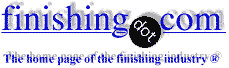
-----
Pitting Problems in Silver Plating
We locally deposit approximately .020" of silver plate, which meets AMS2410, onto a steel part using a cyanide bath. Occasionally we get pitting in the silver plate. The pits are nice and round and appear to go all the way through the plating. Any ideas on what may suddenly cause this to occur?
Patricia Smith- Rome, New York
2006
It is a high probability that it is an air bubble trapped on the surface or a hydrogen gas bubble from the plating process that prevents silver from forming under it. Talk to your supplier about getting and test controlling a wetting agent for your tank. An alternative would be to add mild mechanical agitation of the parts. Air agitation forms carbonates, so it is not a good idea.
James Watts- Navarre, Florida
2006
First of two simultaneous responses --
Hi Patricia,
What is the potassium carbonate level in the bath? If it is too high, pitting can occur. Carbon treatment of the silver bath should be done on a regular basis. I like to filter using carbon cartridges once per month. One carbon cartridge for every 2 hours, change the filter and repeat the process one or two more times. This preventative measure can save you costly down time when you have to do a hot peroxide carbon batch treatment, which by the way may be necessary. It all depends on the chain of organics that are present in the bath (short or long chained). Good Luck!
Process Engineer - Syracuse, New York
2006
Second of two simultaneous responses -- 2006
Hi Patricia,
Below please find some possible causes and solution of pitting on silver deposit:
Possible Causes
1. Low pH
2. Low KCN
3. Poor filtration
4. Organic contamination
5. High additive content
6. Anode polarization
7. Base material defects
8. Improper pre-treatment
Corrective Action
1. Adjust to optimum level
2. Adjust to optimum level
3. Check cartridge and replace if necessary
4. Perform H2O2/Carbon treatment
5. Perform carbon polishing
6. Check voltage to confirm and replace anode plate
7. Check base material
8. Perform water break test to confirm effectiveness of pre-treatment prior to plating
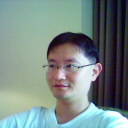
David Shiu
- Singapore
Q, A, or Comment on THIS thread -or- Start a NEW Thread