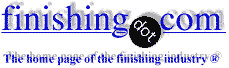
-----
Peeling problem in reel to reel plating
adv.: Supplier of Copper Anodes, Nickel Anodes, Bismuth Metal, & Other Metal Products for Industry & The Arts
Q. Hello,
Hopefully this isn't too much detail; thank you all in advance for reading. We're encountering a very odd nickel adhesion problem that neither myself nor my plating technicians have any explanation for, so I'm hoping someone here can give me a clue as to where to look further. We reel-to-reel plate matte nickel from a pretty typical Watt's bath onto brass, bronze, and copper substrates, and have seen this particular issue on multiple types of base metals. Before nickel plating, our parts go through an alkaline electroclean, a descaler, and a sulfuric acid dip. Chemistries on all baths are checked regularly and are comfortably within control limits, as are temperature, pH, and specific gravity.
Twice in the last few months, we've had an event where 100% of parts were peeling within the nickel deposit. Very consistently, as measured by XRF, about 3-7 microinches of nickel would stay adhered to the work piece, and the nickel above (anywhere from 50 to a few hundred microinches) would peel very easily when subjected to a bend test. We tried the following with no impact on the peeling:
* Verifying connection quality of nickel plating rectifiers
* Swapping out nickel plating rectifiers with our spares
* Treating the nickel bath with peroxide and a carbon filter to remove organics
* Increasing/decreasing nickel plating ASF
* Adding a copper flash and additional acid dip between descaling and nickel plating
* Plating only in the second nickel cell (we have two in-line plating cells fed by a shared bath sump)
* Increasing time in the alkaline electroclean, descaler, and acid dips
We eventually found the direct cause to be our alkaline cleaning bath. Particularly, disabling or drastically reducing the anodic current in the bath prevents parts from peeling in the nickel deposit. After remaking the bath, the issue goes away and we can run at our usual amperage again. The concerning thing is that I've been unable to narrow down what could be happening to this bath that would cause the nickel deposit to behave this way. Typically, we replace our alkaline bath about every 90 days, but twice within a month, it's seemingly overnight gone bad, and I have no way of predicting when it will happen again. Is there a particular type of contaminant that could be at fault here? What could remain on the part even after copper plating a brand new surface onto it (no adhesion issues with that copper), and yet cause the subsequent nickel deposit to flake partway through? Why is the nickel not peeling off entirely instead of leaving a flash behind? If there were intermittent electrical connections, I would expect a more random distribution of thicknesses left behind instead of the very consistent ones we get.
Any help or considerations anyone can provide would be greatly appreciated!
Plating Engineer - Minneapolis, Minnesota
February 3, 2023
Tip: This forum was created to help build camaraderie through sharing tips, opinions, pics & personalities.
The operator & those readers who want that might not engage with anonymous posters.
A. Hi Luke.
I personally find it very hard to believe that the electrocleaning bath is the prime cause of this issue, especially when I have personally seen interrupted current cause such problems, and when interrupted or reverse current is universally accepted as the cause of laminar nickel plating :-)
But assuming the electrocleaning is in fact the problem, the only way I could envision things is that the anodic cleaning is changing the temper/strength/stiffness of the substrate in a way that is causing the inherent nickel stress to become a problem. In that event is it possible to try swapping the bussing to make the electrocleaner cathodic?
But back to the problem actually being in the nickel tank, is there any possibility that a stray current or bipolar effect could be happening during some kind of maintenance?
I don't have any visualization of your contact arrangement, anode arrangement, etc. But any possibility of a dead anode connection at one spot, or a passive anode due to accidental non-sulfurized anode? Quite a puzzler!
Luck & Regards,
Ted Mooney, P.E. RET
Striving to live Aloha
(Ted can offer longterm or instant help)
finishing.com - Pine Beach, New Jersey
A. First go back to what Ted Mooney said, look for electrical problems that vary over time Then passivate a stainless steel panel and plate it in the Hull Cell ⇦ huh? , if the peeled deposit curls as shrunken then you have tensile stress, look at the chloride level, if it peels and curls as in expansion it is compressive stress. The problem could be a combination of polarity variance with stress. If there are two anode circuits in one solution and the voltage is not exactly the same, then the higher anode voltage will passivate the cathode near the lower anode voltage.
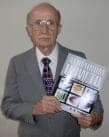
Robert H Probert
Robert H Probert Technical Services

Garner, North Carolina
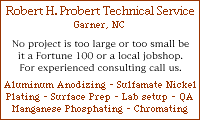
Q. Hi Ted,
I understand your skepticism; I too would find it very hard to believe if I hadn't personally witnessed our tech alternate between recreating and eliminating the failures precisely to the inch on a reel of test parts by simply toggling power on the electrocleaning rectifier. With all else equal, parts that passed through the alkaline bath with no current showed no signs of peeling, while those that had anodic treatment failed a bend test every time. After replacing the bath, we were unable to recreate the failures.
When this anomaly happens again (and hopefully that's never), I will try inverting the polarity of the electroclean step and see if there is any effect.
I wouldn't think that a dead or passive anode would be the cause, since the peeling behavior appears identically if we (essentially) use the same bath with a completely separate set of anodes, but I will try swapping anodes from the "upstream" location in the cell to a more "downstream" one to see if that impacts the thickness of the successful portion of nickel deposit.
P.S. Apologies for simplifying my city to the metro area it's part of. If it's preferred, I'm happy to list the exact city I'm in.
- Maple Grove, Minnesota
February 7, 2023
Ed. note: We were referring to the fact that your real name certainly isn't Luke S. :-)
It's boring ancient history, but there was a time way back when, where people were rather bored of the anonymous 'Shop Problems' in every metal finishing magazine every month. I convinced the publisher of Metal Finishing magazine to try a new approach: problems from people with their real names, company names, and location. Although some people were unwilling to participate so openly, we still had far more postings than we could print, and readers were fascinated by the finishing problems of real people at real shops. Over the decades we learned that it also led to more civil discussions, and a willingness to help as well as being helped; so to the extent possible we prefer people to fully identify themselves :-)
⇩ Related postings, oldest first ⇩
Q. I am a fresh graduate chemical engineer, now working as a plating process engineer. We are running reel to reel plating here and the constant problem that we are facing is the peel-off defect. It happens to our tin and tin-bismuth plating. Our process here is from pre-cleaning to nickel to tin or tin-bismuth or gold.
The problem happens randomly, comes and goes as it likes. We have changed all our pre-cleaning chemicals because the only reason I know is that a poor pre-cleaning can lead to poor plating adhesion due to surface condition.
If anyone knows the probably root cause to this problem, please help.
Thank you!
plating for connectors - Georgetown, Penang, Malaysia
2006
A. May I know whether the peeling is happened between base metal and plated nickel or between plated nickel and tin/tin bismuth/gold.
If between base metal and plated nickel then could be due to poor pretreatment (not enough cleaning and/or microetch of base metal) or nickel bath issue (too high internal stress of nickel deposit, too high current density, etc).
If between plated nickel and tin/tin bismuth/gold then could be due to nickel passivation after nickel plating due to too long rinsing time, de-wetting, etc.
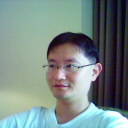
David Shiu
- Singapore
Q. Hi,
Thanks for your reply.
Under the microscope, after the tape test, the exposed surface is very shiny and bright so I assume that is nickel. Tin, to me, looks dull or matte.
We have four cells for nickel plating, running right after another. I have thought of the passivation of nickel surface after plating but each of the 4 nickel plating cells are separated by a rinse station. So the maximum rinsing time between any two cells at one time cannot be more than 10s (even that is a lot considering the speed we are running the terminals). By observation, it is usually 3-4s before entering the next nickel plating cell.
The nickel defect comes in two forms - crack under bent and blistering. I have made sure the pre-cleaning chemicals are changed once a week and I have doubled the concentrations as well to ensure adequate cleaning as some of the parts that come in are very heavy in stamping lubricant oil.
Can the blistering be caused by trapped H2 gas? But how does the gas got trapped in the first place?
Is it true that nickel, once plated, over 2 microns have higher internal stress which will lead to crack under bent?
The problem is still persisting until today. Running out of ideas.
Thanks a lot!
- Georgetown, Penang, Malaysia
Q. How to check if there's a high internal stress in the nickel bath? the pH of our sulphamate bath has yo-yo throughout due to poor air knives which lead to high acid drag-in from acid pickle.
From the observation, nickel is still seen on the terminals' surface after the tape test.
besides monitoring the concentration and density of the pre-cleaning
(alkaline-based) cleaner, what other parameters can we be on the lookout for? I am currently doing weekly dumping and new makeup for the pre-cleaning. I am assuming that is taking care of the poor precleaning issue?
thanks!
- Georgetown, Penang, Malaysia
A. A simple way to verify if internal stress of Ni deposit too high is to plate a hull cell panel (e.g. 2 ampere for 10 mins) and slightly bend it at the high current density area (left hand side of the hull cell panel). Crack and blister occur if nickel stress is high.
Too low Ni bath pH or bath contamination will cause high Ni deposit stress. Add in nickel carbonate to increase pH to ~4.5 and run dummy at low CD (~3 asf) to remove metallic contamination (such as Cu, Fe, Pb) and carbon polishing to remove organic contamination. You may even consider to add in some stress modifier (contact your supplier) into nickel bath to reduce Ni deposit internal stress.
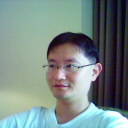
David Shiu
- Singapore
A. The origin of your peeling problem could be a bad electrical contact between the running parts and the current supplier.
Check the voltage of the rectifiers for the nickel cells.
What is the nature of the plating on the tape? If it looks like nickel than the problem is between two nickel cells.
Where is the localisation of the peeling problem : high density areas or all over the strip?
- Lyon, France
Q. The values at the Nickel rectifiers (we have 4 of them) are
V: 4.1 - 4.3 V
A: 22 A
The peeling is everywhere on the strip BUT always confined to only one side of the terminal.
The blister is always on the pilot hole which has a huge surface area compared to the contact point i.e. LCD area.
We are also facing nodules on the terminals. The higher level personnel is saying this is due to the contact gap between the passing terminals and contact rod, which causes sparking. Hence, the only solution we have so far is to tighten the contact guide i.e narrowing the gap between the passing terminals and the contact rods. The problem with this so-called solution is that the nodules always come back RANDOMLY, I might add. How to rectify this problem? We are currently using a three-rod contact where the terminals pass through in between. The machine manufacturer is saying this contact design is state-of-the-art.
- Georgetown, Penang, Malaysia
A. I guess that you are plating stamped parts.
Anyway if you observe sparkles it proves that the contact is bad and you must first treat this problem.
I suggest you to use brass wire brush
⇦ on
eBay or
Amazon [affil link]
for the electrical contact, with a diameter of the fibers close to 0.15 mm so that you don't cause scratches on the strip.
This technique is common in the reel to reel industry.
Good luck!
- Lyon, France
A. Hi E-Jen Teh,
Firstly, you need to check what exactly is observed after the peel off. Is it the base metal or Nickel. Nowhere in the above discussion I see a note on the Base metal you are plating. In case you are using a X-ref Machine to check on the coating thickness, you may also be able to verify this. In case it is a non-ferrous metal, you may need a copper flash treat below the Nickel undercoat.
Plating time and gap is not a constant but a variant that depends on the concentration and make of chemistry and also on the area of the part. By all means logically, Nickel undercoat needs to be as wet to ensure no deactivation and as dry to ensure no excess acid. Mean to say JUST DAMP. This is an art and not science. Most cases this is seen based on results. Please check if you can observe the same during plating.
Crack under bent is more on account of adhesion which is obvious due to improper initial rinsing. Blistering closer to holes is on account of excess oil during stamping which again can be taken care during rinsing. But blistering on flat surface is clearly more to do with the plating chemistry or bath contamination.
The Gentleman from France has rightly answered your question of concern on peel off on only one side of the terminal.
Lastly, hope you are doing only Matte tin. In case it is Bright Tin, please check on the additives as well as the Brighteners batches used versus the rejection data. Can you attribute something on this.
supply chain - Bangalore, India
A. Hi E-Jen Teh,
Peeling is a normal problem and can be easily solved. First you must confirm at which station the peeling occur. My guidelines are as follows:
A) if you see base material after bend test, it is pre- cleaning issues. Check activation and degreasing stations. A good plating line normally come with bi-polar degreasing cell and oil separator.
B) if you see nickel after bend test , you should not assume that it is tin peeling. It may be nickel peeling over nickel as you have more than 1 nickel plating station. For this case it is normally due to cathode contact arcing. Good cathode contact normally come water rinsing. I recommend rotary mercury cathode contact.
C) if you confirm it is tin peeling, it is more likely to due to nickel passivation or cathode contact arcing. I am not sure how far the last nickel station to the tin cell . The passivation risk depend on the substrate surface area and line speed. To minimize the risk , it is best to install an acid activation before the tin station.
I hope all these recommendations helps.
Best regards
- Singapore
July 20, 2013
Q. Hello sir,
I am facing a problem of peel out of tin plating over nickel. My thinking is that nickel is getting passivated so there is no proper adhesion of tin over nickel. Kindly suggest some troubleshooting.
Thanks.
- Bangalore, Karnatka, India
March 20, 2012
Q. I am a Diploma in chemical engineering, now working as a plating process engineer. We are running reel to reel plating here and the constant problem that we are facing is the peel-off defect. It happens to our nickel and tin plating. Our process here is from pre-cleaning to nickel to tin or or gold (base parts are phosphorous copper).
The problem happens randomly, comes and goes as it likes. We have changed all our pre-cleaning chemicals because the only reason I know is that a poor pre-cleaning can lead to poor plating adhesion due to surface condition.
If anyone knows the probably root cause to this problem, please help.
Thank you!
Raghu
- Karanataka, India
June 22, 2012
A. Raghu,
I had a similar issue with sporadic peeling of nickel from the phos bronze in reel-to-reel plating. We tried replacing the pre-treatment chemistry, but the problem would always come back after a short period of time. We found that the cables attaching the rectifier to the electrocleaner cell had become hard (and electrically resistive) over time and were inhibiting current flow. We replaced the cables, cleaned the cathodes, and problem solved!
- Stratford, Connecticut, USA
Q. I have a problem of flaking on Sn/Bi plating, I have checked chemical level and power of the blower. This is not problem.
And now I don't know cause of this problem.
Sn/Bi plating - Thailand
July 2, 2012
Tip: This forum was created to help build camaraderie through sharing tips, opinions, pics & personalities.
The operator & those readers who want that might not engage with anonymous posters.
Q. I am a lead finishing engineer under a semiconductor industry. We are doing rack plating of Tin Matte plating Nickel-plated leads. We are having peel-off problems on our packages but the occurrence of the problem was observed when the rack used was newly stripped with Nitric acid as tin stripper. All pre-treatment chemical, bus bar contact to the rack hooks and bus bar contact to the rectifier were checked and all are in good working condition. Would a newly stripped rack cause the peel-off? In what way will this contribute? How can we eliminate this peel-off problem?
Aiza BuloronSemiconductor - Taguig City, Metro Manila, Philippines
May 19, 2013
A. Hi Aiza,
The best machine to run your products is the continuous strip to strip plating machine. Such machines are made in Holland or USA and utilizes a metal belt from strip transfer. Such technology are more than 30 years old.
I believe that you are using stainless steel as a contact on the rack . As for peeling after the rack are stripped, these are my recommendations:
- check the changes in resistance-- if the resistance is high, it is safer to use the rectifier in constant voltage mode
- alternatively you can change the rack contact to copper alloy
- alternatively you can plate the rack stainless contact with a woods nickel and tin flash before using on production.
Hope these recommendations help.
Best regards
- Singapore
Q. Hi,
I am a Process Engineer and during the summer months especially in June and July we experience a lot of peeling due to humidity. Unfortunately there is not a whole lot we can do about that. I am not sure if it is gold peeling off the nickel or if the nickel is peeling off the base material. Does anyone have any suggestions how to reduce the peeling from humidity. We only experience a high rate of peeling in the summer.
Thanks
Zach
- New York, USA
July 9, 2014
Tip: This forum was created to help build camaraderie through sharing tips, opinions, pics & personalities.
The operator & those readers who want that might not engage with anonymous posters.
A. Hi Zach. I think you must determine which layer is peeling, or more than half of your troubleshooting effort will be wasted :-)
Often it's as simple as looking at the substrate and the peelings. Is the underside of the blisters gold colored (gold peeling from nickel, or silvery (nickel peeling from substrate). If you can't tell visually, it may be because of laminar nickel plating peeling mica-like. Interruptions in current can cause this, especially if for some reason the strip exists the nickel plating tanks mid-process. If you can't tell from visual appearance or other in-house measures, you'll have to send the strip and flakes out for analysis, as it's not productive to change things to try to fix a problem that is unknown.
You probably know this but, so that newbies aren't misled, we need to mention that while the humidity might be causing a loss-of-adhesion process issue, the humidity is not "causing" the plating to peel -- satisfactory plating is a thousand times more robust than that! :-)
Regards,
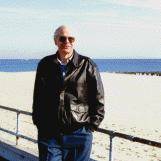
Ted Mooney, P.E.
Striving to live Aloha
(Ted can offer longterm or instant help)
finishing.com - Pine Beach, New Jersey
Nickel is still visible after bright tin plating
Q. I am a plating chemist, Nowadays we are facing the Nickel visible after the Bright tin plating, so please give me the suggestion how can I avoid this problem.
ASHOK KUMAR.Celectronics - Bangalore,Karnataka, India
August 20, 2015
? Hi Ashok. That's a bit vague. How thick is the bright tin plating supposed to be? How thick is it at the thickest point? Is it always absent (or too thin) in the same area? Thanks.
Regards,
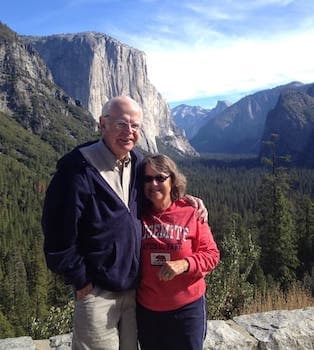
Ted Mooney, P.E. RET
Striving to live Aloha
(Ted can offer longterm or instant help)
finishing.com - Pine Beach, New Jersey
A. The surfactants used in bright tin formulations are impossible to rinse off, you have to go back thru an alkaline soak cleaner, another rinse, a weak 5% sulfuric acid, THEN, the nickel will bond,
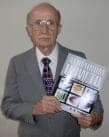
Robert H Probert
Robert H Probert Technical Services

Garner, North Carolina
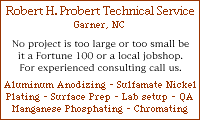
Q, A, or Comment on THIS thread -or- Start a NEW Thread