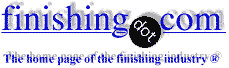
-----
Boric-Sulfuric acid anodizing BAC5632 Issues and Answers
Q. Hello everyone, I'm getting big pits on big panels surface on boric-sulfuric acid. First the part
After that the other side was running and when the panel was removed we looked the first half full of big pits and the second one clean of them.
Running conditions.
First running: 18 volts, 20 min ramping 5 v each min starting at 0 v
Second running; 18 volts, 20 min ramping 5 v per min starting at 5 v and higher air agitation
Chemical engineer - Los Angeles California
October 8, 2021
⇩ Related postings, oldest first ⇩
Q. We are having problems with our Boric-Sulfuric Anodize tank. We are getting some bad pitting and what looks like corrosion on our parts. This is the 2nd time this has happened in 3 weeks. The first time we suspected contamination of the bath, but now we have a brand new bath and it has my mind boggled. Please help me with any advice as to what our problem could be.
Tony SchmaltzPlating Shop - Seattle, Washington USA
2005
Q. Please send your answer for the problems of pitting in boric-sulfuric anodize process.
Kario Michael- Lod, Israel
2006
Q. We are having problems with our Boric-Sulfuric Anodize tank. We are getting some bad pitting and what looks like corrosion on our parts. I see same question but there was no answer.
Please, please, let me know why those pitting(or burning?) are generated and how to resolve this problem.
Aluminum treatment - South Korea
2006
2006
Hello, I.S. There are several other letters on-line here about boric-sulfuric anodize, and several of them mention that the process is Boeing BAC5632. Are you following BAC5632?
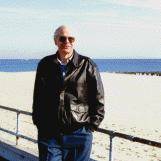
Ted Mooney, P.E.
Striving to live Aloha
(Ted can offer longterm or instant help)
finishing.com - Pine Beach, New Jersey
Q. Yes, we perform Boric-Sulfuric Anodize in accordance with BAC5632 for Boeing parts.
I.S. HwangAluminum treatment - South Korea
2006
A. I.S.
It is a long shot but I would check for chloride contamination, particularly if the pitting coincides with a bath make-up or new solution (container) addition.
- Colorado Springs, Colorado
2006
Q. Dear sir, we do Boric & sulfuric acid anodizing.
After the process we get pits/ black pore-like things.
Please can you throw light on this?
Thanking you,
Regards,
- Bangalore, Karnataka, India
July 9, 2013
A. We really need more information on your process parameters in order to come up with an insightful response but I have found that when I have had pitting problems they usually come from either too weak of a deox/desmut solution or too much time in the deox/desmut solution.
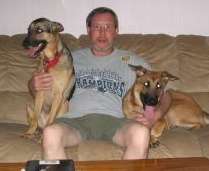
Tim Hamlett, CEF
- West Palm Beach, Florida, USA
July 11, 2013
A. I think your problem is not related to anodizing. I had had same problem 4-5 month ago. I noticed source of problem was extrusion and storage conditions. Long time storage profiles's surface getting corroded. After caustic bath, these pits reveal and after anodizing you can see it. Solution: profiles not to wait too long time; avoid humidity storage; and also I wonder do you see these pits for bright profiles after anodizing? I don't see so far... because these profiles not treated with caustic.
Alaattin Tuna- Sakarya, Turkey
July 25, 2013
Boric Sulfuric Acid Anodize tank analyses
Q. I am looking for a titration procedure with factor for boric acid and sulfuric acid. I am having difficulty getting the correct concentration for each and I've tried three different methods
Christy Sanchezlab tech - Savannah, Georgia
May 10, 2016
![]() |
A. Christy, it would be helpful to know what 3 methods you have tried, so that your follow up reply is not I tried that and it does not work. - Navarre, FL May 10, 2016 You can easily determine total acidity via a titration with 0.1N NaOH ⇦ on eBay or Amazon [affil link] to a phenolphthalein endpoint. I imagine that you could isolate the boric by titration to a method orange endpoint with the same solution. Plenty of stirring and slow the titrant. ![]() Dave Wichern Consultant - The Bronx, New York May 10, 2016 |
Thank you for all your help. Yes, I am using a Boeing spec for the titration procedure. The Procedure No. I used is B-281A of which uses 1.0 N NaOH as the titrant. I have started over and redone the procedure and finally got my end results in reason from what they were. I appreciate all the advice on this and will utilize it to my advantage. Thank you!
- Savannah, Georgia
May 11, 2016
Pitting under the rack marks in Boric-Sulfuric anodizing
Q. We are experiencing pitting under the rack marks. This is a boric/ sulfuric process. It is only occurring on this part configuration. Does anybody have any suggestions as to what might cause this?
metal finishing - Holdenville, Oklahoma U.S.A.
August 22, 2018
A. Such big electrical contact, maybe acid residual when drying leads to these pits.
Tingqiang WangZhejiang XIZI Aviation Industry Co., Ltd - Hangzhou, China
August 24, 2018
A. Hi. The pictures might be deceiving me but those pits look so deep & severe that in my limited experience it doesn't seem likely they would happen in a short time solely from chemical reaction. I get the feeling something electrical is happening like a momentary short circuit, or dirty contacts not carrying any current during ramp-up then suddenly breaking through at higher voltage.
Regards,
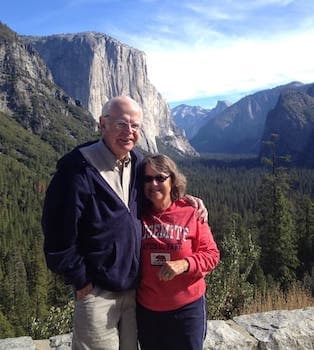
Ted Mooney, P.E. RET
Striving to live Aloha
(Ted can offer longterm or instant help)
finishing.com - Pine Beach, New Jersey
August 2018
A. The cause could be a poor electrical contact, probably the surface is uneven so only a small area is doing the electrical contact and that produces the burns.
Yohands Rey- Chihuahua, Mexico
August 24, 2018
A. Brandon
What does the surface of the contact plate look like? Does it have the same pitting?
Have you tried unracking the parts prior to seal to see if the problem originates in the anodize bath? If you have residual acid trapped between the part and contact point, elevated temperatures might cause the pitting you are experiencing.
- Green Mountain Falls, Colorado
August 27, 2018
A. I don't suppose this appearance is "pitting" ... pitting is completely different. We can say "stain" as described. My advice: you can change rack design, or degreasing and neutralize duration can be much more, like 5 min. Because maybe profile's surface was dirty from normal level so in that joint area had effected as we see picture.
alaattin tuna- Turkey,sakarya
August 29, 2018
August 2018
Hi Alaattin. Agreed that this is not what we usually call a "pitting defect", but it sure looks to me like quite deep etched craters, not a surface stain. Pictures can be deceiving: one of us sees stains, but one of us sees deep corroded indentations :-)
Regards,
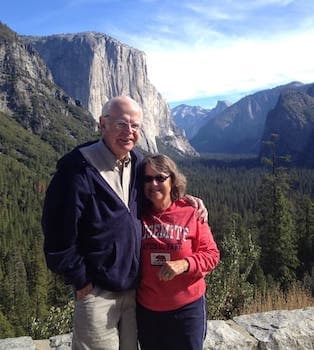
Ted Mooney, P.E. RET
Striving to live Aloha
(Ted can offer longterm or instant help)
finishing.com - Pine Beach, New Jersey
A. Hi Ted, yes, I agree with you about "point of view" issue for some problems like this one ... but I think solution of this problem should be "one". In this situation I follow this way:
1- How often does this problem occur? for example, every rack or some racks ... also does the same problem occur on different profiles?
2- one of the key words in this situation is "survey". Is this problem emerging before/after anodizing or etching ... also sealing.
So we can collect and filter all the results and diagnose; after that, of course, treatment.
- sakarya,TURKEY
September 4, 2018
A. We have had the same problem as Mr. Boyd, however, not just on the contact areas. The deep pits in Mr. Boyd's photos are all too familiar to me while using boric/sulfuric anodize. I have never been able to nail down a cause. My tank will produce perfect parts for three months straight - then, without warning, an entire lot of parts will exhibit those monster-pits. The pits will appear at contact points AND at random areas all over the anodized parts. The pits are quite deep and generally will cause the entire lot of parts to be scrapped. Our parts are racked on clean and deoxidized racks and the contact points are as small as possible to reduce the likelihood of trapped solution. Pre-clean includes a deionized water rinse after deox.
Steven HaubeilAerospace - Wantagh, New York USA
September 19, 2018
November 16, 2018
(to help readers better understand the Q&A's)
To avoid confusing newcomers, please note that we are speaking of Boeing BAC5632 boric-sulfuric anodizing on this page. Boric acid anodizing is actually a very different process used for applications like electrolytic capacitors.
Q. What is needed to start up a boric acid anodizing tank. Does it need to be chilled or any type of special liner like a lead liner. Going to be using it per the Boeing Spec BAC5632.
Roger Leon- tustin California
A. Assuming you mean Boric acid-Sulfuric acid anodizing, as that's what the referenced spec covers, there is no special liner: we have ours in a poly tank.
There are specific cathodes that must be used, which is specified in the spec & subsequent PSD's.
You will need a heater and a chiller, as it has a tight temperature requirement.
- Seattle, Washington, USA
November 16, 2018
Q. Fauna Tester, I appreciate your response. Is the poly tank the gray color that is more resistant to chemical?
Roger leon [returning]- Tustin California
November 16, 2018
A. It is standard white polypropylene.
Fauna Tester- Seattle, Washington, USA
November 19, 2018
![]() |
A. However, I just received the latest addition of Products Finishing, which rates polypropylene the worst. - Seattle, Washington, USA November 19, 2018 A. Thanks Fauna. (Readers: that article can be found at For a number of years I was 'the plating shop guy' for a fire investigation service for the insurance companies, so I visited many plating shops which had suffered fires and saw the causes and the results. The overwhelming majority were caused by the use of electric heaters in polypropylene tanks. The first rule should be: don't use electric heaters in polypropylene tanks unless 'armed to the teeth' (at least two or more separate safety devices). There are fire-resistant grades of polypropylene (infused with bromine fire retardants) but, besides adding a lot of cost, they can leach the bromine chemicals into the process. We used them on one process line and the bromine was a bit worrisome but turned out okay for most of the tanks ... but the Electroless Nickel tank which was built of fire-resistant polypropylene had to be simply scrapped. Every material has its advantages & disadvantages and I personally feel that if you don't use electric heaters, or you use them only with the greatest care and double safeties, you eliminate 95% of the problem of flammable polypropylene tanks ... and that's a darn good start in any undertaking in my book. And I certainly saw many leaking steel and lined steel tanks in my career. A point which ought to be inferred from the article is that only experienced plating tank designers should build plating tanks. In my career I designed many thousands of plating tanks and although I do not agree with the author of that article that you need automated welding, you do need competent engineers, broad experience with plating tanks, and skilled craftspersons regardless of the material of construction of the tanks. Regards, ![]() Ted Mooney, P.E. RET Striving to live Aloha (Ted can offer longterm or instant help) finishing.com - Pine Beach, New Jersey November 2018 |
Copper contamination of boric-sulfuric anodize process
Q. Hello,
I am trying to identify any impact on parts caused by increasing dissolved copper content in a boric-sulfuric acid anodising tank. Our tank is currently around 200 ppm, but I wanted to know if there was any impact if the concentration was higher (say around 300 ppm). Any information or guidance would be much appreciated.
- Sydney, NSW, Australia
December 2, 2018
A. The spec states 237 ppm max, so I wouldn't recommend it.
Fauna Tester- Seattle, Washington, USA
December 4, 2018
A. If you run the 2000's, there is nothing you can do to prevent copper, it plates out when the current is on, it partially re-dissolves when the current is off, so take the sample shortly after starting the current on; it does not hurt anything.
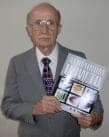
Robert H Probert
Robert H Probert Technical Services

Garner, North Carolina
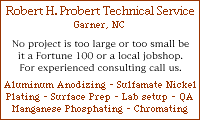
December 5, 2018
A. Copper in anodizing baths tends to lower salt spray resistance.
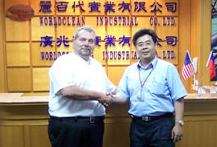
Drew Nosti, CEF
Anodize USA

Ladson, South Carolina
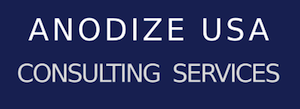
January 17, 2019
A. It is possible to remove copper from this anodize bath by electrolysis with a high surface area cathode. This is preferable to decanting or dumping a portion of the bath in order to control copper.
Lyle Kirmanconsultant - Cleveland Heights, Ohio
January 20, 2019
February 14, 2019

I am working on the implementatation of the boric-sulfuric anodizing system, then it is doubtful if it is strictly necessary the addition of an organic compound such as benzoic acid or sodium benzoate in order to inhibit the biocontamination.
That is to say, according to the norm, it is "possible" to add said compound, but is it really common for biocontamination in these types of anodizing tanks or can the addition of such an additive be dispensed with?
Thank you so much, I waiting for your answers
Q. Estoy trabajando sobre la implantación del sistema de anodizado con bórico-sulfúrico, luego cabe la duda de si es estrictamente necesario la adición de un compuesto orgánico tal como Ácido benzoico o benzoato de sodio a fin de inhibir la biocontaminación.
Es decir, según norma se "puede" añadir dicho compuesto, pero ¿realmente es común la biocontaminación en estos tipos de tanques de anodizado o se puede prescindir de la adicción de tal aditivo?
Muchas gracias, espero sus respuestas
- Huelva, España
Q. Hello,
I'm looking for a way to analyze for copper and NaCl in a Boric Sulfuric anodizing Tank.
I must keep the copper to 235 ppm and the NaCl to .1 g/l
Thanks in advance,
Edwards Interiors - Rincon, Georgia
July 16, 2019
Q. Hello,
I was wondering if anyone knew of a way to analyze NaCl in a Boric/Sulfuric anodizing bath. I must not exceed 0.1 g/l of NaCl.
Thanks,
- Rincon, Georgia
October 30, 2019
October 2019
Hi Micheline. While we're waiting and hoping for a response, I see that you have reframed it in more limited fashion since last time. Please share what if anything you have learned about analyzing for copper in this bath. Thanks!
Regards,
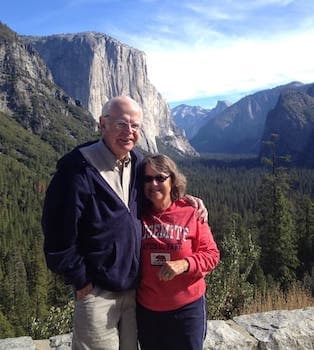
Ted Mooney, P.E. RET
Striving to live Aloha
(Ted can offer longterm or instant help)
finishing.com - Pine Beach, New Jersey
October 31, 2019
Ted,
I have not found a great solution for copper. I do like to do everything in house if it is cost effective. I found a lab to do it for now but they say that they cannot do NaCl.
Micheline
Edwards Interiors - Rincon, Georgia USA
A. Hi, Micheline
NaCl in aqueous solution would be present as Na+ and Cl-, so it might be better to ask to analyse for those ions (as NaCl itself would technically not be present).
Something like atomic absorption spectroscopy
⇦ on
eBay
or
Amazon [affil link] could probably do it. Salts can be pretty harsh on some forms of mass spectrometers and HPLC, so that may be why the lab can't do it.
- Katikati, New Zealand
November 6, 2019
Thank you so much for your response. I will work hard to get a solution. It may involve buying our own equipment
- Georgia, USA
November 13, 2019
Q. Can you please help me out. I want to see what is needed to start a boric acid sulfuric anodizing tank. Per MIL-A-8625 / MIL-PRF-8625 [⇦ this spec on DLA] type IC. If you would please help me I would appreciate it. Thank you in advance for your help.
Roger leon [returning]- Tustin California
July 28, 2020
A. Hi. Fauna previously answered you that a standard white polypropylene tank would be okay, and I think he's right. He also said that Boeing Spec BAC5632 requires very tight temperature control with both heating and cooling. If you are not working to BAC5632 I'm not really sure that MIL-A-8625-1C is truly very meaningful because it says you can only use it if the procuring activity agrees, and it doesn't specify boric-sulfuric anyway, just mineral acid or mixed mineral-organic acid; I think Airbus might use neither chromic, nor boric-sulfuric, but phosphoric acid for similar applications.
There may be shops who do MIL-A-8625-1C boric-sulfuric without adhering to BAC5632 but I don't know, and I don't know of a good way of figuring out ideal heating, cooling, and cathode material, concentrations, etc. without either simply following BAC5632 or being lucky enough that such a shop responds :-)
Sorry, & Regards,
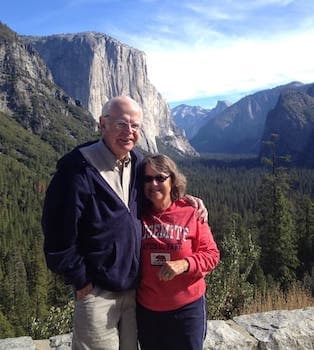
Ted Mooney, P.E. RET
Striving to live Aloha
(Ted can offer longterm or instant help)
finishing.com - Pine Beach, New Jersey
July 2020
A. I believe that purchasing the most current copy of BAC5632 would behoove you. It is the governing spec for Boric Sulfuric Anodizing.
Taylor Clarke- Minden, Nevada
July 28, 2020
Q, A, or Comment on THIS thread -or- Start a NEW Thread