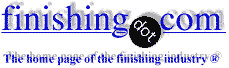
-----
Etching / pickling Inco 718 (Inconel)?
Current question and answers:
Q. Wondering if anyone can help me with a perplexing phenomena. We have this 718 nickel part and we EDM a slot on one end. After that it went to chemical clean in preparation for welding. The chem clean was a nitric acid/Turco Nitrad bath, 120 °F for 20 minutes. The area around the EDM cut turned dark gray. I ran it through EDS analysis on our SEM and didn't pick up any foreign contaminates or oxides. We scotch-brited the discoloration off and ran it through the bath again and the same thing happened. Is it possible, although I find it hard to believe, that the electrical discharge machining somehow changed some characteristic of the material around the area so it reacts differently in the pickle? This makes no sense to me at all. Any theories would be appreciated.
Tino Volpe- Sharon Massachusetts
October 26, 2020
A. Big disclaimer, as I've got no experience running that particular process...
However, I've got plenty of headaches taking in EDM jobs (in my case, stainless steel destined for passivation) and having to explain to the customer that the surface left after EDM is essentially a casting, and must be treated as such. I've operated EDMs and my takeaway is that, while they are a brilliant evolution in metal-cutting, and as last resort can work milling miracles, they are too often simply used as a time-saver at the expense of an easily plateable surface finish, and it's the finishers who bear the headaches!
The re-cast layer left after EDM will never interact with the finishing operation in quite the same manner as a cleaner milled finish. Wire EDM in a DI electrolyte is marginally easier to troubleshoot than sinker EDM in oil, simply due to the additional hydrocarbon residue that needs to be cleaned off.
I would start looking at pretreatments intended for castings entering your process. Hopefully someone with more specific experience will chime in.
Cheers and best of luck!
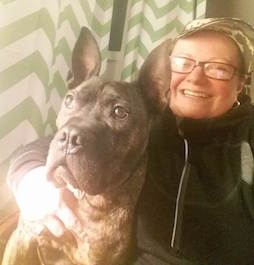
Rachel Mackintosh
lab rat - Greenfield, Vermont
November 5, 2020
Rachel,
Thank you for that response. I get it that the EDM'd surface is basically a casting, however what I find most puzzling is that it's the machined surface around the EDM'd surface that discolored, not the actual EDM surface itself. That is what is throwing me.
- Sharon Massachusetts
November 5, 2020
⇩ Related postings, oldest first ⇩
2002
Q. I have a problem in etching the Inconel 718 alloy strip as pretreatment for plating. Pretreatment consists of degreasing, pre-etch in HNO3/HF/H2O, electroclean in Na3PO4/Na2CO3/NaOH, and etching in sulfuric acid.
Problem is occurrence of smut after etching in sulfuric acid solution with current density of about 5 A/dm2. This etching condition worked well up to now for the bright annealed material condition. But, for the material having thin oxide about 500 Angstrom, the etching exhibited black residue on the surface. Titanium and Niobium was excessively found in the smut location by EDS analysis.
Questions:
1. the probable cause of smut occurrence (oxide?)
2. identity of the smut (phase, composition)
3. alternate etching method (or solution) preventing from occurring the smut
Thanks for everyone interested in my letters.
- Korea
Macroetching Inconel 718
Q. I have a problem with macro etching INCO 718. I tried many Etchants, but without success. If somebody has experience, write urgently.
Please advise!
University of West Bohemia in Pilsen - Pilsen, Czech Republic
2005
----
Ed. note: Hi, Radka. If your need help "urgently", please retain consulting services. You'll usually get pretty good answers in this public forum eventually, but knowledgable readers wander in and out over weeks and months, there is no summoning them. Best of luck.
A. Try www.kaker.com website! Good luck!
Solution no 2: try www.metallography.com website.They have ask experts forum! Good luck!
- Cerovski vrh Croatia
2005
A. There are a lot of definitions for macro etch. What are you trying to do? Is this on a part or a microsection?
James Watts- Navarre, Florida
2005
2005
A. You can try the following mixes:
70% by vol HCl
3% by vol HNO3
27% by vol Be 42 FeCl3 sol
at ambient
You can also use :
90% by vol of Be 42 FeCl3 sol
10% by vol HCl
at 110F to 120F
- Paramount, California, USA
A. If all else fails you can try a mix of HCl and Peroxide in a well ventilated area. The proportions change based on your concentration but I've found that an 80/20 mix of ~20%HCL (pool acid here in AZ) and 30% H2O2 works well. The mixture can be used at room temperature. If you use lab grade acid cut waaaay back on the H2O2 or the reaction becomes very violent (boiling out of the container).
I would suggest submerging the part in the desired amount of acid (whatever concentration) and then slowly add the peroxide until a reaction occurs. The desired mix will result in a reaction that gradually speeds up to a rapid evolution of small bubbles (think freshly poured ginger ale). The reaction will peak and then stop. More oxidizer can be added at this point if the part isn't sufficiently etched. I've used this etchant on a range of alloys and superalloys and it works well for macroetching for grain size.
A few words of warning though...
This etchant is very aggressive and can induce IGA so I wouldn't advise it if you intend to do any metallography after etching (which I wouldn't advise anyway). Secondly this reaction puts off a lot of noxious fumes and should be done in a hood. As mentioned before the etchant is aggressive and as a result the etching time is usually just a few seconds. The possibility of over-etching is fairly high.
- Phoenix, Arizona, USA
November 24, 2008
A. Depends on how big of a sample. If you have a sample small enough to fit in a casserole dish, use a hot plate. Use HCl straight about 55 to 60 °C for about 10 min. When it is pulled out it might be blackened -- drop in a full tub of warm water, drain water, as water is draining pour 20% nitric acid on sample and scrub softly with a soft bristle brush: that should etch; if not then I have been doing this wrong for the past 7 yrs.
Beto Godina- tomball, Texas usa
October 5, 2011
Etchant for Inconel 718 after welding and heat treatment
Q. I need to know what are the suitable etchants for Inconel 718 (compressor blades) after a welding and heat treatment (760 °C). The purpose is to investigate bluish color that appears after heat treatment process is conducted.
Farah Ismailprocess engineer - Kuala Lumpur, Malaysia
May 18, 2009
A. Since you say "turbine" you really need to follow the OEM's procedures as some allow different chemicals than others do.
Nitric acid with a bit of ammonium bifluoride works very well, but some companies do not allow it. Do not use HCl (muriatic acid) which no one allows.
A better way is to use a vacuum furnace or a furnace with a slight reducing atmosphere.
Your blue is simply oxidation of some of the metals in the alloy and surface contamination. The parts need to be clean and dry before going into the oven.
- Navarre, Florida
May 19, 2009
A. I am assuming that these are jet engine compressor blades; you probably want something which will not render them useless.
GE standard practice manual has a section 70-24-00 which deals with preparation and use of various etches for engine components. This will cover an etch solution for Inconel 718.
Aerospace - South Wales, UK
May 21, 2009
Q, A, or Comment on THIS thread -or- Start a NEW Thread