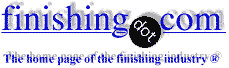
-----
Corrosion problem after phosphating process
2006
Hello, first of all I want to thanks to this web to give me opportunity to send question to your team.And to apologize if my English is not enough cause of my lack ability in English but I encourage to write this letter as the to find out solution of my problem.
Recently I have two problem seriously, as mention below :
1.The result of zinc phosphating process become to red-ish or corrosion/oxidation after 24 hours.This process through pickling by
40% HCl process to remove carbon and rust without degreasing process.The flow process as mention below:
1.40% HCl pickling
2.Cold Water Rinse
3.Surfacer (Activation by Ti sol'n)
4.Zinc phosphating
5.water rinsing
6.Passivator (Use Chromic acid sol'n)
7.water rinse
I think my zinc phosphating result durability to corrosion resistant is too poor.Please suggest to us.
2.My zinc phosphating solution eventually transform to jelly solution.It is about 1-2 hours after production. Whats wrong in this step of production.
Thank you ver ymuch and hope help me to help me to find solution this problem.
- Bekasi, Indonesia
2006
Dear Mr. Made Antana,
you have not mention what is product on which you are applying zinc phosphate coating.
secondly you are not doing Degreasing for oil and grease removal. Please note acid pickling is not just enough to remove all foreign matter including oil, etc.
third point is activation after heavy pickling is difficult to maintain, check pH of the bath.
fourth point-Give minimum 60 sec. dipping time in hot passivation bath after phosphating.
for better corrosion protection you have check all the parameters carefully.
Thanks,
- New Delhi, India
2006
Hi Made Antana
You need to degrease your components before pickling. Pickling operation is to remove rust/oxide scale from the steel/ iron. Hydrochloric Acid can not remove oil / grease.
So, your sequence should be degreasing, rinsing, pickling, rinsing.....etc.
regards,
- Chennai, India
Thank you very much for your kind reply, usually I do the complete process from degreasing,rinsing,pickling,rinsing,.... finally with/without passivation.But this customer used to do the process sequence as I mention at letter no 39564.Their process pickling 40 % HCl rinsing, rinsing, surfacer(activator 0.2%),zinc phosphating without passivator. By this process I heard that their result of phosphating not getting problem of corrosion and can stay at HCl environment for about 2 month without getting corrosion.
Please give us suggest, thanks
- Bekasi, Indonesia
2006
2006
Degreasing is missing in your processing sequence. Navin Maheshwari and Keshava Prasad have already suggested the importance of degreasing. It is essential to remove any greasy contaminants and corrosion products from the surface to obtain a good phosphate finish. Moreover, degreasing in organic solvents usually promotes the formation of fine-grained coatings while strong alkaline solutions and pickling in mineral acids yield coarse coatings.
I am surprised to note that zinc phosphate coating prepared using a processing sequence that does not involve the degreasing and final passivation treatment remains good in HCl environment for 2 months without getting corrosion.
Zinc phosphating bath transform to a Jelly solution?
I presume that you have observed the formation of ferric phosphate
(white in colour) in your zinc phosphating solution.
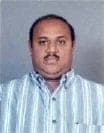
T.S.N. Sankara Narayanan
- Chennai, Tamilnadu, India
(ed.note: The good doctor offers a fascinating blog, "Advancement in Science" )
2006
Corrosion after phosphating. Thanks again, During I have been waiting for your reply, I try to simulate pickling process by make HCl solution by dilute 20 gr (HCl 32%) in 1 liter of water (Assumption it is 20 % HCl solution).After that I do process zinc phosphating as usually than I found that corrosion resistant in HCl fume environment increase from 2 days to 7 days.It is the right effort or wrong?. AS adding information the point of Zinc phosphate solution are TA=24;FA=3.5.
Once, What the best value of FA and what the optimum ratio of TA/FA.
Thank you very much for your answer.
- Bekasi, Indonesia
Q, A, or Comment on THIS thread -or- Start a NEW Thread