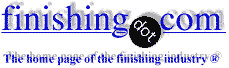
-----
Small pores at the surface SF20T
2006
Recently, our product is facing a serious appearance problem. After the tumbling process, the surface of is full of small pores which look like dented and scratch scrawl.
Therefore, I would like to seek for the help whether any solution/suggestion/root cause here.
Thank you.
precision hardware - Singapore
First of two simultaneous responses --
Lots of questions for you before answer. What is the material you are working with? How Big? What are you doing now and what have you tried? What happens to the part next? Are you using any media or liquids? If they are castings, what process is used to make them?

AF Kenton
retired business owner - Hatboro, Pennsylvania
2006
Second of two simultaneous responses -- 2006
Maybe segregation or corrosion of the free-machining constituents
(lead, sulfide, telluride).
Is this a wet tumbling processing?
SF20T is a free-machining, ferritic stainless steel rarely seen in the USA:
Carbon 0.05% max
Manganese 2.00 max
Phosphorous 0.05 max
Sulfur 0.15 max
Silicon 1.00 max
Chromium 19.00/21.00
Molybdenum 1.50/2.50
Lead 0.10/0.30
Tellurium 0.03 min
Iron -- balance.
- Goleta, California

Rest in peace, Ken. Thank you for your hard work which the finishing world, and we at finishing.com, continue to benefit from.
2006
It surface is round with the diameter about 9mm. It is produce by CNC cutting and after the tumbling process, the part will go to DI wash and visual inspection.
After the CNC cutting, no such problem is found.
During the tumbling process, we use media, compound and DI water for the process. The barrel is coated with rubber.
- Singapore
Hmmmmm. After reviewing you info, I am still leaning toward a problem with your material. If you are using a small media a 3 or 4mm abrasive ceramic media, you should be able to improve the surface finish significantly provided you are using a compatible liquid compound that does not react to the metal.

AF Kenton
retired business owner - Hatboro, Pennsylvania
2006
Q, A, or Comment on THIS thread -or- Start a NEW Thread