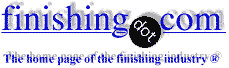
-----
What process for Niobium Coating?
Anyone out there know of a process to electroplate niobium onto a stainless steel substrate? Is thick film sputter coating of niobium doable, and if so what thicknesses of deposited material are reasonable?
Michael Auld- St. Charles, Missouri
1999
First of two simultaneous responses--
Reasonable thickness for sputter coating depends on the application requirements. Usually, up to 10 microns is trivial. Up to 0.01" (25 microns) is relatively simple although it might not be feasible if you want the coating to withstand lots of bending. Above 0.01" is doable but it depends on the requirements of the coating, the coating process, etc.
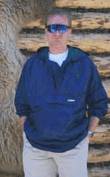
John Davis
- Berthoud, Colorado, USA
1999
Second of two simultaneous responses--
It shouldn't be much of a problem to sputter niobium onto your substrate to a thickness of 0.001" or so. You can also look at cathodic arc or e-beam deposition. The cheapest approach is e-beam. Cathodic arc coatings have the best adhesion, but the process produces droplets of material that leave holes in the coating, though not that many with niobium. If the coater uses an unbalanced magnetron for the sputter system, the sputter deposited coating can have nearly as good adhesion as the cathodic arc deposited coating.
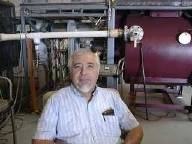
Jim Treglio - scwineryreview.com
PVD Consultant & Wine Lover
San Diego, California
1999
1999
The main problem with depositing thick layers by PVD processes is the buildup of stress in the film as the thickness is increased. This intrinsic stress can cause cracking or blistering of the coating. If the stress is controlled during deposition, thickness is not a problem except for economics. If you want a thick coating consider plasma spraying. Niobium can be electrodeposited from a molten salt (fluoride or chloride) electrolyte.
Donald M. MattoxSociety of Vacuum Coaters
Albuquerque, New Mexico
"Handbook of Physical Vapor Deposition (PVD) Processing" (2010) [on AbeBooks or eBay or Amazon affil links]
and "The Foundations of Vacuum Coating Technology" (2018) on AbeBooks or eBay or Amazon affil links]
Sputter or cathodic arc coating of thick niobium films is practical and can result in high quality films with good adhesion and dense, high performance films. Deposition of thick coatings requires special attention to the development of film stress in the coating which can give rise to adhesion problems along with spatially local film continuity failures. Niobium is quite reactive and the vacuum system used to deposit the film should be capable of attaining a low base pressure and have no vacuum leaks in order to prevent unwanted chemical reactions in the film. If the required film thickness is large, cathodic arc coating may be a better option, though this technique often results in particle inclusions in the film. These particles may not be a problem, depending on the coating application. Both sputtering and cathodic arc deposition can result in high purity thick coatings with excellent properties if done correctly.
Stephen Elliott- Boulder, Colorado
2002
Q, A, or Comment on THIS thread -or- Start a NEW Thread