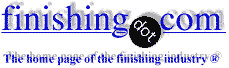
-----
Scratch resistant aluminum finish
Q. I am looking for a finish for several aluminum housings that are used for professional portable audio equipment. The end product has traveled up Mt. Everest across the Sahara and over the Andes. Due to the extreme conditions a scratch resistant finish is required. I was recently shown a sample that had a black glossy finish, that was very scratch resistant, and claimed to be hard anodizing. I sent out samples to several companies and none came anywhere near the sample I had. Any possible finish alternatives would be greatly appreciated. Thank you in advance for any help you may be able to offer.
2006
![]() |
A. Maybe hard anodizing and Teflon bonding. 2006 A. 6061 material you may want to look at a hardcoat, MIL-A-8625 / MIL-PRF-8625 [⇦ this spec on DLA]F Type 3, Class 2 Black. Chris Snyder2006 A. Hard Anodising is almost certainly what you're looking for. As for the samples you received that were not scratch-resistant, I've noticed a tendency for some shops (here in Australia at least) to advertise their finish as hard anodising when it is really just a very thick coating of regular anodising. 2006 |
A. Your description only allows possibilities. Sure sounds like hard anodizing until you said a gloss black. So my guess is hard anodizing with a spray on hard black wax. Serves a a non softening poor mans seal as well as a nice looking finish.
James WattsNavarre, Florida
2006
A. Hi, Kevin. There is nothing wrong with the previous answers: hard anodizing is certainly thicker and harder than conventional anodizing.
However, I once worked with drawer-mounted electronic equipment with brushed aluminum face plates with black lettering on them which looked almost exactly like yours. They were obtained by silk screening the black ink onto freshly anodized aluminum and then sealing it.
I wanted to remove a little bit of the lettering for an in-house prototype once, without taking the time to send the panel out for stripping of the anodizing -- so I tried to scratch the lettering off with sandpaper. It was difficult and time-intensive to remove that lettering even from a small area with deliberate application of sandpaper. So if your samples are scratching easily, I have to wonder if maybe they were simply painted or decal-ed.
Regards,
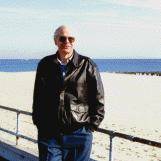
Ted Mooney, P.E.
Striving to live Aloha
(Ted can offer longterm or instant help)
finishing.com - Pine Beach, New Jersey
How to make aluminum scratch resistant?
Q. Hi there. I hope somebody can help; I am a student in my final year of university and I am currently designing a key cabinet. The outside is going to be clad in 0.2 mm thick brushed aluminum. I need a grade which will be scratch resistant and easily cleaned without marking. Will the cladding need anodizing and if so will normal anodizing be sufficient of will hard anodizing be necessary?
Any help you can give would be greatly appreciated as I have not really worked with aluminum in the past.
Kind regards,
March 10, 2009
A. Hi Jack. I think conventional anodizing will be fine and that you can make the cabinet out of readily available aluminum like 6061. Good luck.
Regards,
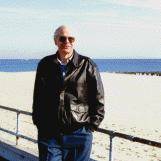
Ted Mooney, P.E.
Striving to live Aloha
(Ted can offer longterm or instant help)
finishing.com - Pine Beach, New Jersey
Q. Hi,
I have been looking for equivalent surface finish process to HARD ANODIZING as per MIL-A-8625 / MIL-PRF-8625
[⇦ this spec on DLA] F Class 2 Type 2, which can be proved more reliable. At the same time, it should be RoHS compliant.
Main objective is to achieve SCRATCH RESISTANCE surface to avoid cosmetic issues.
Thanks
Mihir Rawal
November 22, 2012
A. Hi Mihir, your description conflicts with itself. Type 2 is conventional anodizing, not hard anodizing. Hard anodizing is Type 3 and it is exceptionally scratch resistant.
Regards,
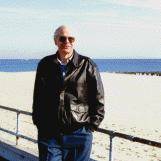
Ted Mooney, P.E.
Striving to live Aloha
(Ted can offer longterm or instant help)
finishing.com - Pine Beach, New Jersey
November 25, 2012
Q, A, or Comment on THIS thread -or- Start a NEW Thread