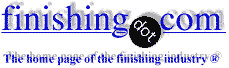
-----
Rust inhibiting coatings for steel hinges
Does anyone know about the coatings on 12 gauge 6-inch steel T-hinges for exterior use? I was thinking of specifying a centrifugal galvanized coating of 5-mils, followed by 5 mils of UV-stabilized black powder coat paint. Is this typically what you would find at most hardware stores, from most large brand name manufacturers?
Thanks much,
SolidMotion Trailers - Lititz, Pennsylvania, USA
2006
2006
I hope I am understanding your question correctly Brian, I work for a company here in Pa. that makes industrial door hinges of all sizes & shapes, usually before we powder coat them, we give them a 2 minute phosphate coating(160 degrees) then a cold water rinse,then a quick dip in a hot chromate rinse(180 degrees),then off to the powder coat they go.
Best Regards,
McKinney Products Assa Abloy America - Scranton, Pennsylvania, U.S.A.
2006
Anyone can to critique on the differences?
1. Molten zinc bath, substrate centrifuged to a zinc thickness of 15-microns, (.015mm), (.6 mils), tolerances of ± 1 micron.
2. Fine grain zinc phosphate conversion coating weight to federal specification TT-C-490
[from DLA]
- Type I, Class 2A: Immersion or Dip application (300-mg/sq. ft. minimum, to 500-mg/sq. ft. maximum), with a dry clear organic seal.
3. TGIC Black Polyester UV-stabilized powder coat paint to thickness of 75 microns, (.075mm), (3 mils).
4. Bulk packed in one-end opened plastic bags for OEM use, as per the samples.
5. Note: All metal parts are plated prior to assembly to enhance rust resistance
6. Finished products to pass salt spray test ( ASTM B117 ) of 500-750 hours, and a QUV test (ASTM G53) of 1,000-1,500 hours, minimum.
OR...
Alternative Acrylic Electrocoating (E-Coat) paint processŪ
1. Molten zinc bath, substrate centrifuged to a zinc thickness of 15-microns, (.015mm), (.6 mils), tolerances of ± 1 micron.
2. Fine grain zinc phosphate conversion coating weight to federal specification TT-C-490
[from DLA]
- Type I, Class 2A: Immersion or Dip application (300-mg/sq. ft. minimum, to 500-mg/sq. ft. maximum), with a dry clear organic seal.
3. Acrylic UV-stabilized Electrocoating to thickness of 35 microns, (.0375mm), (1.5 mils).
4. Bulk packed in one-end opened plastic bags for OEM use, as per the samples.
5. Note: All metal parts are plated prior to assembly to enhance rust resistance
6. Finished product coatings tweaked to pass salt spray test (ASTM B117) of 500-750 hours, and a QUV test (ASTM G53) of 1,000-1,500 hours, minimum.
SolidMotion Trailers, LLC - Lancaster, Pennsylvania
Both processes sound highly capable, Brian. The advantage of the electrocoating is full coverage if the part is complex in shape, has internal surfaces, or any areas difficult to cover because of Faraday cage effects. The powder coating probably offers an edge in appearance.
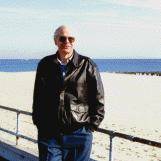
Ted Mooney, P.E.
Striving to live Aloha
(Ted is available for instant or longterm help)
finishing.com - Pine Beach, New Jersey
2006
Q, A, or Comment on THIS thread -or- Start a NEW Thread