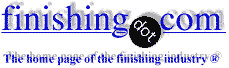
-----
Optimum Current Ramp for the Stamper Electroforming
Q. We are using a machine for our Nickel Electroforming process to make CD & DVD Stampers. We are using 240 mm glass master in the process. The operating bath parameters are optimum (pH-4.0, temp-55 degrees, boric acid-38g/l, Ni-80 g/l). What is the maximum current can be used in the plating to obtain a literally flat stamper? Right now we are plating at 65 amps with 70 Ah. We are using dye polymerised & nickel metallised glass master in the galvanising process. Due to delay of even 30s of the current from the rectifier the peeling of the metallised master get started. So, what is the optimum current ramp can be used for the plating with minimum stress suitable to our 240 mm glass master?
Pramod SabatEmployee - Mumbai, Maharashtra, India
2005
A. Maximum current actually depends on voltage. The limit on voltage is 20 vdc. If the cell is not kept clean; if the mesh is covered with Ni-sulphate residue; if the anode basket, and nickel anodes have not been cleaned and activated recently; if the anodes have started to become passive; if the work-holder needs maintenance; and/or if there are problems with head and motor, you will see higher voltage readings. Usually a safe setting is 90 amps. What voltage reading do you show, when you plate at 65 amps? If 15 or 16, try 70 amps; if 18 or 19, you might need to do some maintenance to your cells. Slowly work up in amps, 70 then 75, and then maybe 80, and record the voltages that you see, and look for any signs of stress. Dwight
Dwight Bancroft- Hempstead, New York
September 10, 2009
adv.: Supplier of Copper Anodes, Nickel Anodes, Bismuth Metal, & Other Metal Products for Industry & The Arts
Q, A, or Comment on THIS thread -or- Start a NEW Thread