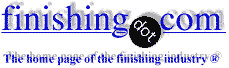
-----
Poor paint adhesion on galvanised surface
Q. Poor paint adhesion on galvanised iron steel! We have three pretreatment tanks before coating, there are degreasing, chromating and passivating. Poor paint adhesion is it because of chromating not proper done? What are the major reasons which cause the paint peel off from the galvanised iron steel. Any suggestion? Thank you
ming [last name deleted for privacy by Editor]- Sarawak, Malaysia
1999
A. Hi Ming, A procedure I would follow would be to degrease only if necessary followed by copious rinsing.
Secondly try cold phosphating with a mild Zinc phosphate solution instead of passivation.
Follow with adequate rinsing and direct painting or powder coating. You may try to Chromate dip the phosphated Zinc if you wish but as long as you preheat the parts well before painting the parts, you should have no problem. Please note that the galvanised Zinc will turn dark grey to black when you phosphate but that should not worry you!
Regards,
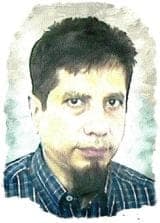
Khozem Vahaanwala
Saify Ind

Bengaluru, Karnataka, India
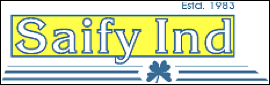
1999
Ed. note: See our FAQ Prepping Galvanized Surfaces for Painting
A. Perhaps you are using the wrong coating for your product. There are a few good waterborne polyurethanes available that do not require a passivation process or work well with it. Pete.
Pete Bagley- Reno, Nevada
1999
Thanks Pete. Are they reported to help address this particular problem of poor adhesion to galvanised surfaces? Thanks.
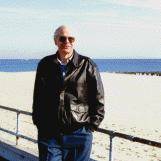
Ted Mooney, P.E.
Striving to live Aloha
(Ted can offer longterm or instant help)
finishing.com - Pine Beach, New Jersey
1999
Ming and Ted, There are so many variables to successful galvanized steel coating that it impossible to definitely subscribe to one single coating. However it has been my experience, and the success of my colleagues in the U.K., Turkey, Australia and Canada, that a cross-linked waterborne polyurethane applied to a similar prepared galvanized surface has lasted for more than 10 years without peeling and with less than 25% gloss reduction. Perhaps Ming would do some diligent testing with a similar product to provide us all with real performance data. Since waterborne coating technology is advancing so fast in our industry, we are definitely lacking in engineering data in order to support its usefulness. The timing could not be better with the demands of meeting reduced VOC content and the concern for environmental emissions from non-compliant products that our industry faces today and must meet tomorrow.
Pete Bagley- Reno, Nevada
1999
1999
Hi Ming,
I hope I can assist you with your problem. I think I posted an explanation similar to this some time ago but things sometimes are difficult to locate on the Web.
You say your process is "degreasing, chromating and passivating". I am a little confused about chromating, then passivating. You do not mention any rinses.
My main experience with this type of problem is with powder coatings but I am certain the explanation is relevant to wet paint systems.
When a steel surface is galvanized, it immediately begins to corrode. Galvanizers don't like this, so to reduce the incidence of corrosion and to diminish the possibility of storage corrosion, they like to quench the galvanized part in a dilute potassium dichromate solution or similar. Now this chromate is not suitable for powder coating causing adhesion problems if not removed. It probably will give adhesion problems for painters as well. If the galvanizer knows an item is to be powder coated they can be convinced to not quench it in the chromate solution. If the chromate has been applied, it can be removed in a medium alkali degreaser.
The surface of the zinc begins to corrode immediately it is produced. Often, the first signs of this are small black spots that are difficult to see with the naked eye. Under magnification one would see a small white spot in the center of these black spots. This white material is a zinc corrosion product that contains moisture. As the zinc surface ages, then more and more corrosion product is formed and eventually a white stain can be seen (without magnification) on the surface of the item. These corrosion products are not adherent to the galvanized surface and if not removed will give adhesion problems after painting. Beneath the stain, there are shallow small pits in the galvanized surface; the depth of which depends on the severity of the corrosion. These pits are full of damp zinc corrosion products.
The white surface material may be removed mechanically, but the material in the pits will not be removed by wire brushing. It has to be dissolved out with acid. If not removed the product may give rise to pin holing - if heat curing is used, but will give rise to a lack of adhesion whether room temperature cured or heat cured.
I suggest the following:
Degrease if oils or greases are present.
Rinse well
Wire brush the surface if a white stain can be seen
Etch in an aluminium etch or 5-10% phosphoric acid.
Rinse very well
Chromate
Rinse well
DI rinse
Dry
Paint or powder coat.
Some applicators also preheat the item after chromating and rinsing to ensure all the moisture in the pits has been removed. Since you are chromating, you should not exceed 65 °C for this preheat as the chromate will be adversely affected so the preheat would need to be done for a protracted period of time.
Rather than chromate I would suggest an alkali metal phosphate if the parts were for interior use and a zinc phosphate if for exterior application. Then you can preheat at a much higher temperature.
I hope this helps. If not let me know and I will try again.
Mario S Pennisi- QUEENSLAND, AUSTRALIA
A. Do yourself a favor and neglect all the advice about chromating if you value your life and the life of your fellow men.
Nowadays it is quite easy: clean the surface with a cheap thinner and a cloth and paint it with an ACTIVE paint (for example any epoxy paint) that allows the continuous interaction between the zinc coating and the CO2 (we call it breathing) which actually causes paint not to stick to hot dip galvanized surfaces.
Regards,
- Jakarta, Indonesia
2007
We're appreciate your input, Budi! But I think most of the responders recommended phosphatizing rather than chromating; and it's hard to see the environmental benefit of using solvents like "cheap thinner" in place of phosphatizing -- not to mention that the phosphatizing probably works better on galvanizing than "solvent wiping", just as it does on bare steel :-)
I'm not familiar with this concept of "active paint", but it sounds interesting, so thank you for alerting us to the idea. We have to keep striving for improvement, but galvanized finishes often last 75 years without maintenance, and numerous finishes that outperform it in accelerated testing don't hold a candle to it in the real world, making it difficult to predict what will be an improvement :-(
Thanks againn.
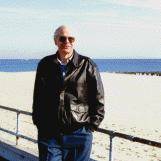
Ted Mooney, P.E.
Striving to live Aloha
(Ted can offer longterm or instant help)
finishing.com - Pine Beach, New Jersey
Q, A, or Comment on THIS thread -or- Start a NEW Thread