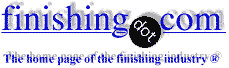
-----
Roughness/pitting on flat vertical surfaces in Bright Ni
2006
We are bright Ni/Cr plating a large volume of highly polished brass items, and frequently have a problem where we experience either roughness or pitting (sometimes both) on flat, vertical surfaces of plated parts. We can sometimes fix the problem by Cr strip, buff Ni and re-Cr, but this is not always successful, depending on the severity of the problem.
This is our process:
Soak Clean @ 70°C
Cathodic Clean @ 70°C
Anodic Clean @ 55°C
Double Rinse (counterflow)
Acid Dip
Double Rinse (counterflow)
Cu Alloy Activator
Double Rinse (counterflow)
Bright Ni
Drag-out
Double Rinse (counterflow)
Cr Drag-out
Cr Plate
Cr Drag-out
Cr Neutraliser
Double Rinse (counterflow)
Hot Rinse
Deionised spray rinse
So far I have tried 3 different soak cleaners and 2 different electrocleaners, with little difference in results. We also tried dumping, cleaning and refilling all rinse tanks, adding anti-pit agent to the Ni plating solution, adding wetter to the Ni plating solution - once again with little difference to results.
We filter over activated carbon, usually changing filter packs once per week. I'm not sure if I'm using the right amount of carbon though
- our tank is 3200 litres, I put on about 1 litre of carbon. Any more than this, and the filter pack fills up virtually overnight. I'm wondering if this is because of excess activated carbon, or because there is simply so much organic contamination in the solution it really needs the filters changed daily. I should add, the solution is a slightly brown-green colour, whereas I generally expect Ni solution to be bright green.
Any advice would be greatly appreciated
Plating Shop Supervisor - Brisbane, Queensland, Australia
![]() |
I'll start with the last first. The dark color of the solution and the fact that you are plating brass would leave me to believe that the bath is high in organics. A high pH treatment (oxidation and carbon) would seem to be in order. With this thought in mind, the possibility that grease/buffing compound is getting to your nickel tank and combining with the wetter/anti pit to create some or most of this organic contamination. For this you must talk to your vendors and get a combination of soak cleaner and electrocleaners that will completely remove your buffing compounds without attacking the metal specifically de zincing the surface! process supplier - Great Neck, New York Hello John, process engineer - Malone, New York Sounds like organic contamination is a good possibility. Have you tried a batch carbon treatment? I would take a sample of the bath and run some clean (clean offline) brass panels on the nickel. See how they look, then carbon treat your sample and run another to see if it improves. Might also want to try one that has been peroxide/carbon treated. That ought to tell you something. Your vendor should be able to provide you with procedures. ![]() Trent Kaufman electroplater - Galva, Illinois DEAR SIR MAY BE I'M THINKING LOUD BUT IF YOUR BRASS CONTAINS ZINC WHICH MAY CONTAMINATE YOU NICKEL TO DARK COLOUR/AND YOU MAY HAVE PITTING INPACE OF THE DISSOLVED ZINC , I BELIEVE YOU SHOULD USE A SPECIAL NICKEL BEFORE YOUR BRIGHT NICKEL OR A COPPER PLATING UNDER THE BRIGHT NICKEL . GOD LUCK AND GOD BLESS ![]() Khair Shishani aircraft maintenance - Al Ain, UAE |
2006
First you want to find out what cause your roughness/pitting problem. It could be separate reason.
ROUGHNESS as caused by particulate in solution-
During operations, get at least a liter of the solution. Run it thru a fine laboratory filter paper and under a microscope, Check for particulate matters.such as fine particles carbon, Metals, etc.( if no or minimal amounts of particulates found go to the next step)
Particulates are introduce to the solutions as follows:a) airborne b) carbon Particles not completely filtered. C) Rip anode bags d)a lot of undissolved materials at the bottom of the tank.
Transfer entire solution into another tank using a 10-micron filter or better. Check anode bags for rip or simply replaced them.Clean the bottom of the tank.
ROUGHNESS as caused by cleaning procedure:
ANODIC Cleaning Of Brass at a higher voltage can cause preferential etching of Zinc at the grain boundaries and copper oxide formation. Your acid rinse might not dissolve all of the oxide. Try skipping this one and see what happens.
ROUGHNESS as caused by Chemistry imbalance-from above filtered solution, run a Hull Cell
⇦ huh?
test. Weigh the cathode before and after the test to determine plating efficiency.After test check deposit for roughness and pitting.(if none then your problem is one of the above.)
Make adjustment as necessary.(better have your chemical supplier do this for you.)
Low cathode efficiency might indicate Cross-contamination with chrome solution.
Good Luck,
- Mays Landing, New Jersey
First of two simultaneous responses -- 2006
Thank you everyone for your replies and suggestions. I will try to address each poster's issues sequentially:
Gene Packman:
Yes, I am fairly certain that our cleaning process is not adequate. This is evidenced by a ring of soil around the top of our acid dip. I have tried four different cleaning processes in the past 6 months, none of which have been particularly successful. Our supplier is currently working on obtaining a new cleaning process for us, although I'm not sure when that will happen. Consequently, we are still struggling along using an inadequate one - I suppose this will lead to more organics in the plating solution.
Mark Baker:
We have had the solution tested for both iron and copper contamination, both were negligible. I don't think this is our problem.
Yes, the filtration method is continuous carbon filtration. I don't plate while packing the carbon on to the filter (it is done at the end of each days' shift).
Trent Kaufman:
We haven't tried a batch carbon treatment, yet, although on the advice of our supplier we are starting one today. He took a sample and treated it with permanganate and carbon, and almost 10% of the volume of the solution settled to the bottom as sludge.
Our filtration is 10,000 liters per hour on a 3200 litre solution. This is just only slightly over your minimum of 3 turnovers/hours, and with the amount of impurities we seems to be introducing, it might be we need way more.
Khair Shishani
Dissolved zinc I'm not sure of, it wasn't tested with the iron and copper (not sure why, must ask our supplier). Also we do dummy plate quite often (usually weekly), so I'm not sure that metal contamination would really be our problem.
Hamilton Solidum:
Unfortunately I don't have the lab. facilities here to do most of the tests you speak of (I only wish I did! but I'm not sure the company would fund it). I did try skipping the step of anodic cleaning, it made no difference, so I'm fairly certain it's not that.
We do have some minor amounts pitting on the hull cell test, but nowhere near the problem we have on the production parts. This leads me to wonder if the problem is mostly not in the nickel, but in the cleaning or other pre-treatment, and if so how it could be solved (I and my supplier are running out of ideas).
Unfortunately because of our location we are pretty much tied to one supplier, unless we deal with one whose local rep is based in another city, or even interstate.
Regarding the cleaning system, we run at a maximum temperature of
70°C (158°F), but still experience some discolouring/darkening (I assume this is dezincification?) of the brass. For a short time we had a cleaner @ 90°C (194°F) which discoloured the brass even worse, but seemed to clean well.
Today we commence the batch treatment with KMnO4 and carbon hopefully that will bring some good results.
Sorry for all the what seem like stupid questions, my former background is electroless nickel plating on aluminium and I don't know a terrible lot about either brass or bright nickel plating. Once again thank-you for all your help.
- Brisbane, Queensland, Australia
Second of two simultaneous responses -- 2006
Dear John,
You have 3 issues to solve.
1.Roughness
2.Pitting
3.Colour of the solution- Brown green.
All three problems relates to poor maintenance of your bath and shop floor.
1.Roughness:due to dragged in particle/dust from air/fallen Ni particles/Ni. anode particles from the anode bags, etc.-Keep you shop floor dust free.Run a heavy magnet thru the bottom of the tank to remove needle like pieces of Nickel anode,Take out all your anode baskets and clean.Wash anode bags/replace old bags with new.Clean the air agitation pipe and check for entrapped foreign particles.See to it that activated carbon does not escape to the tank from the filter pack-this also causes roughness!.
2.Pitting : Due to dragin of oil,due to excess additives,imbalance in boric acid etc.Best way is to carbon treat with care.Try the following for a while-See that you clean the filter say after every 4 hours of carbon run.There is a chance that adsorbed organics is left out by the activated carbon after 3-4 hours.Overnight carbon filter may cause re introduction of organics back in the bath.
3. Color of the solution brown-green: usually related to iron impurity though you plate brass items!. Why take a chance.Give the bath a high pH (above 5.5) treatment.Here also you have to be careful.Use high grade Nickel carbonate to increase the pH. Remember to clean the filter before you reduce the pH to operating level.Or else the trapped iron will dissolve escape in to the bath.Lastly If you have a spare tank, transfer the solution, clean the working tank thoroughly and restart.
john,do all this.You will be out of all your problems
Good luck.
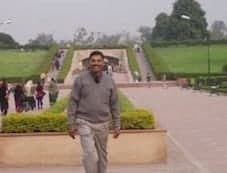
T.K. Mohan
plating process supplier - Mumbai, India
John,
As you said, your hull cell test doesn't show as much pitting as your production parts. It may indicate that your problem is the part itself. to test this, I recommend attaching a Brass Hull Cell panel along with your production parts.If both of them have the same amount of pitting, Run a second test with 1/2 half the current density. See what the results are. Obviously, if the brass hull cell panel Plates good then it is your production parts.
I did a lot of bright Nickel on highly polished brass surface(Casted Products). I used Brass Hull Cell panel as test pieces(Bent Cathode test and leveling characteristics) along side with the production pieces. If the test panels don't come out right, then I would concentrate on the Process.
I end up doing the casting myself.
Good Luck,
- Mays Landing, New Jersey
2006
Stop using carbon,only use filter powder. Carbon treating requires heating to 140 degrees F. pumping over to a treatment tank, lowering ph, adding peroxide and sprinkling filter powder on top then let it settle for about six hours. Then pump the top clear solution back into your plating tank before it can cool making sure you aren't pumping the dirty precipitate off the bottom. Just putting carbon in a filter doesn't make sense.
Here is what I would do. Get some clean steel plates about 3ft x 3ft. Bend them into a nice 180 degree concave horizontally and plated them in you tank at 1 to 2 volts and no agitation overnight. Next morning pull them out very slowly and see what kind of junk you have in the low density areas.You may want to let the tank settle for a day or two.Your problem may be caused by initial blow out every time you repack and start your filter.You may find out you don't have to run that filter nearly as much as you think.Make sure your air coils are about 2 to 3 inches above the bottom of your tank so as not to stir up debris from the bottom of the tank. I don't know if this will help you but it seems to work for me with this kind of problem. Good luck, Frank
- St. Louis, Missouri, USA
2006
Thanks everyone for your advice. Just to follow-up, we (mostly) have this problem solved. In the majority of cases, it ends up having nothing to do with the nickel solution at all, but rather the preceding steps. It seems we are frequently getting some kind of floating contamination in our water rinses, acid dip and microetch solutions. I have not yet confirmed the source of this contamination.
Usually, when the problem begins to appear, I go through each tank in the line prior to the nickel, take a sample of them and inspect for contaminants, then replace the one I consider most likely to be causing the problem. Unfortunately this can get quite expensive in terms of waste removal and new chemicals in the case of the acid/microetch solutions, and also water for the rinse tanks (not to mention, we are currently in the worst drought for 100 years here).
If anyone could give me suggestions on what the source of these contaminants might be, it would be much appreciated.
So far I have considered it could be incoming water quality, nickel flaking off plated racks or swarf coming off machined parts (we do plate some of these in addition to the polished components previously mentioned.
Thanks,
Plating Shop - Brisbane, Queensland, Australia
2006
2007
Well I have the same problem on high polished brass parts, and I didn't find the answer yet, but the customer that send me the parts pissed off and decided to go to another shop because we couldn't deliver on time and at the beginning everything was very well but now he is back because he started to have the same problem. I saw you have done lot of efforts trying to solve the horrible problem (more than me) I noticed that the problem doesn't have a pattern in my case, and you haven't solved it at all, (I don't know how either) but the things that I saw was:
1) In my case it happens on parts that have holes, (I suspect that they get buffing compound in to those holes and are difficult to remove from there, usually alkaline cleaners are too bad removing solid buffing compounds, I did not saw you using solvents on your process) my hypothesis is that fat and greasy components of the buffing compounds are entrapped in to the holes and the wetter agent of the bath make then soluble in water then that cause the pitting problem but as you see I have this problem yet because I didn't have changed my cleaning process yet.
2) once upon a time there seems that everything was under control and the method that worked pretty much closer to that was when to change everything that could be etching the brass before the bath. specially the acid dips because if you
use HCl dip and you use the same line for ferrous parts it can appear ferrous chloride on the acid dip and that etch the brass, very similar to you.
3) we add cyanide flash before nickel thinking that the zinc was attacked in some part of the process including the bath and it worked well for a small period of time or the pitting problem was in some way improved but with copper or not it appeared again later.
I hope this give you any idea I would like to know what do you think about it and maybe we can find a solution.
- Bucaramanga Colombia
Well, I run many test with cleaning with solvents and in my case that wasn't the problem, so I tried a different approach.
I remember that some day reading the ASM HandBook of metals I saw some advice about zinc die castings, and if the casting had 40% or more of zinc it must be plated with a layer of copper of a 5 µm minimum so I did it I applied copper and the problem disappeared.
Hope to work with you
The problem wasn't in my preparation, it was that the pieces were not uniform in the mix!
- Bucaramanga, Colombia
2007
Q, A, or Comment on THIS thread -or- Start a NEW Thread