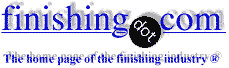
-----
What's a supplier to do
I am a mechanical engineer with an antenna supplier for the wireless industry. We currently use a Zinc-Chromate coating on all of our standard mounting kits and will have to change over to a non-hexavalent chromium finish as we supply antennas all over the world. We have been lead down the path of Trivalent Chromium with a clear coat. I have run sample parts through 168 hour salt spray with very good results, however I am trying to obtain the actual plating specification required on our drawings to enable us to procure parts from various vendors. Can you please help with this spec.
Wayne PeavyEMS Wireless Inc. - Norcross, Georgia, USA
2006
2006
I WANT TO HOW CAN TRIVALENT CHROME PLATING TO SPECIFIED FOR EXAMPLE Fe/Zn/8c FOR HEXAVALENT CHROME PLATING YELLOW.
I ALSO WANT TO KNOW UNDER WHAT STANDARDS(INTERNATIONAL) IT IS GOING FALL UNDER SUCH AS EN12329
[BS EN 12329].
AUTOMOTIVE - Bangalore, Karnataka, India
This question has become quite repetitive because so many people are concerned about it. So, for a 2nd opinion, please patiently apply the search engine and you will see many very similar threads. But to summarize in a few sentences--
Until the last few years trivalent conversion coatings were greatly inferior to hexavalent coatings in corrosion resistance. The gap has been greatly reduced, and in the opinion of some, closed with today's technology. But that technology is all proprietary and has followed a number of different routes, including thick layer trivalent chromates and thin layer trivalent chromates with or without sealants. If your only requirement is corrosion resistance, it is pretty simple: just specify the same salt spray resistance you always have specified, and note that the coating must be free of hexavalent chromate and RoHS and EoLV compliant. Then the shop can use whatever conversion coating technology they have adopted.
But if the parts require good conductivity, or will be powder coated, or must meet aesthetic requirements, or other requirements, things do become much dicier because the various shops will be using differing proprietary technologies and some may not be suited for some applications.
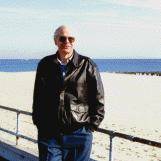
Ted Mooney, P.E.
Striving to live Aloha
(Ted can offer longterm or instant help)
finishing.com - Pine Beach, New Jersey
2006
Q, A, or Comment on THIS thread -or- Start a NEW Thread