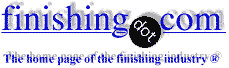
-----
Phosphoric acid sludge removal
2006
Hello!
I am working in a terminal and receive Phosphoric acid product to respective tank, after long period sludge forms at the bottom of the tank and clogged the suction nozzle, specially during pumping out the product by pump the suction line of the pump chocked and the pump start cavitation. my question how can I remove the sludge before receiving or after receiving.
is there any method could be used to prevent or remove sludge formation
- Saudi Arabia
Is the sludge impurities, corrosion products or simply, thickened phosphoric acid?
If this is 85% phosphoric acid, maybe the latter case (100% acid has melting point 42°C). You could add heating coils near bottom of the tank, add variable speed controls to the pump motor, switch to a more suitable pump, or add an agitator.
I suggest contacting Sulzer Pumps re SALOMIX¹ agitators (up to 25 meter shaft length) for phosphoric acid slurries. They also have suitable pumps and filters (if needed).
- Goleta, California

Rest in peace, Ken. Thank you for your hard work which the finishing world, and we at finishing.com, continue to benefit from.
2006
April 19, 2008
I am currently facing a challenge of a similar nature in my factory (Omnia Phosphates, Rustenburg, South Africa). I am busy with a research and the following might be of interest:
Phosphoric acid is mainly pure, the sludge comes from excess material which is unfortunately part of the Phosphate Rock - reacting with the acid itself and forming new Metal-P2O5 compounds.
The three factors that needs investigation are:
As the concentration increases, so does the probability of reaction. Armed with this information, theoretically filtration (separation) should be considered at a higher concentration - >38%
Cooling improves crystallization as well. If it is possible in your process, reduce the temperature to below 20 °C before filtration
Lastly, but more important: The final retention time for your storage tanks/thickener/settlers will have a considerable impact on your final product. The higher the retention time the better sludge will settle. This last thought is the one that you will like to avoid maximizing since it means you will have to handle more sludge at a later stage of your processing.
Please feel free to discuss and maybe we can come to a solution to this age old problem.
Kind Regards,
- Rustenburg, South Africa
Q, A, or Comment on THIS thread -or- Start a NEW Thread