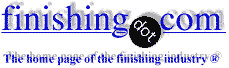
-----
Copper and zinc plating (thermal diffusion)
2006
Hello. I hope that I have enough details to obtain anyones help to my problem...
I work with a process that takes steel and plates it with copper and then with zinc. The steel is then diffused with thermal heating to create brass.
The process problem is that it appears there is a lack of copper plating resulting in a very low and inconsistent copper deposit and a grey / silver appearance of the steel.
In every case of the problem, the total grams of copper is low and the zinc is normal.
I would appreciate any suggestions as to troubleshoot the causes of the low copper deposit.
This is a copper pyro bath used with potassium pyrophosphate to form Cu(P2O7)26- and zinc sulphate in the zinc bath. The copper bath ph is normally 8.6 - 8.8. Sometimes the ph must be controlled with polyphosphoric acid. During these times are when the most notable loss of copper efficiency occurs.
Please note the following:
-The time and temperature needed for diffusion is correct.
-The method of electro plating the copper and the zinc to the wire is the same.
-The current density required for correct plating is observed and followed, but most of the time the amperage needed for the copper must be increased to help maintain the deposit.
-I notice the loss of copper reside in the zinc baths. (zinc contamination?)
-I notice a light blue residue on the copper anode in the bath.
-I notice that the copper anode, after replenishing, can become very cloudy in color after a short amount of time with high amperage.
Also, any details regarding orthophosphates and the method used for measuring the total pyrophosphates in the bath would be much appreciated. (icp
⇦ on
eBay
[affil link]
, titration)
Please ask me for any other details.
plating employee - Dallas, Texas
2006
It sounds as if you are forming an intermetallic compound between the iron and zinc. This happens when you heat treat the steel after it has been plated with copper and zinc. If the copper is too thin, the zinc will just diffuse through it and into the steel. It is possible that the copper may also go into the steel, as I don't know if copper and iron form intermetallics - I suspect not, but it is always an option!
I would suggest you get your copper plating right and then apply the zinc. Heat treating to form the brass can be done at a lower temperature as the reaction between the copper and zinc will be diffusion controlled and this is linked to the process temperature - it will just take longer to get your brass.
Analytical methods for copper pyrophosphate baths can be found in the Canning Handbook, or any other reputable hands-on plating book. It is quite long and will take some time to put it here. Basically, the pyrophosphate is titrated against sodium hydroxide using a mixed indicator of methyl red
⇦ on
eBay &
Amazon [affil link]
and bromocresol green
⇦ on
eBay &
Amazon [affil link]
, but the solution needs to be traeted to get it in the right form.
Copper pyrophosphate can be a difficult solution to use if it is not exactly in balance, so you do need to have it properly analysed.
Another suggestion is that you use a proprietary brass plating solution. These are usually based on cyanide, but they do work.
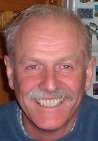
Trevor Crichton
R&D practical scientist
Chesham, Bucks, UK
2007
You should check why the plating efficiency is so low that there's not enough copper deposit on the steel wire surface.Some suggestions below:
1.Check the electrolytic pickling process to verify if the steel wire surface is clean enough.If it's not clean,it should be one of the reason.
2.If your current desity is within the spec. (For brass sequential plating, the current density of pyro copper usually at
9¡«12A/dm2 ,for acid copper is £Š25A/dm2,acid Zinc is£Š35 A/dm2),I suggest you to check your pyro copper solution if it's contaminated by polymer or other metal ions,the contamination can strongly decrease the deposit efficiency .You can use a Hell Cell Test to do the analysis,It's very easy.
3.The PH for Pyro Copper must be between 8.8¡«£É.2,you should take measures to keep it at a normal line.Also the temperature of the pyro copper solution is important......
- Taizhou, Jiangsu, China
Q, A, or Comment on THIS thread -or- Start a NEW Thread