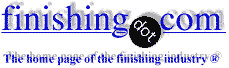
-----
How to do Magnetic Shielding on plastic
Does anyone have any info or know if a magnetic shielding can be put onto plastic parts of various shapes? Thank you,
Dan Storey- Fort Collins, Colorado
1999
There are a couple of ways to do this. As I understand it, Nickel is the material of choice for EMI shielding. We spray a nickel-rich paint that is manufactured by Acheson Colloids for this purpose. They also sell a variety of other coatings (e.g. copper, silver, graphite) that are suitable for EMI and RFI shielding. Their tech support may be able to help you choose the right material for your application. The other ways to come to the same result include electroless nickel plating and vacuum deposition. They are out of my area of expertise, but I'm sure others will elaborate. Mike
Michel Moninger- Sarasota, Florida
1999
We Have Done EMI and RFI shielding on plastic for a long time. We use a vacuum deposition type process.
Don Shadel- Wauseon, Ohio
1999
There are a number of ways to provide for EMI/RFI shielding on plastic parts; plating using electroless copper or nickel, shielding effectiveness is 65-120 dB, zinc arc spraying, 80-120 dB, cathode sputtering, 30-120 dB, vacuum metallizing, 30-129 dB, conductive paints using silver, 60-110 dB, nickel, 40-80 dB, and copper, 40-90 dB, foil application, 50-100 dB, conductive plastics, 30-60 dB, silver reduction, 90-120 dB. Additionally, I have seen metal shrouds configured to match the plastic parts. Many pros and cons to each method.
One company I worked for performed high volume EMI/RFI shielding on plastic and used zinc arc spraying and nickel or copper paints such as mentioned previously.
The conductivity tests used for QA inspection were ohms/sq and ohms point to point, with values defined by the OEM on the print. Shielding thickness does not reduce resistance in a linear fashion, the data collected at the time indicated a logarithmic relationship between thickness and resistance. I have a notebook of papers and if one wanted the references. For what it is worth, the type of coating which was the easiest from an environmental perspective, cleanup and ease of application using HVLP guns was a water based copper.. Frequently, we worked together with the designer, who would call out EMI/RFI coatings based upon aperture sizes in the plastic parts which affected the wavelengths of the radiation "leakage". Labor and production rates were affected by the quantity of maskers not by the applicators. Hope that helps.
Ward Barcafer, CEFaerospace - Wichita, Kansas
1999
Q, A, or Comment on THIS thread -or- Start a NEW Thread