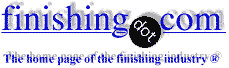
-----
How to get salt spray of 500 hrs on welded joints
2006
How to achieve salt spry resistance of 500 hrs on welded joints? What kind of pre-treatment (phosphating) process or chemicals to be used. Post pre treatment powder coating is done.
Pl explain or suggest companies who have achieved this.
Thanks & regards
First of two simultaneous responses --
Yes, it is difficult to get good SS resistance over welded areas. If it is feasible you may lightly grind polish over the weld and phosphate immediately followed by powder coating. This may increase SS resistance. Or better still use a better performance/ more suitable powder coating over the parts.
Amit Amembal2006
Second of two simultaneous responses --
Dear Mr.Ashish,
A good Zinc phosphated substrate will give easily 1000 hours salt spray resistance after powder coating(remember a well maintained bath with proven chemical is a must).In general salt spray tests are conducted on flat areas only.If you need salt spray resistance on a welded joint you need to prepare the joint properly.Some kind of polishing/grinding needs to be done right on the joint prior to the pretreatment process.This will help in removing soots and other foreign material at the weldment as well the areas nearby.Going for some sort of blasting will definitely give good result.You need to test this to suit your product.
But for consistent results you have to do typical welding and surface preparation.
Your question lacks details of the welding(Arc,TIG, MIG etc.,) and also the specific area of the welding(corner, flange, butt, lap, etc.)
Be specific on your query for getting a detailed reply.
Regards,
2006
Q, A, or Comment on THIS thread -or- Start a NEW Thread