inc.

McHenry, Illinois
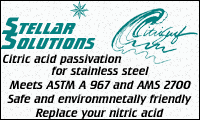
2006
June 28, 2016
Q. We have some small 17-7 parts in condition TH1050. Unfortunately they have been unprotected on our shelf for about 7 years. They are thin stamped parts and appear to have a discoloration from heat treatment.
We recently added passivation in accordance to ASTM A967. The parts had been pulled from the shelf and sent out, our vendor returned the parts claiming that they started to rust during the passivation process.
There is concern that the certification is incorrect and they are not 17-7.
My thought is that they parts have been stamped using a steel tool, heat treated to TH1050 with unknown cleaning after and then sat on the shelf for many years in an unprotected and open environment. It is also not know what method of passivation was used when the rust appeared.
Is it likely that these parts could be dirty or even lightly corroded prior to the passivation process and that caused the attack or is it more likely that they are truly the incorrect material?
Thank you
Dan
- Cleveland, Ohio USA
A. Hi Dan,
ASTM A967 recommends passivation of precipitation-hardening stainless steels using the Nitric 1 (20-25% v/v nitric acid, 2.5% ± 0.5% weight sodium dichromate, 20 minutes minimum, 120-130 deg F) or Nitric 4 (45-55% v/v nitric acid, 30 minutes minimum, 120-130 deg F).
It is possible that these parts were not passivated IAW the guidelines of the spec. The spec does also have recommended procedures for other grades of stainless steel.
I hope this is helpful!
- Milwaukee, Wisconsin, USA
July 6, 2016
A. Dan,
Too little information, obviously.
The idea of new rust forming while a part is in the passivation acid bath is absurd, however it can happen during the subsequent water rinses.
If they are 17-7 or some other variation of stainless, it shouldn't be that hard to clean up that corrosion and passivate them using a properly formulated citric acid based product.
Let us know if we can help.
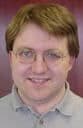
Ray Kremer
Stellar Solutions, Inc.

McHenry, Illinois
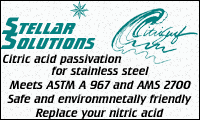
July 12, 2016

this text gets replaced with bannerText
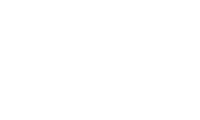
Q, A, or Comment on THIS thread -or- Start a NEW Thread