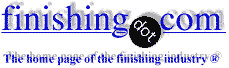
-----
Anodized parts fail salt spray test if dyed

Q. We are doing Type I & Type II Class 2 anodizing using Black dye as per MIL-A-8625 / MIL-PRF-8625
[⇦ this spec on DLA] on AA2024 T3 sheets. The specimens are failing in Salt Spray test as per ASTM B117 after 48-50 hrs. instead of 336 hrs.
The Class 1 (Non-dyed) specimens are passing the salt spray test.
1. What can be the reason? Shall we use different parameter for class 2 than class 1?
2. If dye may not be suitable, can any one suggest the dye specification which can withstand 336 hrs salt spray test?
Manufacturing - Mumbai, India
2006
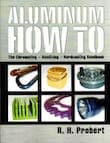
Aluminum How-To
"Chromating - Anodizing - Hardcoating"
by Robert Probert
Also available in Spanish
You'll love this book. Finishing.com has sold almost a thousand copies without a single return request :-)
Treatment &
Finishing of
Aluminium and
Its Alloys"
by Wernick, Pinner
& Sheasby
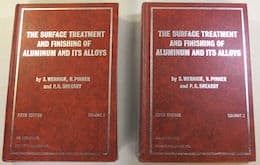
on eBay or Amazon
or AbeBooks
(affil link)
A. The dye has nothing to do with it. Anodize at a proper temperature, a proper voltage/amperage and long enough to get an adequate thickness to pass more than the minimum weight loss criteria and finally, seal it with a cobalt or nickel seal-HOT not this room temperature stuff. If you have proper cleaning, etch desmut deoxidize rinses, then it should pass.
Finally, are you using parts or coupons for the salt spray.
- Navarre, Florida
A. The most likely cause of failure has been mentioned. You lack proper sealing after dye coloring. Check the sealing process for temperature and time.
Kas Amadi- Dayton, Ohio
Q, A, or Comment on THIS thread -or- Start a NEW Thread