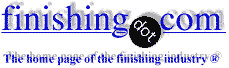
-----
City water dept. finds 316 SS Butterfly valves rusting
Q. We in our water department encounter a new problem with a stainless steel butterfly valve used in the process air line. All valves 10 " and less 316 SS Valves are corroding and valves 12" and above are not corroding and also all the corroded valves are not attracting the magnet and others not. SS valves are not suppose to attract magnet.These valves are cast based on "CF8M" process. Can anyone help me why these 316 SS(CF8M) valves are corroding? Other valves are attracting the magnet why?
Thanks
Vinu VarugheseFailure analysis - Philadelphia, Pennsylvania
2005
2005
A. CF8M is the casting alloy that corresponds to the wrought 316 material. It has slightly different chemical composition, which has several consequences.
1. Foundries usually balance the relative amounts of the various elements (while maintaining each within its own specified range) so that the microstructure is predominantly austenitic, but with typically 5-8 percent ferrite. The ferrite phase is attracted to a magnet (if it is present to say 5% of the structure, the strength of the attraction will be in the vicinity of 5% of that of mild steel). It is by no means essential to induce this small amount of ferrite, and indeed the CF8M composition can be balanced so that there is no ferrite and hence no magnetic attraction, but knowledgeable foundries do not do this unless these is a special need for low magnetic permeability that was specified by the purchaser. The wrought 316 has its composition deliberately balanced so that ferrite does not form, because it is much easier to roll the material into its final form (plate or strip) if there is no ferrite in the microstructure.
2. A consequence of the ferrite is an increase in strength during and immediately after solidification, which greatly reduces the possibility of hot-tear defects occurring which would require subsequent repair by the foundry - such a repair would not detract from the integrity of the component, but is an avoidable additional manufacturing cost. So the ferrite is induced to give this protection against hot tearing.
3. An incidental benefit is that the room temperature yield strength is increased, although this benefit is rarely exploited by design engineers.
4. An incidental benefit is enhanced corrosion resistance, because the chromium specification range for CF8M is higher than that for 316, and furthermore it is usual to manufacture CF8M towards the top end of its chromium range as part of the ferrite-inducing element balance but to manufacture 316 towards the bottom end of its chromium range as part of the ferrite-avoiding element balance. The higher chromium content of CF8M confers better corrosion resistance.
5. All of the above relies on the manufacturer heat treating the product appropriately, so as to avoid the presence of any of carbides, or sigma phase, or chi phase, in the microstructure because any of these will detract from corrosion resistance.
Additional note: Having written the above, it now occurs to me that perhaps you are referring only to rust on visible external surfaces of the valves, and not to corrosion on internal surfaces. If that is the case, it is possible that a manufacturer shot-blasted the castings with steel shot rather than stainless shot, thus contaminating the surface with non-stainless debris. There are many postings on this site that refer to pickling (or passivation) to clean such contamination from stainless surfaces.
You need to talk with the suppliers of the valves to clarify their manufacturing procedures. Bear in mind that any one particular valve supplier might source his component castings from different foundries, so even if you are only using one valve supplier you might have castings from several different manufacturers, and some might be using better procedures than others.
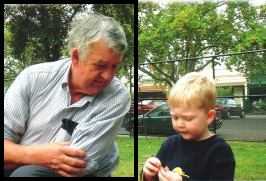
Bill Reynolds [deceased]
consultant metallurgist - Ballarat, Victoria, Australia
We sadly relate the news that Bill passed away on Jan. 29, 2010.
Q. It is true that the rust is visible only on the visible external surface. Is it common? Can you please explain me the difference between steel shot blasted and stainless shot blasted? And how does this affect surface rusting as shown in the picture?
Vinu Varughese [returning]- Philadelphia, Pennsylvania
2005
![]() |
2005 A. Aha! It becomes clearer. When your original query downloaded, only the first of what I now know to be two photographs appeared on my monitor. Some glitch in the web site or my browser, I guess. So I saw no rust on the outside of the valve. But now, two photographs download and the second one makes it clear that many of the points I made in my original response, while correct, don't apply to your case. ![]() Bill Reynolds [deceased] consultant metallurgist - Ballarat, Victoria, Australia We sadly relate the news that Bill passed away on Jan. 29, 2010. Ed. note: Sorry, Bill, we originally displayed the pictures with the good one on the left. I think readers didn't realize that there was another picture off to the right, out of the field of view on some screens. 2005 Thank you Bill for the best description of the CF8M process I have seen. ![]() ![]() Lee Kremer Stellar Solutions, Inc. ![]() McHenry, Illinois ![]() |
A. Vinu,
Regarding the rust on outside of 316 castings, This can be caused from blasting with steel shot. Where the steel becomes embedded in surface. If no further machining is done, then this embedded iron will rust over time. For internal surfaces which are most likely machined after casting + blast cleaning, the embedded iron would be removed.
There are stainless steel shots and stainless steel cut wire shots available, which will prevent embedding of Free iron in the first place. The next time a unit rusting in the field is removed, have it sectioned + evaluated metallurgically for the depth of rust, and give you peace of mind for other units in service are ok. You will then be able to confirm if rust is limited to as cast surfaces.
North Tonawanda, New York
2005
Q. Another question is that the non rusted valve does attract the magnet and the rusted one does not attract the magnet. Both of them are CF8M casting material. Is this because CF8M is usually made with its chemistry balanced to give 3 to 8 % ferrite, which is magnetic in the microstructure? I assume that 3% ferrite is less magnetic and 8% ferrite is more magnetic. Thanks
Steel shot contamination for SS valve. This is with reference to the letter no 37534 at finishing.com. Thank you very much for the excellent description about CF8M material. Our valve under question is in service. Is there any way that I can prove that the foundry used steel shot rather than stainless steel shot when this is in use now. Is testing with copper sulphate ⇦ on eBay or Amazon [affil link] solution as described in ASTM A380 give us some results if there is any contaminant? Is there any way to test the air in the area?
Vinu Varughese [returning]Philadelphia Water Dept - Philadelphia, Pennsylvania
2005
A. Vinu,
I've just about reached the point where I'd need to write a book to take the whole matter further, because there are so many combinations of possible variations in processing details during manufacture, and they are all just that ... possibilities.
Even if the surface was contaminated by non-stainless steel, that doesn't constitute non-compliance with ASTM material specifications than include CF8M, and I suspect that your organization didn't set out any requirements on the subject.
If you really want to know what has caused the rust, you need to take the valve out of service and submit it to a metallurgical lab for investigation.
But my best advice now is to try Lee Kramer's clean-up if you don't like the look of the rust, then print this whole thread and give it to your valve supplier with a request that they don't let it happen again.
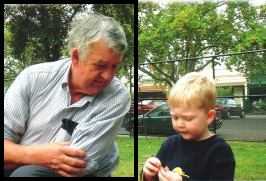
Bill Reynolds [deceased]
consultant metallurgist - Ballarat, Victoria, Australia
We sadly relate the news that Bill passed away on Jan. 29, 2010.
2005
Q. How to determine the cast is pickled or not. We have some valve in service which is corroded on the outside surface. We were told that this may be due to the absence of proper pickling after the casting process. Is there any method other than copper sulphate spot test to determine the casting is properly pickled or not?. I already performed copper sulphate spot test. Thanks
Vinu Varughese [returning]Philadelphia Water Dept - Philadelphia, Pennsylvania
2005
A. My final post on this thread.
In general terms:
Pickling is only needed if the castings are blasted with steel or iron abrasive, thus contaminating the surface. If they are blasted with stainless shot or garnet, there is no need to pickle them afterwards but no harm is done if in fact they are pickled.
For your castings:
If they are NOT rusting, either (1) they were blasted with an appropriate abrasive and might or might not have subsequently been pickled, or (2) they were blasted with an inappropriate abrasive and were subsequently correctly pickled. It doesn't matter which, because they're not rusting and that's what you want.
If they ARE rusting, there are multiple possible causes, including (but not limited to) any one of, or combination of: inappropriate abrasive and subsequent pickling, inappropriate element balance within specification, incorrect heat treatment, composition out-of-specification, unsuitable specification in the first place. Examination by a metallurgical laboratory would be needed to determine the actual cause(s) in a particular case. I'd give you a price myself to do the investigation, but you're in USA and I'm in Australia so it really wouldn't work.
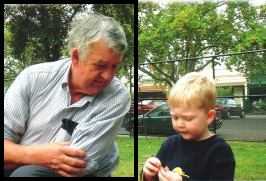
Bill Reynolds [deceased]
consultant metallurgist - Ballarat, Victoria, Australia
We sadly relate the news that Bill passed away on Jan. 29, 2010.
2005
CF8M (316) surface rust on face of parts facing road
Q. Before winter we supplied some CF8M "posts" for building entrance protection (9/11....). We cast them and sold them here in Boston. I just got a call saying that the side facing the road is rusting. I have yet to take a ride over there but I was wondering if you guys have any input? The parts have been heat treated and passivated. Keep in mind that last winter was about the worst in history for us.
Thanks in advance.
Foundry - Braintree, Massachusetts
2005
A. Check out the moly percentage,
K.Ravikumar- India
2007
Q. I am in the process of choosing between industrial hose fittings. One is made of CF8M with investment casting versus 316SS.
My understanding of the above is that both CF8M and 316SS are made from the same alloy but that there is a difference is in the forming process.
If this is the case should CF8M AND 316SS products have the same chemical resistance various fluids/acids, etc.
INDUSTRIAL FITTINGS - SCARBOROUGH, ONTARIO, CANADA
April 25, 2008
A. The first thing to ask of the 316 valve casting is what casting process was used. Sand casting or investment casting. Looking at the picture it looks like a sand casting! This would be the start of the rusting problem!
In sand casting, particles of sand are attached to the surface of the SS and leave pockets on the surface when removed with grit or sand blasting method. In these pockets will hold contaminations and cause rusting. In passivation or pickling the solution is tied up in these pockets and dried and when exposed to moisture again rusting will seem to come from these pockets in the SS surface. If the surface is machined to remove a thin layer you remove these pockets and remove this problem.
The grit blasting with steel will cause this rusting but what casting house would use steel shot blast on SS casting?
- Ontario, Canada
June 10, 2009
Q. Why CF8M castings are rusted when it is exposed to open atmosphere for long time.
Omkar KshirsagarStudent - India
September 10, 2009
September 10, 2009
A. Hi, Omkar. As you can see, we appended your inquiry to a thread that hopefully answers it. If you have remaining questions, please post again.
Regards,
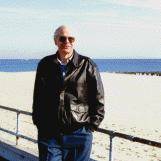
Ted Mooney, P.E.
Striving to live Aloha
(Ted can offer longterm or instant help)
finishing.com - Pine Beach, New Jersey
"Rustiness on CF8M material after water testing"
September 19, 2017Q. Rust appeared on the CF8M material after assembly testing (hydrapress measurement); after 1 week we found the rust appeared on casting surface.
The part was produced by resin sand process.
which process should be investigated with regard to this condition?
1. quenching process
2. solution heat treatment and acid cleaning passivation?
3. chemical composition? Cr content?
Do we have a standard for checking the corrosion such as a salt spray test?
Kevin Kong
- Qingdao China
this text gets replaced with bannerText
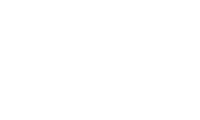
Q, A, or Comment on THIS thread -or- Start a NEW Thread