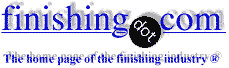
-----
Coating on inside surface of aluminum tubes used in heat exchangers
2006
Dear all,
We mfr. aluminum heat exchangers, both air and water cooling. In water coolers we are facing corrosion problem which is occurring nearly after one year of use.We learnt from somebody that, inside coating would prevent the corrosion. would you pl. suggest us the method of coating where the tube size is rect 2.5 mm x 3.5 mm. Seeking your help in this subject.
Regards,
HEAT EXCHANGERS. - VASAI, MAHARASHTRA, INDIA
Most likely you have contamination that is corrosive or is reacting to form a corrosive mixture. Aluminum is very difficult to protect for it is very sensitive (active). Any coating must be absolutely impervious. Once coated, any void, pore or crack, no matter how small, become a dismal failure point. I'm afraid that, unless you can treat your fluid with anticorrosion products, you will have to consider another base metal to handle that situation.
Guillermo MarrufoMonterrey, NL, Mexico
2006
2006
Thanks Mr. Guillermo Marrufo.
Sorry for the long silence. We are using D.M. water for testing and we have been told by our clients that, they also use D.M. water. But after a due course of time chances of contamination is there if water is not changed on time. You have any idea of chromate conversion coating, plasmathermic coating? can this help, create an inside surface of the tube?
Regards,
Heat Exchangers. - Vasai, Thane, Maharashtra state, India
Dear Sir, the corrosive nature of your application does require that you incapsulate the surface as suggested by the first respondent. The coating that will provide excellent chemical corrosion protection is NICKEL - Teflon matrix. Deposit electroless nickel and teflon at the same time to a thickness of .001. This is the solution we have used for similar applications in the U.S.
Ed FabiszakMorris, Illinois, USA
2006
Mr. Fabizak,
According to many technical books and papers and to our own experience, the incorporation of particles to an electroless nickel matrix is done for other purposes (i.e. dry lubricity, wear resistance and hardness), not for corrosion resistance. Do you have evidence that the Teflon particles indeed are responsible for a corrosion resistance improvement in such application? Or could it be just a coincidence that platers capable of doing composite plating are usually better qualified for the whole plating procedures, thus render a better product? Best regards,
Monterrey, NL, Mexico
2006
Q, A, or Comment on THIS thread -or- Start a NEW Thread