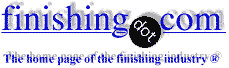
-----
Bending powder coated aluminum sheet/plate after coating
Q. I am having trouble with powder coat adhesion to aluminum after a post forming process (after painting). I am getting chipping paint in the area of the radius (about 1/16") that is formed. Aluminum is pre-treated, powder coat is medium gloss. I am looking for some QUICK HITS on what I should be looking into to get to the root cause of this chipping phenomenon.
Mer Adamsresearch for 1st tier auto - Grand Rapids, Michigan
2003
A. Hi Mer,
You should check the following things:
1. Was the paint applied to the proper thickness?
2. Was the paint cured according to spec?
3. Were the pretreatment baths operating according to spec?
You didn't say whether this was a chronic problem or a one-time incident. If it's a one-time incident, then something in the pretreatment or paint process is currently out of whack. If it's chronic, then maybe you have the wrong type of paint for post-forming.
George Gorecki- Naperville, Illinois
A. There are two tests that address your concern. Any reputable powder supplier should be aware of them.
1) Mandrel bend: This is a generic test to measure the flexibility of the coating in a mass production atmosphere. It is measured by the amount of film delamination (cracking) at 1/4" or 1/8" increments. This test equipment is readily available from BYK/Gardiner.
2) T-Bend: This is predominately used in the coil coating, blank and aluminum extrusion markets. There are different degrees of "T" with the ultimate being a full 180 degree bend w/out any cracking. This is rated at a Zero T. Again, any reputable powder manufacturer is aware of these tests, ask yours about it tomorrow.
Andy PealAutomotive Components - Grand Rapids, Michigan, USA
2003
A. What was the "pretreatment"? If chromate, it must be very thin under powder coat. If too thick the moisture in the gel will explode right thru the powder coat. If anodizing, then you are cracking it when you bend.
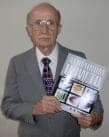
Robert H Probert
Robert H Probert Technical Services

Garner, North Carolina
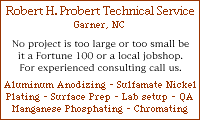
2003
Multiple threads merged: please forgive chronology errors and repetition 🙂
2005
Q. I am a consumer, not metal coating professional. I have read the editorial standards regarding such posts and searched the site for an hour or so to no avail. So now on with my questions, which I hope someone will find interesting enough to answer.
I am working with my church to build some custom designed acoustic absorber panels to install in our auditorium. The basic unit involves taking a 3' x 4' sheet of 1/16" thick perforated aluminum sheet and cold bending it into a half circle (or half cylinder) on about a 12 inch radius. Put another way, imagine taking an aluminum cylinder that is 4 feet tall and 24 inches round and slicing it down the middle lengthwise, so you have two half cylinders. The perforations consist of 1/8" diameter holes spaced 1/4" apart, giving an open area of about 23%.
For aesthetic reasons, we'd like the aluminum sheets to be white to match the walls where they will be hung. The manufacturers we have talked to have recommended powder coating. My questions are:
-Is this an appropriate coating given the application and substrate? These will be hung on the walls and ceiling out of reach of people, so they will not be bumped or touched.
-Will bending the sheets as I described after they are coated cause the coating to crack or wrinkle?
Thanks for your consideration
consumer/church volunteer - Cincinnati, Ohio, United States
A. Properly applied powder coating should last virtually forever in your application.
Problems are unlikely with such a large radius of curvature, but it is preferable to powder coat after bending.
- Goleta, California
2005
A. I believe you are in the clear, both ways.
If this is simple aluminum sheet it will have been anodized rather than plated (most likely).
If it has been plated bend it anyway, sand any flakes off and use a Rustoleum spray paint, it will bond to the metal and comes in a good flat white.
Blacksmith - Shiloh, North Carolina
2005
Q. I work for an aluminum extrusion company which also operates a powder coat line. Most of our powder coating is on lineals, but we have a few dies which our customer bends after we powder coat them. The powder coat is cracking and peeling at the bend. My question is, how much of a bend can there be before the powder coat fails? Also, does the rate of speed at which the part is bent contribute to failure? What about the mil thickness of the powder coat? We are getting up to 3.8 mil thickness depending on our supplier of powder coat. All of our tests (cross hatch, impact, MEK) are passing. Our titrations are good, wash stations good, temperatures and cure ovens are good.
Lori SlisherAluminum Extrusion/Powder Coat - South Bend, Indiana, USA
December 7, 2015
A. How about a few photos of failed components?
Certainly post-form powders have been around for a long time most obviously in the white goods industry.
These are, as I recall, usually Hybrid resin technology, thin film build powders ~1.5 mils (~40 Microns).
I have personal experience of tailoring line processes to achieve less than 2t bend radius on powdercoated steel.
Basically the metal failed prior to the powdercoated bond.
Photos would be very instructive.
Regards,
Bill
Trainer - Salamander Bay, Australia
Q, A, or Comment on THIS thread -or- Start a NEW Thread