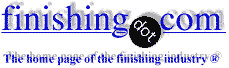
Help? Random uneven thickness on flat surfaces with sulfamate nickel
-----We are having an appearance problem with sulfamate nickel plated nickel iron alloy. The parts are less than two inches square and exhibit a very rough blotchy appearance after plating. Cross-sections reveal a very smooth base metal and the rough appearance is the result of nickel thickness varying from 75 to 200 microinches. High magnification photos reveal no co-plated contamination is present. It doesn't look like gas pits as the roughness/blotches are random, not round. The bath is dummied daily and continuous carbon treated. The bath is also monitored regularly for impurities and kept we below supplier recommended limits. Any help would be greatly appreciated.
Microcircuit package mfgr. - New Bedford, Massachusetts
2006
What is your thickness specification? No engineer would ever specify zero tolerance, so there must be an upper and lower limit. The best way to get a uniform deposit is to have the anode and cathode as far away as possible, so any minute differences in the relative distances are minimised. Other improvements can be made by good but uniform solution agitation. You can also improve things by using robbers and screens. but give us the actual spec and bath geometries so that better guidances can be supplied.
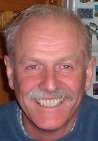
Trevor Crichton
R&D practical scientist
Chesham, Bucks, UK
2006
The thickness specification is 50-350 microinches so holding that is no problem. The parts are plated on racks and are about 12" from the anodes. A circulation pump maintains good solution flow throughout the tank. The problem is only the visual appearance of the plated surface. This condition comes and goes and most product does not exhibit the rough looking surface. Any thoughts on the root cause being organic contamination? I have read other posts where it is believed organics can re-enter the bath in a continuous carbon treatment process.
Steve Tower- New Bedford, Massachusetts
2006
Dear Steve,
You may have to look into the pre-treatment. Since the plating is done after glass sealing there is a possibility of leftover glass on the surface which is not removed completely by your current pretreatment operation. (Do you sand blast the surface?). This might tell why it doesn't appear on all the parts.
Also, if you are doing any other pretreatment to remove the scales after glass sealing check the effectiveness of the scale removal process, left over oxides after heat treatment can cause this type of roughness.
If you are very confident of the above and feel there is not residual contamination you can do a Hull Cell
⇦ huh?
and check the plating quality in that particular current density as the area shown in the picture seems to be in the recess (a low CD area).
- Austin, Texas
2006
I found that the best anti-pit and leveler was a strong fine bubble air agitation system. (sulfamate nickel system) Pump agitation may not be adequate, even with the venturi eductors installed because it does not guarantee a uniform solution flow across the racked parts.
James Watts- Navarre, Florida
2006
OK, so the plating is in spec, but it appears rough. This can be caused by numerous things, including poor pretreatments and out of balance plating baths. The essential thing is to make sure your substrate is suitably "flat" to achieve your spec, so do not use shot blasting or any other surface roughening process; also do not start etching it - you can get differential etching and roughening. However, you must ensure the surface is suitably active for good uniform plating; this means it is as chemically "clean" as possible and is oxide free. Your cleaning process will depend on the substrate, so ask your supply house for the best system. Next, make sure your nickel sulphamate bath is in good condition and is well filtered; personally I like high filtration rates (6-10 turnovers per hour), but I know lots of people disagree with this. Secondly, make sure there is a good leveler in the bath and that it is in spec. There are lots around including NTS and diol; NTS is a real pig to control as it cannot be removed once it is in and if you overdose, you have major problems. Diol is a very good leveler, but can give control problems if you are not used to it. Another good one is saccharin - this also hardens and brightens the nickel, so you can get a lot of useful things out of it for little process difference. I would suggest anything from 0.2-1g/l, depending on your needs. Thirdly, make sure your surfactant is good - any retention of gas bubbles on the cathode will result in uneven plating. Fourthly, if you can extend the anode-cathode distance, do so, if not, you may want to consider screens or a robber system. Hopefully this will help you resolve your problem.
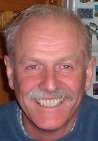
Trevor Crichton
R&D practical scientist
Chesham, Bucks, UK
2006
Q, A, or Comment on THIS thread -or- Start a NEW Thread