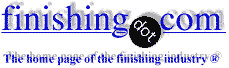
-----
Chrome Plate Adhesion Tests, Chisel Test Interpretation
I am performing a destructive QA evaluation of a critical helicopter drive part. This part incorporates a chrome plated (0.006" nominal thickness) outer diameter: the chrome plate acts as a seal journal and anti-fretting surface. The substrate is shot-peened 9310 steel heat treated to 180 ksi max (Rc40). The chrome is ordinary hard chrome, BAC5907 CL 2 (no special pre-plate cleaning like sulfuric/HF is specified).
In the interest of diligence, I am trying to evaluate the adhesion of the chrome. The part is round and thick, and I wanted to perform other evaluations after I strip the chrome, so I selected a chisel test instead of a bend test (I would have to machine a thin strip for that). I filed a square groove through the chrome with a small diamond file. I made a tool steel chisel (45 degree angle tip) and struck it a with 21 oz plastic non-rebound hammer, placing the tip of the chisel in the groove.
The chrome popped off in 3/16 inch diameter pieces. There is no transitional fracture at an angle through the chrome. The edge of the chrome is square. I cannot pick any additional chrome off at the edge.
Depending on who I talk to or the reference I use, this is good, or this is bad. One source told me it should fracture the chrome, not chip it off at the interface. Another said chipping is allowed at the interface as long as it does not exceed 4mm, and that he would never use a chisel test on such soft steel, or without special pre-plate adhesion enhancement treatment. One reference says this is bad, while another says it is ok as long as the piece is less than 4mm and I cannot pick any additional pieces off with a probe.
So, my question is, in the world of hard chrome plating, how much delamination should be expected, provided the plating is done properly, not using sulfuric/HF or similar adhesion promoters.
Also, what should I expect if I ever do a bend test? I am inclined to think the plating in the radius of the bend will crack and pop off, forcing me to do a lot of probing at the edge. Or does the chrome merely crack into very fine pieces that remain adhered to the steel?
Aircraft MRO & Operator, M&P Engr. - Portland, OR, USA
2006
2006
Normally, you would use whatever test is called ot in the plating spec or in the OEM's overhaul/standard practice manuals.
I do not remember the chisel test called out for chrome by any of the 5 major engine manufacturers, specs.
The problem with your test is that it is not quantitative in the amount of force that is applied. Chrome is relatively brittle, so if you apply enough force, it will chip. How much is dependent on the size of the chisel and the amount of force applied. The fact that it did not peel would possibly be good enough.
- Navarre, Florida
Aircraft industry is perhaps the most stringent and rigid. It should be. I understand that being a destructive test maybe you just want to learn something about chrome plating, but in any case, for the processing of a new or repaired part you have to perform any tests that are covered in the specification and interpret them by the book. You are not supposed to modify them, alter them or select other ways of testing. Anyone's opinion in this case is just academic.
Guillermo MarrufoMonterrey, NL, Mexico
2006
First of two simultaneous responses --
...while another says it is ok as long as the piece is less than
4mm and I cannot pick any additional pieces off with a probe."
Per the requirements of BAC 5709, this response is correct. The goal is to have a fracture zone that contains residual chrome, which means the chrome fracture was cohesive rather than adhesive (at the chrome-steel interface). The picking at the edges of the fracture zone was added to the spec to allow for "marginal" conditions to be accepted. We are looking at tightening the requirements in some cases
(shortening the 4 mm zone, mandating some residual chrome in the fracture area, etc).
Boeing Materials & Process Technology - Renton, Washington, USA
2006
Second of two simultaneous responses --
Jim,
BAC 5709 is a Boeing specification. The chisel test you mention has a BSS which describes both the test and interpretation. I would suggest you either talk to Boeing or, if they are not your customer, the customer and ask for a copy of the test method. Much better than getting an open forum to interpret your results.
Aerospace - Yeovil, Somerset, UK
2006
Q, A, or Comment on THIS thread -or- Start a NEW Thread