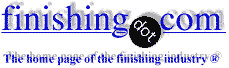
-----
Recommended plating for automotive connectors
2006
Hello everybody,
I am interested in getting recommendations with respect to the following topic: for a new client we intend to make automotive devices which have also an electrical connector. Our customer is trying to push us go down with our price(who doesn't these days?), and we want to look at other plating options.
Have you encountered during your experience of working with these processes such a thing as 'recommended/not recommended/not allowed' combinations of platings?
Thanks in advance,
automotive parts maker - Apeldoorn, The Netherlands
Please start with what plating combination you are using now, Leo. Readers don't like to spend a lot of their time making a detailed suggestion only to have it instantly dismissed as "that's what we already do". Also, it's difficult to suggest anything without knowing any details of exposure, voltage levels, current, etc. For example, there are connector materials like electroless nickel and tin which may be fine for most applications but won't be acceptable for very low signal levels where only precious metals will do. Good luck.
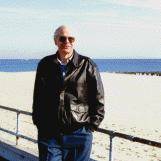
Ted Mooney, P.E.
Striving to live Aloha
(Ted is available for instant or longterm help)
finishing.com - Pine Beach, New Jersey
2006
2006
Ted, thanks for the recommandations. Indeed we are talking about very low voltage levels (up to 5V). Obviously the best solution is Au(connector)/Au(counter-connector), but as well we have seen Ag/Ag as being a functional combination. At the contact point between connector and counter-connector there is a gasket isolating the respective space and the temperature range is -30/140 °C.
Also, do you think mixed combinations (Ag/Au) or partial plating could work ?
Thanks in advance,
Leo
- Apeldoorn, The Netherlands
I'm not actually a connector expert, Leo. I was trying, as the site administrator, to clarify the question to facilitate getting it answered by someone who is. The temperature range may rule out tin, but electroless nickel sounds possible.
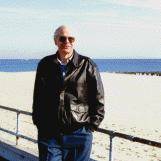
Ted Mooney, P.E.
Striving to live Aloha
(Ted is available for instant or longterm help)
finishing.com - Pine Beach, New Jersey
2006
First of two simultaneous responses -- 2006
A variety of plating options are available for connectors, namely, hard gold, Pd-Ni, Gold flash/Pd-Ni, Rh, Ag, Ni, electroless Ni, Sn and Sn-Pb alloys. It is not possible to give a detailed account here.
Noble metal plating could be the wise choice in many instances. If your customer is pushing you to go down with the price ¯ you can use tin plating. But tin plated connectors are susceptible for fretting corrosion and they are not suitable for high temperature applications. The tin plated connectors used in engine hood could experience up to 155C and under such conditions they fail very quickly.
Pd-Co alloy plating is one of the latest developments in the finishing of electrical connector contacts.
Lubrication could improve the service life of all plated connector contacts by several folds.
If you need more details, please refer the following:
Robert S. Mroczkowski,
"Electronic Connector Handbook: Theory and Applications", McGraw-Hill, New York, 1998,
Chapter 3, pp. 3.1-3.49.
Morton Antler, "Materials, Coatings and Platings", in
Electrical Contacts: Principles and Applications P.G. Slade (Ed.), Marcel Dekker Inc., New York, 1999, Chapter
7,
pp. 403-432.
Plenty of papers published in IEEE Journals: http://ieeexplore.ieee.org/
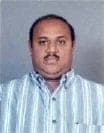
T.S.N. Sankara Narayanan
- Chennai, Tamilnadu, India
(ed.note: The good doctor offers a fascinating blog, "Advancement in Science" )
Second of two simultaneous responses --
I would suggest looking into gold over mid phos EN. The thickness of each would be a factor of necessary conductivity and wear resistance. Any reduction in gold thickness would have cost savings but they would have to be significant enough to outweigh the additional manufacturing cost.
Gene Packmanprocess supplier - Great Neck, New York
2006
Q, A, or Comment on THIS thread -or- Start a NEW Thread