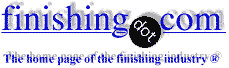
-----
Problems with Powder Coating over Tin Plating
Will Tin Plating survive Powdercoating fluidized bed?
Q. We have a requirement for copper parts to be tin plated per MIL-T-10727, Ty I followed by application of epoxy powdercoat insulation using the fluid bed process, with masked areas where the tin should remain exposed.
The customer's process spec calls for the parts to be heated to 400 °F for the application of the epoxy insulation. We have a concern for the tin plating being able to withstand that temperature. What is the maximum sustainable temperature that a tin plated part could withstand? How about electroless nickel, cold that withstand the 400 °F?
- Baltimore Maryland
April 29, 2024
A. Hi David. Tin plating and solder is sometimes reflowed at 500 °F so I think it will withstand the 400 °F preheating. However, read below for a report of problems even at 375 °F
I guess I would suggest heating sample parts to this temperature range and seeing what results you get. But even if you see no visible change, I don't think you can guarantee that the epoxy powdercoat will adhere well, only that the tin will remain okay.
Luck & Regards,
Ted Mooney, P.E. RET
Striving to live Aloha
(Ted can offer longterm or instant help)
finishing.com - Pine Beach, New Jersey
⇩ Related postings, oldest first ⇩
for Shops & Engineers

avail from eBay, AbeBooks, or Amazon

avail from eBay, AbeBooks, or Amazon
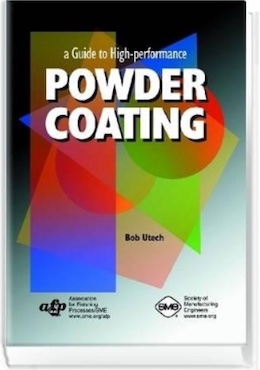
avail from eBay, AbeBooks, or Amazon
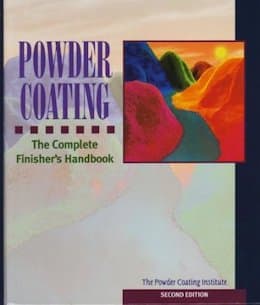
avail from eBay, AbeBooks, or Amazon
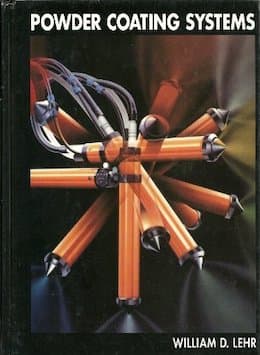
avail from eBay, AbeBooks, or Amazon
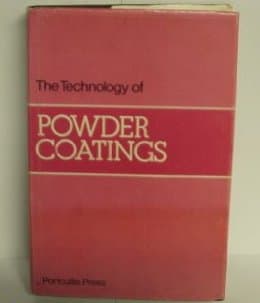
avail from AbeBooks, or Amazon
avail from AbeBooks, or Amazon
(as an Amazon Associate & eBay Partner, we earn from qualifying purchases)
Q. As a commercial plating shop, it is not unusual for us to plate tin over copper bus bars. In certain instances, there are problems with powder coat adhesion. We have seen varying degrees of (apparent) tin oxidation on the powder coated components. It is reported that they bake the parts at 375 deg F. The customer is frustrated, the powder coater is pointing his finger at us and we are stuck in the middle - trying to come up with answers. How suitable a surface is tin for powder coat? What can be done to help insure success and eliminate adhesion problems?
Murray RitlandCommercial Plater - Minneapolis, Minnesota, USA
2006
A. How fast is the temperature increasing by starting the powder coating burning process? Also, do you use an adhesion agent after tin plating? Are the parts clean prior to the powder coating and do the workers wear gloves while racking the parts? When you write that you have adhesion problems, could you figure out where it comes from (check also the plating process)?
Regards,
- Mexico City, Mexico
Q. We have been powdercoating over tin plating for the past several months and occasionally have an outgassing type event occurring on the parts which leaves volcano type bubbles on the surface. Parts are aluminum plated in matte tin using the Alstan 88 process.
The big difference I see between parts that are good vs. bad, would be the base layer. Good parts use a copper cyanide base where the parts that typically cause issues use a bronze type base. Any ideas why one would net better results or is that just a coincidence?
Ryan CarterEngineer - Cincinnati, Ohio United States
November 3, 2017
A. I'm not too savvy on why one material is yielding more out-gassing than the other, but I have found that most of our out-gassing issues are with cast parts, aluminum or iron. We use a prebake process that consists of full cure temperature and time, then apply the powder coat while it is still hot. This way, the part is out gassed before the powder coat is applied and the finished product is smooth as intended. Although, I wouldn't trust all of our coaters to "coat it hot". It's an art form in itself to guess the correct powder thickness when the powder is melting as you apply it. The heat skyrockets the transfer efficiency and you could end up at 15 mils before you know it. Additionally, if more than one coat of powder is in the process, like using a primer or needing a clear coat, only the first coat needs to be coated hot.
Kayla Fagenproduction manager - Cedar Rapids, Iowa, USA
Q, A, or Comment on THIS thread -or- Start a NEW Thread