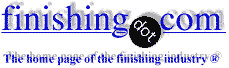
-----
How to know if chemical stripping of hardcoat attacked my aluminum
We needed to strip, weld, re-machine and re-hardcoat some worn aluminum hardcoated parts. Since we didn't have some chemicals, we tried sand blasting to strip them. The brownish hardcoating seemed to vanish with the blasting leaving a white matte surface except for some deep recesses where the sand couldn't reach. Then we finally got the required chemicals and went for the chem strip. After a relatively short time (3-4 min) the remaining recessed brown areas came out white and shinny but the rest, where it was white before, now looks very dark. We used a 40g/L of chromic and phosphoric acids and 200oF. This formula supposedly dissolves anodizing w/o attack to aluminum. What could be the reason for the dark color? I doubt it's only a light effect due to the roughness left by the sand. After the welding and re-machining, could the surface be ready for hard anodizing in a conventional way? What other steps should we take to make sure this dark look won't interfere?
Guillermo MarrufoMonterrey, NL, Mexico
2006
![]() |
What is the alloy? ![]() Robert H Probert Robert H Probert Technical Services ![]() Garner, North Carolina ![]() I don't use that particular etching formulation, so I don't know that this is the case, but... It sounds like you just developed some smut on your parts. A proprietary desmutter might be a good bet, otherwise I believe straight nitric CAN work (although not as well). With regard to the straight nitric - I don't know for certain that it will do the trick nor what else it might do; I use a proprietary blend for desmutting and always recommend the same. But, it may be worth trying on a piece or two to see what happens. Compton, California, USA Sounds like the impurities in the aluminum are surfacing after the stripping. Try etching the parts briefly (2 minutes) and then using your deoxidizer afterwards @ 5-7 minutes. after the deox the parts should be white in appearance and ready to plate. You can also used a nitric acid stripper to strip anodic coating without attacking the aluminum surface. I find nitric a better beast to play with than Phosphoric. The makeup for Nitric stripper is 50% 42 deg. Nitric and 50% DI water. It takes a bit longer. 15-30 minutes roughly. But I like it better than the alternative. ![]() Ryan Cook Toccoa, Georgia First guess: A Cu- & Fe-containing smut, similar to one formed in phosphoric-nitric bright dip, from dissolution and precipitation into the low spots of the blasting. Will remain dark in caustic, come clean in nitric. - Goleta, California ![]() Rest in peace, Ken. Thank you for your hard work which the finishing world, and we at finishing.com, continue to benefit from. |
Thanks to all. We're still at the welding and re-machining stage but as soon as we're thru, we'll go ahead and try with your suggestions.
Guillermo MarrufoMonterrey, NL, Mexico
2006
Q, A, or Comment on THIS thread -or- Start a NEW Thread