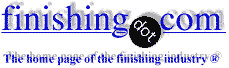
-----
Aluminum gas cylinder treatment
I need to clean the inside of an aluminum high-pressure gas cylinder to remove any grease deposited during the manufacturing process. I also need to remove the layer of aluminum oxide and any scratches, pits and other surface defects in order to prepare as smooth a surface as possible. Ideally I would like to do this with a chemical treatment only but information about other techniques would be useful. The inside of the cylinder is only accessible via the outlet which is approximately 27mm diameter.
Best regards
Preparation of high-pressure gas mixtures - Hampton, Middlesex, United Kingdom
2005
2005
Is this Al 6061-T6?
First, ensure that you are complying with all applicable manufacturing and inspection standards.
The following 2-stage cleaning is abridged from pages 33-34 of
"Luxfer's Guide To SCUBA Cylinder Inspection" www.luxfercylinders.com
--> Downloads.
Oil, grease, lubricants: Clean with a soapy solution (one tablespoon of liquid dish detergent per gallon of soft water). Rinse several times with tap water, twice with soft water, steam cleaner
⇦ on
eBay or
Amazon [affil link]
and blow dry.
Inspect the interior. Any material not removed by the soapy water washing and which impairs seeing the cylinder surface should be tumble cleaned.
Tumble the cylinder at 25 to 35 rpm for 10 minutes with a wet detergent + aluminum oxide chip combination (recipe given below). Empty cylinder (to reuse tumbling chips -- strain from the liquid and rinse). Rinse the cylinder well with warm soft water, then rinse with warm deionized water [if available]. Blow dry with warm, dry air or briefly steam dry the interior. Inspect. Repeat if necessary.
Tumbling solution: Add two to three cups of aluminum oxide tumbling chips to two quarts of soft water. Then add one teaspoon of a liquid dish washing detergent to the cylinder. Swirl or rock cylinder to mix.
Double the ingredients to make a gallon of the tumbling solution, as needed for large cylinders.
Do not shot blast or use any abrasive cleaning methods other than that above.
- Goleta, California

Rest in peace, Ken. Thank you for your hard work which the finishing world, and we at finishing.com, continue to benefit from.
2006
Ken,
Many thanks for the information. I have downloaded the Luxfer documents and found a source for the tumbling chips in the UK so I should be able to make some progress shortly. Although I predominantly deal with aluminium cylinders I may also have to prep mild steel cylinders, do you think that this treatment would also be suitable for polishing the inner surface of a mild steel cylinder?
Many thanks again for your reply, this is the first time I have posted to this board and it was great to get such a useful and quick response.
Happy New Year, Graham
- Teddington, Middlesex, United Kingdom
2006
For cleaning steel, a hot, alkaline detergent is appropriate (more effective than a warm, neutral solution). For oxide removal, include alkali-resistant (non-alumina) tumbling chips or a subsequent dry abrasive blast step. Although the latter seems like extra work, it precludes rusting during rinsing and blow drying. Follow immediately by blowing out with compressed dry air or nitrogen (dewpoint < -1 C) with a lance inserted nearly to the bottom of the inverted cylinder, then plug. For details and alternatives, see RR-C-901D
(Sect. 3.3) and MIL-STD-1411A (Para. 5.3), both available from ASSIST: http://assist1.daps.dla.mil/quicksearch/
Additional US info is in 49 CFR 178, subpart C (all cylinders), 49 CFR 178.37 (seamless 4130X steel, DOT 3AA) and 49 CFR 178.46
(aluminum, DOT 3AL). The enduse and any applicable CGA, ISO, EN, UK, etc. specifications should also be considered.
- Goleta, California

Rest in peace, Ken. Thank you for your hard work which the finishing world, and we at finishing.com, continue to benefit from.
Q, A, or Comment on THIS thread -or- Start a NEW Thread