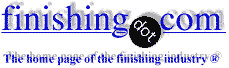
-----
Leadframe Plating, NiNiP vs Full Ni (without NiP)
2006
Hi All,
Our current concern is on the effect of the elimination of the phosphorous plating over a copper material, or leadframe. All of our leadframes are plated with Ni + NiP. Recent customer complaints on our products revealed that we have a problem on the plating itself. We are working full time on the Pure Ni plating leadframe qualification(without the NiP) but we found severe package delamination (taken through CSAM) as against to the Ni+NiP (control) plated leadframe.
Not only this, we also encountered poor solder (SnAgSb soft solder) wetting when we only have 8%H2 and 92%N2 gas (also called as mixed gas) at our diebond process. The control have no problem at all with this condition. We resolved this problem by increasing the mixed gas to 14%H2.
My questions are:
1.0 What is basically the purpose of the Phosporous in the leadframe plating. Or its purpose in the combination NiNiP?
The P-thickness by the way is only at 0.127 to 0.5um. The overall plating thickness is only about 1.27 to 3.0um.
2.0 Other than increasing the H2 gas, how can we improve the wetting of the solder?
3.0 Are there any available related literature on this topic that you can share?
4.0 What are your challenges in the use of Pure Ni plating only and how did you resolve them?
Thank you very much for any response you can provide.
Semiconductors - Cabuyao, Laguna
Jeff: First off what is the base copper material.If it 7025 you have to use special chemistry to descale.
Not sure why your trying to solder directly to Nickel
If these are Semiconductor lead frames Tin Or Tin Lead
is usally applied for solderbility when using a nickel underplate.
- Anaheim, California
2006
Jeff, we have initially did some evaluation with a full nickel leadframe and result shows mixed gas supply on a die bonder helps promotes better wetting. Have validated also on a certain machine model with less gas supply has poor wetting result. Further more machine mapping is on going to benchmark the gas supply features of the better machine.
Gary Martin- Calamba, Laguna
2006
The importance of Phosphorus in the Plating process for Leadframe are 1. To have a good corrosion protection,2. Lower porosity, 3. Non-Magnetic 4. Not prone to Stains and last Pits Free deposit
nico medrero- Pampanga,Philipines
October 22, 2009

Q, A, or Comment on THIS thread -or- Start a NEW Thread