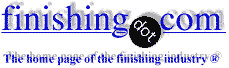
-----
Anodizing supervisor has a lot of questions
1999
I have recently been put in charge of a sulfuric anodize line. My knowledge on this subject is minimal. I have no hands on experience. I have a few questions for those in the know. basic questions that need answers.approve or not.
1. caustic etching -vs- acid etching.?
2. desmut.was a 50% 140 f nitric.....now is a 50% nitric with 16 oz gal ammonium bifluoride room temp.
3. anodize bath cathodes have heavy copper on them to the point it falls off in the solution. some say normal.some say bad news. bath temp 70 f and 15% by volume
4. the use of titanium racks . Have been advised that titanium creates a galvanic reaction in the black dye which causes pitting.better to use aluminum ?
5. constant current anodize -VS- voltage....should anodizing be done with a surface area and current density or is just running 15 volts for 35 minutes allright for black anodize.? so many questions. hope some one has the answers.
thank you ever so much in advance.
Todd Huehn- Blaine, Minnesota
First of two simultaneous responses--
1999Hi Todd,
Without knowing what your end product is and more about what you are trying to achieve it can be difficult to assist, however:
I used to run a jobbing sulfuric anodising plant in the UK that was generally accepted as being the biggest, (by volume) architectural quality producing jobbing plant in Europe. We were producing 750,000 square meters ( 8.1 million square feet) of architectural AA25 anodising per annum of which 65%+ was coloured using the Alcan anolok system. Because our work was 99% architectural the use of dyestuffs was considered unsuitable as we had to guarantee no colour loss on external exposure for 25 years. My comments therefore are biased to what I am familiar with and may therefore be of no use whatsoever.
Etching: I would personally always use caustic (after a hot aqueous soak /wash to remove the magnesium rich oxide layer in the aluminium,) in my opinion the surface finish from a final visual perspective is better. i.e. improved aesthetics.
De-smut: Why use nitric at all? I had perfectly satisfactory results using a sulfuric acid de-smut rather than Nitric. The majority of aluminium I processed was 6063 or 6060, different alloys however might well need nitric.
Cathodes: Recommend you change to Stainless Steel: With proper plant control and bath agitation we achieved, (over a 7.2 meter X 0.5 Meter X 1.25 Meter bath,) consistent film thickness control of ± 1.5 microns from the load average.
Titanium Racks: Sorry not much experience here, always used aluminium due to the Anolok process.
Constant current V's Constant Voltage: The expression "You pays your money and you takes your choice" springs to mind. If you are anodising loads of consistent size / geometric load density and area then constant current is the way forward. (You need to know your load size by area). If you are a jobbing shop doing bits and pieces with no two loads the same then stick to constant voltage, less chances of error.
Hope I was of some help.
Peter HirstSecond of two simultaneous responses--
1999I suppose no one has answered your questions because they require 5 totally unrelated answers. I'll try to answer them as briefly as I can.
(1)- For most applications alkaline etching is more economical and easier to control. Either etch bath consumes a lot of chemical and has aluminum salts accumulate in the bath. Both require frequent solution control and maintenance. When properly controlled, alkaline baths hold much more aluminum than acid baths, and require less frequent dumping. Acid etches almost always contain fluorides, which are the nastiest chemicals one would want to handle. The attack of fluoride-containing etches is quite exothermic, and production baths frequently need cooling. Acid etches are usually used only for special applications, such as etching high silicon alloys or achieving a matte finish on some wrought alloys which don't easily attain a matte finish in an alkaline etch.
(2) Hot nitric acid is right up near the top of the "nastiest chemicals" list and very unnecessary. Adding fluoride as you have done helps, but you essentially have an acid etch bath similar to that discussed in #1. You can't leave parts in it too long or you will etch the parts and consume fluoride and acid. At that high concentration of nitric, control is a big problem, as you probably have to decant a portion of the bath in order to replenish to bring back the acid content to 50%. Proprietary baths, based on ferric sulphate or peroxide and which usually operate at 5-10% concentrations, are much easier and more economical to operate and control, and much easier on your waste treatment system.
(3) Copper in the anodizing bath can be bad for corrosion resistance. Anodizing is a plating tank in reverse, so the copper plates out. Attach aluminum or stainless sheets to your cathodes, allow the copper to plate out during processing, and remove the sheets to remove the copper. If you don't leave them in too long you can remove them without losing much copper, which, if it falls back in the tank, redissolves. But you must find the source of the copper and correct that problem. Unless you run high copper alloys exclusively, you may be dissolving buss bars or someone is using brass bolts.
(4) Galvanic problems with Ti racking mostly occur with high copper alloys. If aluminum racks are objectionable, add magnesium bars to your racks after anodizing.
(5) Constant current anodizing is highly recommended by the "experts" for consistent quality anodizing. My experience has been that constant voltage works O.K if sequential loads have the same parts with the same number of parts per rack. The time and voltage you ask about are good for some alloys, but may not be for other alloys. You must also consider the temperature and acid content of the bath.
Your questions are not really basic, as you indicated, (otherwise you would have had some quicker answers) but they would be to basic to one familiar with the operation of the anodizing process. I would highly recommend that you get educated in a hurry by purchasing books on anodizing, take an AESF or ASM course, and/or read all the questions in the archives of this site and others.
Phil Johnson
- Madison Heights, Michigan
question for Phil Johnson :
can you give some more details about baths based on ferric sulphate and peroxide ?
We have problems with Silicon Smut
Pierre RAES- BELGIUM
2000
Smut from etch baths is, of course, alloying elements and their oxides which are insoluble in an etch bath (usually alkaline etches, but acid etches can cause some smut, too). That smut is dissolved either by a strong acid, or through a mechanism called oxidation-reduction (some use the abbreviation "redox"). Without getting into a full-fledged chemistry lesson here, the ferric iron or peroxide are reduced, that is gain electrons, while the metallic or oxide smut particles are oxidized, that is lose electrons to produce metallic ions, which are acid soluble. Nitric acid has some redox capability, but only when the acid is concentrated. The ferric sulphate or peroxide have a much higher redox potential, meaning that they perform well and desmut as dilute solutions.
Unfortunately, there is one popular alloying element which doesn't readily solubilize with the above mechanism, and that is silicon. With alloys such as 6061, which has a relatively small amount of silicon, the silicon will often lift off with other smut particles, and desmutting is relatively fast. For higher amounts of silicon or for heavily smutted 6061 the bath needs fluoride to dissolve the silicon. Most proprietary desmuts have a small amount of fluoride built into them for that reason. For 4000 series or for cast alloys with 4-12% silicon, a deoxidizer similar to the nitric/HF acid mixture, such as the acidic etch previously discussed, is needed. This can't be said too many times: HF or acidic solutions containing fluorides are very dangerous chemicals, and should be handled only by those trained to do so.
Phil Johnson
- Madison Heights, Michigan
2000
Q. SIR ,
MANY MANY THANKS FOR YOUR COMMENT, NOW I WANT TO KNOW WHY THE PITTING PROBLEM ARISE, WHAT THE MAIN FACTOR BEHIND THIS. SECONDLY IN FLUORIDE TREATMENT BATH WHAT IS THE IDEAL RATIO IN BETWEEN NITRIC ACID & ADDITIVE. WHAT IS THE ROLE OF ALUMINIUM FLUORIDE, HOW WE CAN CALCULATE THE VALUE OF IT IN FLUORIDE BATH.
Thanks
- India
October 26, 2012
Q, A, or Comment on THIS thread -or- Start a NEW Thread