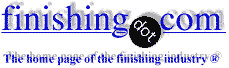
-----
Zinc plating plus powder coating instead of hot dip galvanising
Q. Hello , I'm Ansar working with Enercon India and I would like to know the possibility of reducing corrosion of MS parts by Zn electroplating followed by Powder coating instead of hot dip galvanising? is this process more economic?
Sheik Ansarwind energy converters - Daman, Union Territory, India
2006
A. Powder coating on a phosphatized surface would probably be the least expensive approach, then galvanizing, then plating plus powder coating, but it's hard to say without getting quotes on real parts.
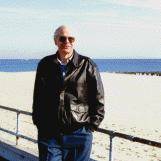
Ted Mooney, P.E.
Striving to live Aloha
(Ted can offer longterm or instant help)
finishing.com - Pine Beach, New Jersey
2006
A. We are in all these businesses, (galv, plating and PC), so have a good feel for the economics.
Zn plate + PC is generally more expensive than Galv only.
There's the difference in colour to consider, but that's not an economics question.
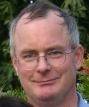
Geoff Crowley
Crithwood Ltd.
Westfield, Scotland, UK
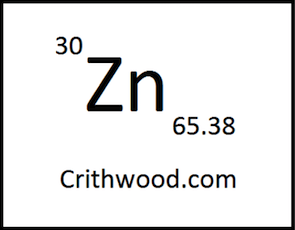
2006
A. Dear Ansar,
I would not advise a move away from Hot Dip Galv to zinc + powder coat unless you evaluate how they both look after a month under rigorous testing in an environmental chamber.
Epoxy powder coats have little UV resistance, the other hybrids are slightly better; but there are bonding issues and all sorts of hassles with getting Powder coating to bond over strongly chromated surfaces the kind you encounter over zinc plating.
Also once out in the sun thermal wear and tear will finish it off. Look around at television antenna poles anywhere in India, some of these are zinc + powder coat, and have nothing left on them after a year or two in our amazing Indian weather that provides summer-monsoon-winter all in one day.
I would also suggest that you compare a Zinc Iron Plating with Hot Dip Galv whilst you are about it. Also Zinc plating with a topcoat of zinc-aluminium rich paint may be a better option. Does your company have Hex Chrome issues?
Best wishes,
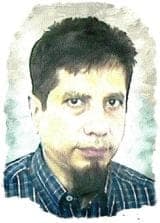
Khozem Vahaanwala
Saify Ind

Bengaluru, Karnataka, India
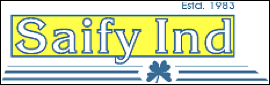
A. Khozem points out that epoxy powdercoating will not last in sunlight, and mentions hybrids as more suitable.
But the more common powder to use for external work is polyester which is very UV stable, even for climates like India.
It can be applied over galvanizing (for corrosion protection) but the pretreatment route chosen is critical to success.
Polyester powdercoating will last for decades in sunny climates.
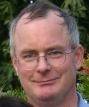
Geoff Crowley
Crithwood Ltd.
Westfield, Scotland, UK
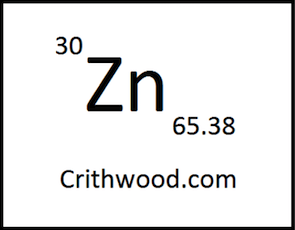
2006
Multiple threads merged: please forgive chronology errors and repetition 🙂
Polyester Powder Coating After Zinc Plating
Q. We have some Steel structures that are built using hot rolled high strength Steel. For corrosion prevention we plan to Zinc plate them then add a layer of polyester powder coat. Though there is an ASTM standard for the Zinc plating, there is no such thing for the powder coating. Does anybody know of an industry standard or procedure for that kind of application?
Thanks,
- Poway, California, USA
2006
A. You mention steel structures, which seems to imply substantial pieces of steel, but then state that you intend to zinc plate.
Electroplating isn't commonly used for large structures in hot rolled steel.
Hot dip galvanizing would be more common for HR structural Steel, and this can be followed by powdercoating.
The standards applicable vary from country to country. One such is ISO 13438 (prev BS 6497).
Zinc plating as a corrosion protection is limited by the thickness of the zinc layer. Its application is usually limited by the size of the item.
Hot Dip galv is typically 10-15 times thicker that plating, and last correspondingly longer. Neither are easy to powdercoat, the pretreatment between zinc coating and powdercoating being the critical point. Either a chromate or a zinc phosphate pretreatment system of 8-12 stages is required. But if you do get it done this way you can expect a competent coater to offer a guarantee of 15-25 years, depending on the installation location.
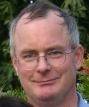
Geoff Crowley
Crithwood Ltd.
Westfield, Scotland, UK
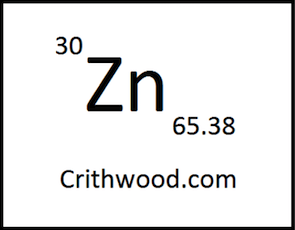
2006
A. Hi again. Zinc plating plus powder coating is a fine idea when part of a component must have a plated surface and part of it must have a decorative powder coated surface -- say a machine screw which requires a decorative painted head.
But paint/powder adhesion onto a chromated zinc surface can be questionable especially in these days of highly proprietary trivalent chromates and topcoats. I think I'd only accept powder coating on top of zinc plating from a shop which does the whole finishing job.
Regards,
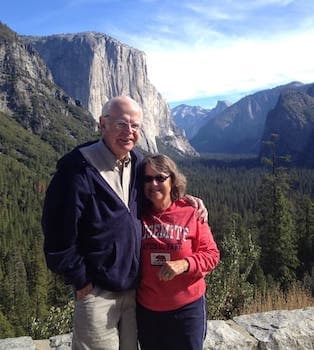
Ted Mooney, P.E. RET
Striving to live Aloha
(Ted can offer longterm or instant help)
finishing.com - Pine Beach, New Jersey
Q, A, or Comment on THIS thread -or- Start a NEW Thread