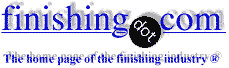
-----
Analysis of residual oil on metal stampings via oil soluble fluorescence
Q. We currently have a metal supplier using a heavy duty, chlorine free synthetic fluid for stamping/drawing steel for a particular part number. Our in-house process includes a 3-stage caustic cleaning step (KOH-based at 170 °F), rinses, H3PO4 acid pickle, post-pickle rinse, DI H2O final rinse and 2 step water-based coating. Standard processing of the subject part reveals poor water break, areas of spotty coating deposition, and poor x-hatch tape adhesion. we currently process 70+ additional part numbers from various suppliers without any issues.
We have completed additional process evaluations following secondary cleaning of the suspect parts, i.e. vapor degreasing prior to std processing. These evaluations have proven that a secondary cleaning method shows no sign of cleaning issues. Good water break, uniform coating, and excellent adhesion.
I have read that an oil-soluble fluorescence method exists to show residual oil on a cleaned part using UV light, but have been unable to locate a resource or vendor on the web. I would like to perform this test and include the data in my report to the metal supplier.
Does anyone have available information on the test method, sources for fluorescent oils, etc?
coating technologies - Huntington, Indiana USA
2005
Q. We are using vapor degreasing using TCE. Currently using copper sulphate
⇦ on
eBay or
Amazon [affil link] test to check for residual oil but it is destructive.
Want to use a simple UV light to check for oil on steel parts. Can it be done without use of a dye? Any harm using UV light with parts which might have some TCE (very low - though I believe it would evaporate).
Any alternate way to check the residual oil?
- Ahmedabad, Gujarat, India
August 6, 2012
A. Hi Abhishek,
It really depends what level of cleanliness you are looking for. The copper sulphate test on stainless steel is usually done as an effectiveness test for passivation, so probably isn't doing what you want it to.
The UV test will work for residual oils only if the oils fluoresce. A lot of oils do, but not all. You will need to check the oils that you are using and see if they fluoresce, if they do then it will be a valid test method. The UV will not damage any of your metallic parts.
We then have various water-break tests, but I feel that after vapor degreasing with trike and no alkaline clean they may not be the most reliable tests.
Getting to a very technical level you could carry out a non-volatile residue (NVR) and particulates tests (see ARP1176 from SAE for more details including several test methods) that are used for critical cleaning applications such as high pressure oxygen use or for parts for the space industry.
Aerospace - Yeovil, Somerset, UK
August 8, 2012
Thank you Brian,
Quite useful. Have ordered the UV and will give it a shot. Since the detection would be for common cutting oils & greases, believe it would be worth a try.
As far as the level of cleanliness go, our customers do not specify any but our processes down the line - shot blasting & phosphating would yield optimum results if minimal oil is carried through to them.
I will also research on the NVR - but I do need to order standards. If you have any recommendations in your mind, kindly suggest.
Appreciate your time and efforts to assist me with the response.
- Ahmedabad,Gujarat, India
August 9, 2012
A. Hi Abhishek,
This is from my perspective where some of the parts the company I work for are exposed to high pressure oxygen. Cleanliness is absolutely critical as explosive reactions with hydrocarbons is a real risk.
Cleaning prior to blasting and phosphate doesn't need the same level of cleanliness determination, so if I was you I would stick with the UV light inspection method.
For the records I use a rotary evaporator, a five decimal place balance and clean room conditions for equipment. The cleaned parts are then washed in a known volume of dichloromethane (also called methylene chloride), the solvent is then distilled off and the residual non-volatile residue determined by weight.
Aerospace - Yeovil, Somerset, UK
August 14, 2012
Q, A, or Comment on THIS thread -or- Start a NEW Thread