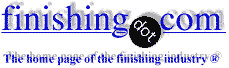
-----
Chemical Conversion Coating on EDM Surfaces
Parts have a white powdery contamination on EDM [electro discharge machining] surface. What is the cause? What can be done to prevent this?
Paul WalshMachining job shop - Topsfield, Massachusetts
2006
It may prove impossible to answer from this distance anyway, Paul, but what is the alloy, and what kind of chemical conversion coating are you speaking of?
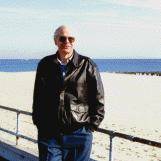
Ted Mooney, P.E.
Striving to live Aloha
(Ted can offer longterm or instant help)
finishing.com - Pine Beach, New Jersey
2006
Ted:
The material is 6061-T651, and the chemical film is AMSC5541 CLASS 1A
- Topsfield, Massachusetts
2006
Chromates can turn powdery at any temperature over 140 °F, the more so if adequate curing time of at least a day hasn't been allowed for. Also remember that the operative phrase is 'chemical conversion coating', indicating a conversion reaction on the substrate caused by chemicals designed to convert that substrate. A surface which is no longer 6061 alloy will not convert properly. You may need to find out what the surface is after EDM and do an etch or deoxidation or desmut that restores an active surface. Sorry for the very general response.
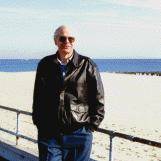
Ted Mooney, P.E.
Striving to live Aloha
(Ted can offer longterm or instant help)
finishing.com - Pine Beach, New Jersey
2006
I have little experience on EDM aluminum, but it is well known that, when used on steel, this process leaves a very hard and stubborn scale of oxide that must be removed prior to any chemical treatment. I am sure the same happens with aluminum. Maybe you have to check if your pretreatment is dealing with this effectively.
Guillermo MarrufoMonterrey, NL, Mexico
2006
The parts go through the EDM process, and then after an extended period of time are chem-filmed. Could this be a layer of aluminum oxide that is affecting the chemical conversion process? I am assuming that an etch after EDM would restore the active surface. Would you agree?
Paul Walsh- Topsfield, Massachusetts
2006
An etch only dissolves aluminum and aluminum oxides, leaving copper and other alloying materials on the surface. You may be able to restore the condition of the metal surface with an etch followed by a desmut. But I would have thought that this was SOP [standard operating procedure] for the parts anyway (you don't usually just dip parts in chem film, you usually go through a non-etch cleaning, etch, and desmut cycle first).
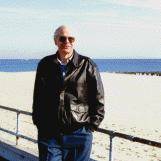
Ted Mooney, P.E.
Striving to live Aloha
(Ted can offer longterm or instant help)
finishing.com - Pine Beach, New Jersey
2006
I also can not speak with authority, but there are several possibilities. The copper comes out of solution. Some carbides are formed. Some oxides are formed. Not easy to clear this mess well enough to chem-film.
James Watts- Navarre, Florida
2006
Because of the tight tolerances of the parts that we make, we prohibit the use of etch cleaners on any of our parts. The parts do go through a non-etch cleaner and desmut step as part of the plating process. We are running a test piece at the present time that will go through an etch-cleaner and desmut process. I will let you know how it worked out.
Paul Walsh- Topsfield, Massachusetts
2006
Q, A, or Comment on THIS thread -or- Start a NEW Thread