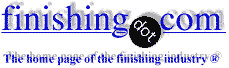
-----
What Coating Should be between a Stainless Steel shaft and a rubber coupling?
Recently, we have had the following experience:
We have a small electric motor. The shaft (2 mm diameter / 42 mm length / cylindrical) is connecting to a tight cylindrical rubber coupling which acts as a linkage to a rotating unit which the motor drives. In between the shaft and the rubber coupling, we apply a grease. The motor rotates at around 5500 RPM.
We found that the electric current drawn by the motor was increasing due to the friction between the shaft and the rubber coupling. We believe the shaft which is a 420 stainless steel can be treated by some surface treatment method to lower the friction generated.
What should this kind of coating be? Zinc phosphating? Passivation? Or other?
Many thanks.
Kwok-wai Chook- Hong Kong, China
1999
1999
I don't think I accept the assumptions if I understand the description.
In view of the fact that well-aligned rotating shafts can be connected together with rigid couplings that allow no movement at all between shaft and coupling, I don't know why you assume there needs to be energy sapping frictional movement between the shaft and the coupling.
Going just from your verbal description, I would think that the coupling is misaligned, and that the rubber is aging and hardening, and thereby causing an increase in the hysteresis loss as the coupling flexes to take up the misalignment.
It is certainly possible to chrome plate the motor shaft, which would reduce the coefficient of friction, but I still don't see why you would want to do that.
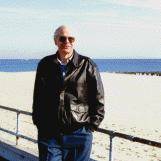
Ted Mooney, P.E.
Striving to live Aloha
(Ted can offer longterm or instant help)
finishing.com - Pine Beach, New Jersey
Q, A, or Comment on THIS thread -or- Start a NEW Thread