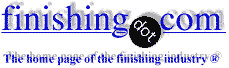
-----
Sulphamate Nickel plated specimens fail the 200 hours salt spray test
Recently we have a problem with the process control of our Sulfamate Nickel Plating process.
The customer requires that the coating, thickness 0.0015 - 0.002 inches, shall pass 200 hours of salt spray test.The chemistry, the plating parameters did not change. New solution and new etch solution did not help,either filtration(1um filter) and purification. The maximum corrosion resistance last from 10 to 24 hours. Under the microscope the plating looks nodular(cauliflower-like), it appears that corrosion begins at the crevice between nodules. Panels that passed salt spray in the past looked smooth without nodules. What parameters can be altered in the bath chemistry or plating conditions that would change the plating morphology from nodular to smooth?.
landing gear - Oakville, Ontario, Canada
2006
Hi Tad,
You had mentioned you changed the etch solution and the nickel sulfamate bath. Was the etch rate tested after changing the solution? Was the Ni bath made up at your facility? If so, was the highest purity nickel sulfamate concentrate added? I have seen similar problems with substandard Ni metal concentrates. I like to carbon polish before adding the leveler and wetter, just in case. If the deposit is semi-bright, how about the leveling and wetting agents? As you probably know the leveler controls morphology. Were the proper amounts added at make up? If you are running an engineered Ni bath, I would assume your anodes are bagged and bags are clean. Current density can play a role as well. In thicker deposits I have had better results with a low and slow approach. Are you getting adequate solution agitation using a 1 micron rated filter? Any time I went below 5, it choked the flowrate down to a bare minimum. I hope some of these suggestions will be helpful, let me know how you make out.
process engineer - Malone, New York
2006
Do a complete analysis of the bath and concentrate on the additives. Analysis of brighteners and stress reducers can be very difficult to do accurately, but when setting up a new bath, they are critical in getting the correct deposit. It would also be a good idea to check you structures by taking microsections. Nickel can be deposited with either lamellar or columnar structures; the difference is that lamellar ones are brighter and more reflective as they have horizontal layers; with columnar the deposit is vertical, so there are distinct vertical lines visible in a microsection. It is generally accepted that the lamellar structure offers less corrosion resistance than columnar. Many platers use duplex coatings where there is a columnar layer beneath a lamellar one. This offers better corrosion resistance than a simple lamellar structure. There is even a triple nickel structure that is claimed to give even better resistance than the duplex.
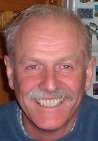
Trevor Crichton
R&D practical scientist
Chesham, Bucks, UK
2006
Q, A, or Comment on THIS thread -or- Start a NEW Thread