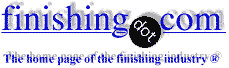
-----
Hot dip galvanizing run-out pots (containers) to recover zinc from kettle failure
2006
Sirs,
There are 20 large vertical cylindrical (not tapered) chambers (10 feet deep) along side and below a very large hot dip galvanizing kettle to collect the zinc in a kettle failure. How should one divide these chambers so that the size of the zinc slabs be small enough to deal with when they freeze? Also will the zinc pull away from the sides of the chambers when the zinc freezes? Should something be put on the walls of the cylindrical chambers so as to make it easier to get the zinc ingots out after freezing? What should be used for the lifting lugs? I have no experience in these chambers and would greatly appreciate any help. Thank You.
Galvanizing Consultant - Hot Springs, South Dakota, USA
Sir,
In my opinion these chambers should be square or rectangular rather than cylindrical. If these are not tapered then they should be made of loosely jointed bricks so that they either collapse during zinc removal or bricks will come out with zinc and can be removed later easily.
To facilitate zinc pulling one should keep vertical hooks in chambers. Bottom of hook should have such a base(usually cross shaped) so that it could be rested in erect position. This crossed base will also hold the zinc mould when zinc is solildified.
Top end of the hook should have an eye formation which can be engaged in a crane to pull out the zinc. Top end should be well above the chamber so that it is not submerged in the zinc.
regards,
pipes - Maharashtra, India
2006
I've successfully used whitewash (lime) as a parting agent in moulds for zinc.
For removal from moulds, we use chain. 12mm link diameter
(nominal 5t SWL) about a metre long, leaving an exposed end outside the mould and with a lifting eye at that end. The other end freezes into the zinc making the only way to get it out re-melting of the zinc.
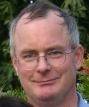
Geoff Crowley
Crithwood Ltd.
Westfield, Scotland, UK
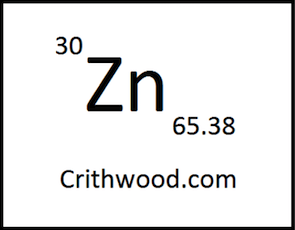
2006
by Kuklik & Kudlacek
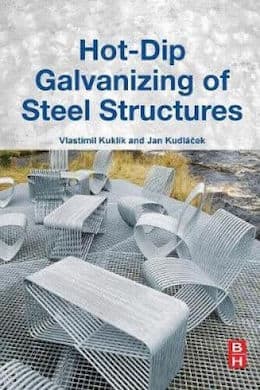
on eBay or Amazon
or AbeBooks
(affil link)
I have seen various chambers for zinc run-outs made with a tapered shape, but if you already have non-tapered chambers, you will probably be able to cut the chambers along the middle in order to separate the zinc. We actually used at one time, the standard 200 liter containers that are seen all over the world for shipping oils, and greases, as chambers for the zinc. After the zinc freezes, we cut them out.
Presently we are preparing tapered chambers, and we are thinking of maintaining them separate to each other by filling with sand.
Kind regards,
Wire Rope Manufacturing - San Miguel, Buenos Aires, Argentina

Q, A, or Comment on THIS thread -or- Start a NEW Thread