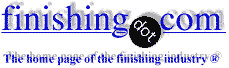
-----
BIG problem with black powdercoat on 7/8" 14 gauge HR tubing
We need some expert help. I work for a small sheet metal shop in rural up-state New York. We mfg. metal chair frames for the office furniture industry. PROBLEM: Our 7/8" x 14 gauge low carbon tube is coming off the powder line looking BAD. The material goes in smooth and clear of surface defects and by the time it comes out of the oven it looks like there are spots and blemishes of surface rust under the coating. We've had the pretreater in here a couple times, as well as the powder guys. We're not very sophisticated here, we use a flat black from Sherwin Williams called "Midnight Magic". The floor people are convinced it's something different with the material because the 7/8" tube is the ONLY thing that's a problem. Can anyone think of a reason for this to be happening? I have to get this problem resolved FAST. I've got 900 frames that have to go through by next Friday and reworking these frames (buffing, sanding, grinding, etc.) is NOT an option. I need some ideas to throw at my metal supplier. We've been powder coating this material for several years. No problem. A few months ago we moved to a different facility and started having "blemishes" appear on parts coming out of the oven, but not all the parts. We generally run carbon steel parts. Everything is fine EXCEPT this 7/8" tube. Any idea what that could be? We're not powder coating experts, and we're at the end of our list of things to try. If our supplier has changed the "grade" of material he's sending us and hasn't told us, could that be the culprit? How can we tell if this material is the same as what we got six months ago?
metal products - Cuba, New York
2006
First of two simultaneous responses --
Based on your description and the picture I vote for fluidizing or powder/air adjustment problem causing the paint to flow unevenly from the gun, maybe worn gun tips and a hurried production schedule exacerbating the problem. Did I win?
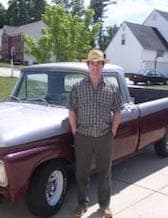
Sheldon Taylor
supply chain electronics
Wake Forest, North Carolina
2006
Second of two simultaneous responses -- 2006
Hi,
We require a little more info.
1)Powder type epoxy/poly or polyester.
2)If polyester - was it classed as TGIC but now classed as TGIC free?
3)The picture image shows a flat area - does this area have the same defect?
4)Have you tried another batch or even another colour -if not, why?
You could over-spray your powder with a waterborne primer - one specifically formulated for use with powder coating -allow to air dry
- spray powder and then bake. However the second powder will follow the contours of the old powder - so stripping maybe your only option.
Have you tried to cut down the KV when spraying this component, this may help if your powder is OK on other items. Have you checked the film build - from the photo it looks as though it is very, very heavy.
powder mf - Birmingham, UK
Dear Sheldon,
Thanks for taking time to answer. No, as far as we can tell, it isn't a fluidity problem. We checked and re-checked the powder and the guns. We actually ran the parts thru with three different batches of powder and various mixes of virgin/reclaim. We're down to a material problem. Our basis for that is that ALL the other material that goes thru powdercoating comes out of the oven looking very nice. This particular 7/8" tube is the ONLY thing that looks like the photo I submitted. I just rec'd a batch of material from a totally different supplier. We're testing that now. Cross you fingers!
- Cuba, New York
2006
Marion, please write back and let us know if the new paint solves the problem, I hope it does.
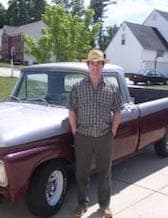
Sheldon Taylor
supply chain electronics
Wake Forest, North Carolina
2006
We have run into a similar problem before and that is porosity in the steel. I am not sure why but this porosity seems to effect tubing more than flat material (probably the forming process). What kind of degreasing system are you using? If it is liquid it is probably soaking into the pores and comes out when the part is heated, thus ruining your finish. We found that running the part through the oven after degreasing and before powder helped to purge the remaining liquid and then we could powder it on the second pass and the pre heated part painted even better.
Good luck!
Axis Laser - Wallingford, Connecticut, USA
2006
Q, A, or Comment on THIS thread -or- Start a NEW Thread