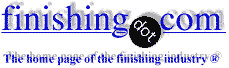
-----
1000 hrs salt spray
2005
Hi
I have some mild steel brackets that require 1000hrs salt spray resistance and have a black finish can anyone recommend a suitable finish.
Thanks in advance,
- East Yorkshire, England
Has been asked and answered several times in the last couple of years.
Do a search of this site's archives.
- Navarre, Florida
2005
Hi Richard
Go for Non cyanide alkaline Zinc-iron plating followed by trivalent black passivation and a top coat (sealant).there is test report available which crossed 1200 hrs SST red Rust. ...And it went on.(Test discontinued as the requirement was 1000 hrs RR)
Please use products from internationally reputed manufacturers.
Regards
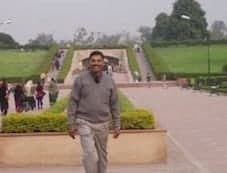
T.K. Mohan
plating process supplier - Mumbai, India
2005
This may be a litle extreme, but it works: 0.0007 to 0.001" of an electroless nickel, high phosphorus followed, by 0.0003-0.0004" bright electroless nickel using a solution that contains a divalent sulfur stabilizer such as Thiourea ⇦ on eBay or Amazon [affil link] . Then expose the deposit to 50-60% nitric acid for a few seconds (5-15 sec.)This will produce a durable black finish. The hi P EN will protect the basis metal provided there are no metal splinters and little or no porosity in the basis metal. If porosity is present increase the thickness of the first EN to 0.001-0.0015" The part must be covered 100% to protect.
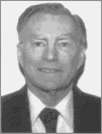
Don Baudrand
Consultant - Poulsbo, Washington
(Don is co-author of "Plating on Plastics" [on Amazon or AbeBooks affil links]
and "Plating ABS Plastics" [on Amazon or eBay or AbeBooks affil links])
2005
E-coat is the easiest/cheapest coating to provide that 1000hrs salt spray. We have passed as much as 3600 hrs salt spray, and 36 hrs of pure HCl submersion. We use a zinc phosphate pretreatment along with cathodic PPG e-coat process. The standard color for e-coat is black, it has a semi-gloss finish.
Adam Adkisson- Seminole, Oklahoma
2005
If you are speaking about red corrosion than it's better and cheaper to use Zn-Ni +black passivation+ sealing.
Efim Ruchman- Israel
2005
I won't dispute either Mr. Mohan or Mr. Adkisson. I'll only note that there are almost always other considerations besides corrosion resistance and color, and after those come out it will become clearer whether zinc-iron plating or electrocoating is the more appropriate process for your particular application.
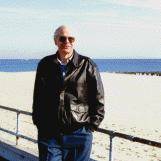
Ted Mooney, P.E.
Striving to live Aloha
(Ted can offer longterm or instant help)
finishing.com - Pine Beach, New Jersey
2005
Autophoresis - black, inexpensive, durable, corrosion resistant.
What is the application?
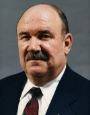
Daryl Spindler, CEF
decorative nickel-chrome plating - Greenbrier, Tennessee
2006
Q, A, or Comment on THIS thread -or- Start a NEW Thread