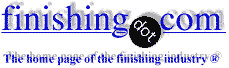
-----
Nickel electroforming coating hardness
2006
We are not getting hardness less than 150 on Vickers scale.What is the required condition of the sulphamate bath.
I have worked with the following bath condition
cd 3.5A
temp 50degree C
air agitation
cathode movement
S Nickel anode
Forging - Mysore, Karnataka, India
You probably have unwanted drag in material or breakdown products or an excess of SNAP A/M (or equivalent). I would do a good carbon treatment, check the bath for all parameters and try again. Should work if your pH is 4.0 + or - 0.1
James Watts- Navarre, Florida
2006
You didn't mention the pH but anyway a sulfamate bath does not give you much chance to move it or raise the temp. Perhaps reducing you current to 1-2.5 A/dm2. Also important is to control impurities specially hex-chrome, sulphate and ammonia. Check your hardness indenter shape and force, it might be misleading you.
Guillermo MarrufoMonterrey, NL, Mexico
2006
2006
Dear Mr. Rao,
What is the hardness required in nickel Electroforming?
To get minimum hardness avoid chloride in sulphamate bath . S nickel will dissolutes to 1-3 gms of Nickel chloride. Also at less cd and low temperature without any additive addition you can get the low hardness. controlling chloride in the bath is very important.
- Maharashtra
I would not expect to get any nickel hardness less than 150Hv, so I reckon the bath is doing what is is designed to do. What hardness do you want?
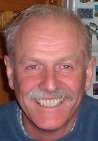
Trevor Crichton
R&D practical scientist
Chesham, Bucks, UK
2006
2006
W.H. Safranek's book
Properties of Electrodeposited Metals and Alloys
[affil link to
Amazon
or
on AbeBooks affil links] gives a range of 140 to 650hV. Another more generic reference says 250 to 300.
Lead and iron impurities raise the hardness. Try holding your pH to a tight range of 3.8 to 4.0.
- Navarre, Florida
Q, A, or Comment on THIS thread -or- Start a NEW Thread