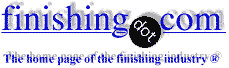
-----
Anodized parts are getting fingerprints from unknown step
Q. Our shop uses a nickel acetate seal process on all Type II anodizing. One customer's parts are processed as follows: 60 sec clean in a Houghton cleaning solution at 160 °F, rinse, 15 sec R5 at 220 °F, triple rinse, heavy etch in caustic soda ⇦liquid caustic soda in bulk on Amazon [affil link] solution at 125 °F, triple rinse, 35 min anodize @ 14 V, triple rinse, nickel acetate seal for 10 mins @ 190 °F, parts triple rinsed w/final rinse DI water.
Once parts are processed here, gloved hands are used to pack the parts. Once the customer receives the parts, they are handled, screened and baked at 250 degrees for 10 min to cure the screen. Once parts come out of the oven, fingerprints can be seen on the parts and cannot be removed. There is also at this time a slight haze to the finish of the part. We have our theories as to what's causing the problem, but desperately need to hear what others may think. Please if you have any thoughts let us know.
Justin Crispindustrial anodizing - Indianapolis, Indiana
2006
Treatment &
Finishing of
Aluminium and
Its Alloys"
by Wernick, Pinner
& Sheasby
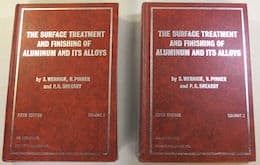
on eBay or Amazon
or AbeBooks
(affil link)
Hello, Justin. I respectfully suggest that for the best response, if you "have your theories", that you present them. I know that readers often don't respond because they're thinking that they'll spend many minutes thoughtfully preparing a suggestion, only to have it dismissed in two seconds flat with "yeah, we thought of that one already". Better to present your theories, please. Good luck.
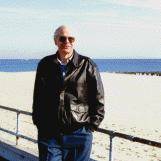
Ted Mooney, P.E.
Striving to live Aloha
(Ted is available for instant or longterm help)
finishing.com - Pine Beach, New Jersey
2006
A. I would say that the parts are being mishandled at the other end. That is, if you are certain that the parts come off of the line with gloved hands. Ask your customer if they have a cleaning process before they are screening their parts; also if they are using gloves to handle their parts as well. If all else fails get the local law enforcement to run a check on the print and find out which end it is occurring on.
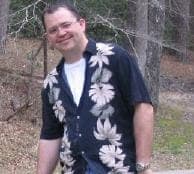
Ryan Cook
Toccoa, Georgia
2006
A. As Ted said above, give us more information. Alloy? 14 volts is not much for some alloys and makes a large pore thru which stuff in the pores (like dissolved aluminum or calcium) can cook out. 250 °F or 250 °C? That will crack the aluminum oxide which has 20% the expansion coefficient as the underlying aluminum. What is the calcium content of the seal? Do you pass the ASTM seal test? You did not show a desmut or deox after the alkaline etch! What is the dissolved aluminum content of the anodize solution?
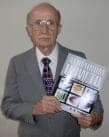
Robert H Probert
Robert H Probert Technical Services

Garner, North Carolina
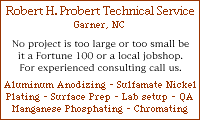
2006
Q. We do have a desmut between the etch and anodize. The alloy is 5052-H34. The coating thickness of these parts is a nominal .3 to .4 mil.
Justin Crisp [returning]industrial anodizing - Indianapolis, Indiana
2006
A. Something is cooking out during the bake, whether F or C, 250° will crack the anodic film. Let's try a fresh new seal in the lab with D.I. water. Let's try an anodizing solution with the dissolved aluminum down to 8 to 12 grams per liter. Let's try a 5% Nitric Acid dip (rinses on both sides) between the anodizing and the seal. Finally, 0.0003 is too thin, try 0.0008 inch thick (out of a clean anodizing solution, thru the Nitric dip, and into a fresh seal solution).
Anodizing job shops are notoriously famous for seal neglect. The seal is the weakest solution in their shop so they think they can slop thru it; however, the opposite is true. The weaker the solution, the easiest and fastest to contaminate. Let us know what you find.
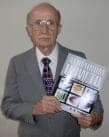
Robert H Probert
Robert H Probert Technical Services

Garner, North Carolina
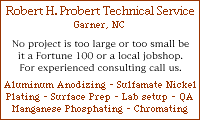
2006
Q, A, or Comment on THIS thread -or- Start a NEW Thread