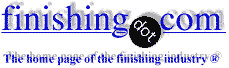
-----
Plating blisters barrel copper
Q. Can you help with a problem I have with blistering of zinc die cast components after barrel copper plating.the process is thus (1) soak clean 5 mins
(2)water rinse,
(3)acid neutralise 12 seconds,
(4) water rinse,
(5)copper plate 1 hour.
All cleaners and acids are new,but I am still ending up with blistering problems the strange thing is I have had good work out and bad work.The barrel rotation is also kept to a minimum.
Marcus Roberts- SHERWOOD, QUEENSLAND, AUSTRALIA
2005
A. Is it cyanide copper or pyrophosphate? Are you confident of the soak cleaner? Can you remove parts after the acid dip and verify waterbreak-free surface?
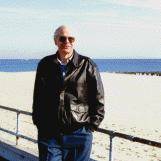
Ted Mooney, P.E.
Striving to live Aloha
(Ted can offer longterm or instant help)
finishing.com - Pine Beach, New Jersey
2005
Q. Cyanide copper --could not see any water breaks.
All parts are mass pre finished (vibrators) with a burnishing compound. could it be possible that the burnishing compound is not being removed by the soak cleaner even tho I would think that if there was a residue left on the surface that the cyanide copper plating solution would remove it, there is no electrocleaner in the line. The compound being used is of a proprietary nature so I am unsure what it is composed of. I have read the data sheet and do not know why we are actually using this as I don't see the need as we only really need to "knock" the flash off so as not to contaminate the nickel solution. It also mentions that, "care must be taken when using this product on zinc based castings". would value your opinion on this matter.
Marcus Roberts- Sherwood, Queensland, Australia
2005
A. Have you tried a copper strike solution prior to copper plate?
The type of bath is important. If the final plating solution is highly alkaline or acidic, the plating bath will begin etching the parts before covered with copper, and smut begins to form on the surface. This prevents a good plate. A strike solution uses very high current densities to deposit a thin coat quickly. The parts can then be plated normally.
It is especially difficult to plate die cast parts in a barrel because of the low current density in the inside of the mass.
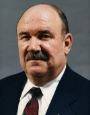
Daryl Spindler, CEF
decorative nickel-chrome plating - Greenbrier, Tennessee
2005
A. Marc,
Step 3 the acid neutralise you have mentioned.. what is it?
I feel the type of acid used to activate diecast after cleaning is important to prevent the formation of smut on the surface which can lead to blistering. Some companies sell acid salt mixtures which contain surfactants and are specifically designed for activating diecast.
- Melbourne, Vic, Australia
2005
A. It would really be helpful if you would list your entire finishing cycle.
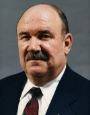
Daryl Spindler, CEF
decorative nickel-chrome plating - Greenbrier, Tennessee
2005
A. I may be old school , but I didn't notice a "desmut" in your process......its been years since I ran zinc diecast...but I tend to agree on trying a copper strike...
Ron Landretteplating equipment supplier - Bristol, Connecticut
2006

Q, A, or Comment on THIS thread -or- Start a NEW Thread