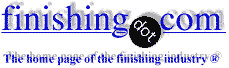
-----
What is causing this on Zinc electrodeposit? Hydrogen Entrapment?
2006
We are Zinc Rack plating a circular part to a spec. requiring 15 to 35 microns. Usually our applied thickness is between 18 to 27 microns in an alkaline bath. Zinc is at 11 to 14 gr/lt, Caustic is at
120-135 gr/lt. We use an internal anode. No agitation. 40 to 50 amps/sq/ft ( 4 to 5 amps/sq.dm.) approx.
We have found these small marks (shown circled in picture) and our client rejects the parts because of these marks. For reference I have traced a 3/4" line, so that you can see how small the marks are.
1.- What can be causing these marks?
One suggestion is Hydrogen Entrapment (not Embrittlement), can this be the case?
2.- And if so, what would the effect of these small marks have on the deposit properties?
We fell these marks are to small to affect the part once in use. If it is roughness, it's to small to have an adverse effect on the part, considering the part dimension and the mark or roughness dimension. The parts are connections for the oil industries.
3.- If the marks are caused by Hydrogen Entrapment, this effect can be visible as soon as the part is processed or does it develop after 3 or 4 days?
Thanks in advance for your help
Plating Shop - Mexico
Hello Hernandez
This may be latent blistering happening due to brightener overloaded or some metallic contamination codeposited. Treat the bath with 0.025 gm perlit zinc dust
⇦ on
eBay or
Amazon [affil link]
and carbon 250 gm per 1000 lit.Also try to maintain optimum bath conc. 10 to 11 gm metal and 100 to 120 caustic.Lower the current to 25 to 30 amp/sqft. In such high bath concentration and higher ampere current density other impurities co-deposit. Also high conc. makes anode polarisd. Do you Have filter on line preferably low ppm.
with warm regards,
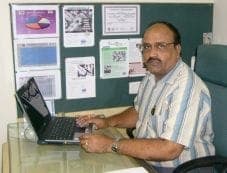
P. Gurumoorthi
electroplating process chemicals - Chennai, Tamilnadu, India
2006
GURUMOORTHI
Thanks for your answer. We do filter continually and the bath looks very clean, you can see through about 90 cms.
We see that the marks are no blisters, they look like comets, with a small circle mark and then a trailing line, like the comets.
This is why we suspect Hydrogen entrapment. So that Hydrogen is trapped during the zinc process and then it escapes, leaving this line.
You can see these marks as soon as we take the part off the line.
Thanks for any additional help,
- Guadalajara, Mexico
2006
First of two simultaneous responses --
What is the alloy of steel underneath? Is it a lead bearing alloy? Under 10X magnification can you see these marks in the steel before plating (as you know, plating magnifies defects).
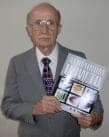
Robert H Probert
Robert H Probert Technical Services

Garner, North Carolina
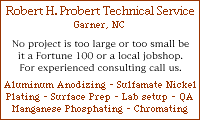
2006
Second of two simultaneous responses --
Mr.Hernandez
Welcome, we use to come across this similar problem. We try to treat the bath as I said earlier. Alternatively we try to remove this by adding some iron removing conditioner which will remove this comet. May be due to some iron might cause this problem. Also try cut purifier addition. Slight excess addition of purifier also will cause this streaky comet.
Thanks,
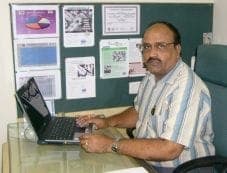
P. Gurumoorthi
electroplating process chemicals - Chennai, Tamilnadu, India
2006
I do not advise meddling with the plating bath, the problem seems to be from the base metal. Large turned parts may get occluded with foreign particles and if you follow Mr Prost's suggestion you may see the root of your problem in your magnifying glass.
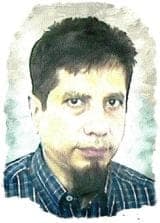
Khozem Vahaanwala
Saify Ind

Bengaluru, Karnataka, India
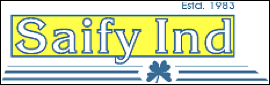
2006
Greetings,
You've indicated zero agitation. Assuming your chemistry and surface prep is all in order, the solution could be as simple as moving the part or perhaps giving the bus bar a good whack ever minute or so to dislodge a adhering H2 bubble. Are you using an (anodic) etching step pre-plate?
TR Hanlon
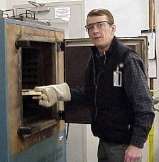
Thomas Hanlon, Materials Engineer
aerospace finishing - East Hartford, Connecticut, USA
2006
Hi There,
I also missed that you're not having any agitation of your parts, except the electrolyte agitation. So therefore I would like to improve your electrolyte agitation as well the determination in which direction the tail of the so called "comets" shows (indicator of which direction and area the gas development is). If the parts are really in order as well as your process (pre-treatment, zinc is in the specs), then check the above tips. Also it will help you to increase the temperature of your bath b/c increasing the temperature decrease the surface tension of the solution. Please remind, that if you use electrical degreasing, that it always should end in the anodic phase.
Regards,
- Mexico City, Mexico
2006
Q, A, or Comment on THIS thread -or- Start a NEW Thread