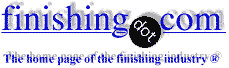
-----
Color inconsistency during hard anodizing of aluminum alloy

Q. Am dealing with hard anodizing for 2024 material, with a specific set of inputs like 250 A/m2, temperature 0 to -5 °C, concentration of sulfuric acid -20% by weight.
Am getting different Color for each run, so what could be the reason for this? Moreover, I supplied the current in 6 steps; like if 35A is required then I provide like 5 amps for 5 min, then increase another 5 amps for next 5 min, finally when it reaches 35A leave it for remaining time. This is the method I am using for total amps calculated for the parts whether it is 20A, 40A or 100 A.
Any suggestions or feedback will be help for me.
Shop employee - Bangalore (Karnataka)
November 17, 2021
⇩ Related postings, oldest first ⇩
Treatment &
Finishing of
Aluminium and
Its Alloys"
by Wernick, Pinner
& Sheasby
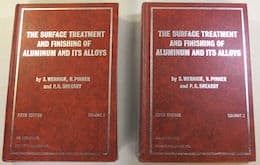
on eBay or Amazon
or AbeBooks
(affil link)
Q. RF power splitters machined from 25.4 mm square extruded al alloy 6063 and temper condition T4 are hard anodized to about 35 micron thickness in sulfuric acid bath. (The component is having a hole of 14.5 dia. and outside diameter is about 18 mm dia. for 150 mm of its 180 mm length) Machining is done using carbide tool.)
Generally the color of the surface is dark steel grey.(required colour) From the same lot of material sometimes we get light greenish grey colour after hard anodizing.
The material composition in both cases are similar.
The finish color is known only after the hard anodizing and then it has to be rejected.
Can somebody suggest solution to this problem?
Engineering consultant - Bangalore, India
2006
A. Believe it or not, it is because of material inconsistency unless you:
1. strip the rejected part
2. re-hard anodize it
3. you could get good(normal) color product.
I often encountered this problem before, however, after few times doing so, my boss was convinced and later we got good materials (cost involved).
In order to convince others, in worst case, you need to strip a normal and an abnormal part together, run it in the same ramp, see the result and if:
you got normal color part from normal product and you got abnormal color part from rejected product then you could conclude material plays a key role. Otherwise you need to check your process more.
By the way, before you strip a good part, think twice; you should have no other choice, or you probably get fired :-)
Singapore
Q. My problem is color issue. The brighter the color the thicker the plating which is not the way it is. Please help about this.
Muhammad Fadhil- Penang, Malaysia
July 11, 2018
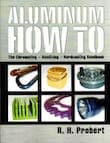
Aluminum How-To
"Chromating - Anodizing - Hardcoating"
by Robert Probert
Also available in Spanish
You'll love this book. Finishing.com has sold almost a thousand copies without a single return request :-)
A. Hi Muhammad. Unfortunately you probably need to spend a lot more words for people to be able to understand and picture your situation. You are hardcoat anodizing type 6063 aluminum but then you are dyeing it? This is unusual, although it is sometimes done on specialty items, such as to distinguish live ammunition rounds from dummy shells.
It is true that thin anodized coatings cannot absorb as much dye as thicker coatings for fully saturated color … but by the time you are doing hardcoat anodizing (0.002" thick), thickness probably has no bearing on dye saturation.
If you are not doing hardcoat anodizing and dyeing of 6063 aluminum, please be clear what process you are doing, and what your exact problem is. Thanks.
Regards,
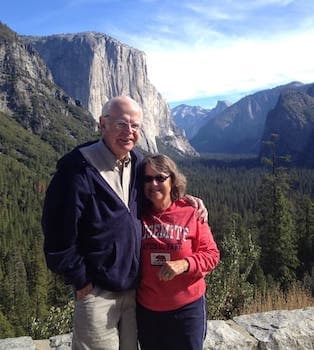
Ted Mooney, P.E. RET
Striving to live Aloha
(Ted can offer longterm or instant help)
finishing.com - Pine Beach, New Jersey
July 2018
Q, A, or Comment on THIS thread -or- Start a NEW Thread