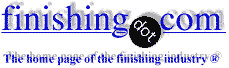
-----
Over 100 Years Ago, How Did They Sponge Plate Antiques On One Side Only?
I restore old horse drawn carriage lamps from the 1800s. Unfortunately, there were no books written on how to build carriage lamps, since the secrets were handed down from father to son. All carriage lamp parts and many plated antiques were sponge plated with silver or nickel on one side only, not dipped in an electro-plating bath that would plate both sides. How did they plate only one side 100 years ago when they only had dry cell batteries and how did they do this before batteries were invented? Modern brush plating of large areas, such as the inside reflectors in carriage lamps, leaves too much to be desired and antiques being restored must be plated on one side only to be authentic. True antique restorers need an answer to these questions and they need a method of sponge plating that is both safe and affordable. Is there a safe and economical method? Thank you.
Paul F. GauvreauCarriage Lamp Restoration. Hudson Copper Products. - Hudson, New Hampshire, USA
2006
First of two simultaneous responses -- 2006
Silver plating before 1840? There are only 3 possible answers:
1.fire silvering (same process as fire gilding,uses alloy of silver and mercury,usualy on only one side of object)
2. immersion plating (with or without zinc contact, combined with lacquer or any other nonconductive coating)
3.paste silvering
- Cerovski vrh Croatia
Second of two simultaneous responses -- 2006
For authenticity, get an older edition of either
ELECTRO-DEPOSITION OF METALS (English translation) by LANGBEIN, GEORGE or
ELECTRO-DEPOSITION: A PRACTICAL TREATISE by WATT, ALEXANDER.
'Stopping off' mixtures of beeswax & rosin were available to prevent deposition on different areas. Placing sheets back to back and sealing the seam also allows one-sided electroplating. Deposition of 'German silver' from a solution containing nickel, copper and zinc may be of interest. Silvering by contact, immersion and friction seems to cover 'sponge plating.'
For accuracy, have the antique parts' compositions analyzed by electron microscopy. You may have German silver (nickel silver) plating. Or maybe, Sheffield silver: silver sheet hammered onto copper, oven heated for improved bonding and then rolled to desired thinness. The ancient Greeks and Romans had similar methods for applying silver foil, as well as immersion plating methods.
- Goleta, California

Rest in peace, Ken. Thank you for your hard work which the finishing world, and we at finishing.com, continue to benefit from.
I am not sure who you have used in the past as a brush electroplating supplier but the process has been used quite often for selective plating of reflective surfaces.
The trick in using the brush plating for this application is to start off with a high gloss finish or a metal that can be plated without etching; such as a copper alloy. The surface is then plated with nickel at low current densities as brush plating solutions do not have organic brighteners. The surface can be left as nickel or plated with silver or gold. Metals such as nickel and silver will tarnish and dull after some time so a clear coat must be added to keep the shine.
- Valencia, California
2006
2006
Just because something was plated one side, doesn't mean it wasn't immersed.
Tank electroplating was developed originally back in the 1850's and is I believe less than 10 years younger than the creation of commercially generated electricity.
Batteries would be of little use because there was no way of charging them, and I believe all battery technology has been developed since the 1880's (please don't nail me down too hard on the dates. )
Brush plating however is an excellent way of re-plating coach lamps if you are using a good quality system.
I have done many of them.
I have never found it necessary to seal silver either.
If it is polished with quality product after plating I have found it to last years.
I have found in a sealed environment the condition of the reflectors deteriorates slower than the clearcoats that may be used to protect them.
The biggest problem with brush plating is that people tend to buy cheap kits from online dealers that offer little support.
Only deal with reputed trade outlets.
If the trade uses it, it should be a decent quality product and the supplier will offer good support.
If it's a 100 dollar internet deal it will be rubbish.
polishing and plating - Belfast, Maine, USA
Q, A, or Comment on THIS thread -or- Start a NEW Thread