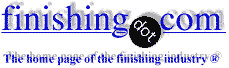
-----
Issues involved in continuous reel-to-reel coil anodizing of aluminum
Q. Is there a table that shows maximum Sheet Aluminum sizes for color continuity / uniformity for anodize Type II Class II?
John Pharr- Minneapolis, Minnesota
January 5, 2022
A. Hi John. From some quick browsing it looks like 48" or 1250 mm is not uncommon. Wider sounds possible, of course, but you would probably have to inquire of various coil anodizers. I doubt that you'll find a table of that sort.
Luck & Regards,
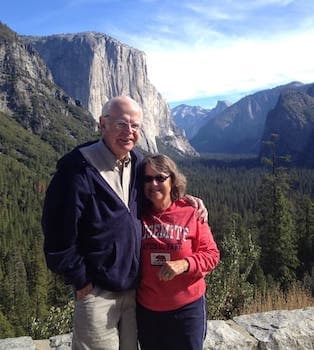
Ted Mooney, P.E. RET
Striving to live Aloha
(Ted can offer longterm or instant help)
finishing.com - Pine Beach, New Jersey
⇩ Related postings, oldest first ⇩
Q. I am looking for a bibliography about pre-anodized aluminium coils. I am looking for studies about the process of continuous anodizing of aluminium.
Thanks,
Mario Bartolomei- Lucca, Italy
Q. Dear Sirs,
Is it possible to do continuous anodizing for aluminum special profiles (such as squares, rods, etc.) with length about 16 m at one stage.Is it done in the world?
Best Regards,
plating shop employee - Tehran, Iran
February 4, 2008
A. Specialized continuous anodizing of sheet aluminum for lithography and for manufacturing of electrolytic capacitors is done ... in addition to coil anodizing for roofing, siding, and decorative applications, Shapour. So continuous anodizing of extruded shapes should present no electrochemical problems.
But a general feature of continuous processing is that the material is wound onto a pickup reel -- which may present plenty of mechanical issues to be resolved.
When you say "length about 16 m" though, it doesn't sound like you're assigning quite the same meaning to "continuous" as I am, so I'm not sure we're envisioning the same thing. Good luck.
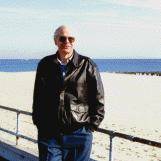
Ted Mooney, P.E.
Striving to live Aloha
(Ted can offer longterm or instant help)
finishing.com - Pine Beach, New Jersey
Q. I make a product that involves the anodization of a continuous web of aluminum. During the course of an anodization run, I see non-linear monotonic fluctuations in my power supply. For example, If I hold the current constant, the voltage will decrease in a non-linear fashion. Conversely, if I hold the Voltage, the current gradually increases.
I am new to the anodization world; is this behavior typical? Could it be temperature dependent? (I'm guessing no, because we control our bath temp fairly well) Is it due to local regions that are "ionically stagnant" in the bath? If so, how can this be disrupted?
I ask because I'm seeing a drift in one of my product quality variables, and this drift in my power supply may be the source.
electronics materials - Minneapolis, Minnesota, US
2005
A. I am not familiar with continuous feed anodizing, but I would expect some wild variations when first starting and when ending, but if the feed rate is constant and the area is constant, then either the amperage or voltage should also be a relative constant.
As aluminum anodizes, it forms an insulator so will pull less amperage at a given voltage. Since you are constantly feeding in non-anodized material, it will pull a huge amperage for a given voltage. BUT, it should reach a nominal value.
My guess is that the feed rate is not constant or the area is variable or your contact points are dirty and the new material is periodically tearing the dirt off.
Not being able to see it in operation and doing some other checks makes it difficult to give a real good answer.
- Navarre, Florida
A. I do not know what a "continuous web" is, but it seems you are not getting the current on the part. If the web members are too thin you may be anodizing all the way through and then the current cannot conduct through to the rest of the web. Otherwise you just need to make contact in more places, closer together. Be aware that titanium is a very poor conductor and may not be delivering enough current to your "web" (whatever that is). Try using all aluminum racking and contacts.
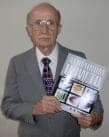
Robert H Probert
Robert H Probert Technical Services

Garner, North Carolina
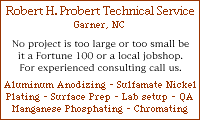
Thanks, Robert. When materials are processed as continuous sheets or foils, we in the metal finishing industry tend to call it "reel-to-reel" or "continuous coil", but in other industries it's commonly called "web processing". So if you picture aluminum foil continuously coming off of a large spool and being anodized then wound onto another spool, I think that's physically what Marty is referring to. Before the miniaturization of electronics, large electrolytic capacitors were a commonplace (the aluminum 'cans' they warned you not to touch in TVs), and I saw continuous anodizing lines for anodizing aluminum for them. A similar process is used to make aluminum lithographic plates.
Hi, Marty. The same principals apply as in rack anodizing, that the resistance of bare aluminum is very low and the resistance of fully anodized aluminum is very high. Since the aluminum "web" is all one piece, you can't control the anodic pole; you need to have separate cathodes and rectifiers so that you can apply low voltage at first and gradually increase it as a particular spot on the coil begins building an anodized thickness.
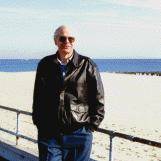
Ted Mooney, P.E.
Striving to live Aloha
(Ted can offer longterm or instant help)
finishing.com - Pine Beach, New Jersey
Q. Yes, Ted, we process a spool of aluminum (0.3 mil) laminated over a poly backing (2 mil). We do control the web speed, so there is always a fresh supply of metal entering the tank at a constant rate.
The web passes over an anode roller (metal side contact, of course), then travels into our electrolyte bath where it passes the stationary cathode. The bath is recirculated, filtered, and cooled.
The temperature does drift up during the course of a run, but I can't imagine that a 10-12 °F change in temperature could cause a measurable drop in resistance. I'm wondering if a collection of H2 bubbles on the cathode could gradually foul the conductive surface (analogous to scale fouling heat transfer surfaces). Or could there be a stagnant boundary layer of ions that build up in the bath, that similarly foul the mass transfer?
Marty Ganseraluminum processing - Minneapolis, Minnesota, US
2005
A. A 10 to 12 °F temperature change is a *HUGE* problem, Marty; you have to fix it.
Anodizing involves two competing reactions: the electrolytic formation of a very highly resistive oxide film vs. the constant dissolution of that film by the sulfuric acid (a reaction that is very temperature sensitive). When the film is thin or non-existent at the beginning of the process, there is almost no resistance, so the voltage must be very greatly reduced or the current will skyrocket, quickly causing unacceptable burning. But you cannot build an anodized film of any substantial thickness at that low voltage because, as the film builds, the resistance skyrockets and no current will flow. The only ways to anodize is by starting at a very low voltage and gradually and smoothly increasing that voltage in close proportion to the film thickness (or anodizing at a constant current). If the temperature rises by 10-12 degrees, the rate of dissolution of the film increases dramatically, so the thickness of the film is varying greatly, and the careful balance between film thickness and applied voltage is gone. It's not primarily a question of the change of resistance of the solution over a 10-12 degree range, it's a question of the change of resistance of the anodized film. Any temperature change beyond 2 °F is usually considered a problem.
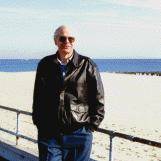
Ted Mooney, P.E.
Striving to live Aloha
(Ted can offer longterm or instant help)
finishing.com - Pine Beach, New Jersey
Q. Does the same hold true for "barrier" anodization?
We aren't using a sulfuric bath, but a near neutral (pH 6.5 ~ 6.7) organic electrolyte; we're only anodizing about 100nm deep, using constant voltage and a "cut-off time" to control film build (line speed controls dwell time in the bath). Typical production takes about 2 hours to process one spool of our product, but dwell time for a given unit length is less than 20 seconds.
I admit our temperature control should be tighter (an expenditure proposal is awaiting approval), but I've done some lab-scale batch tests which indicate that bath temperature needs to change almost 50 °F to see the same change in product quality that we see on-line with a 10 °F change.
Our product quality is highly dependent on the concentrations [proprietary] of our electrolyte, which we monitor closely during each run. Is it possible that something is happening at the interfaces (a concentration depletion or build-up) that wouldn't be noticed in the bulk solution?
Or am I overlooking the obvious temperature issue, and obsessing over a more exotic but unlikely culprit?
electronic components - Minneapolis, Minnesota, US
2005
by Larry Durney
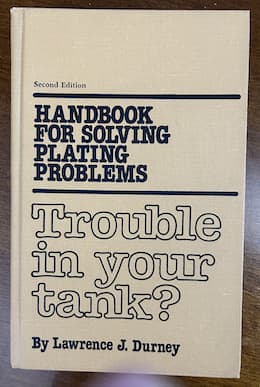
on eBay or Amazon
or AbeBooks
(affil link)
A. Books and the internet reveal that tartaric acid
⇦ on
eBay
or
Amazon [affil link] is often used for anodizing electrolytic capacitor foil, which may be somewhat similar to your process; I was slightly involved in tartaric acid
⇦ on
eBay
or
Amazon [affil link] anodizing 25 years ago. I don't recall the temperature control range that was imposed, but I'm sure that a 10 to 12 degree variation was not allowable even in those ancient days.
As Larry Durney reminds us in "Trouble in Your Tank", electrochemical processes are very complex... and not fully understood. Therefore, he tells us, a primary requirement is total consistency on everything that can be measured and controlled. In his words, electrochemical processes must be "Bible right" / "Letter of the law" right even though we may not know exactly why, or what the effects of the inconsistencies might be.
There certainly could be other causes for the problem; there probably are, and you're probably on their track ... but until we have temperature consistency -- one of the big-picture items that affects chemical activity, solution resistance, diffusion barrier dynamics, viscosity, hydrogen release, and other things -- we are operating out of control. So I think you should do what you can to push that expenditure appropriation through :-)
Good luck.
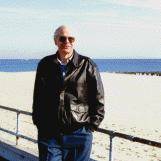
Ted Mooney, P.E.
Striving to live Aloha
(Ted can offer longterm or instant help)
finishing.com - Pine Beach, New Jersey
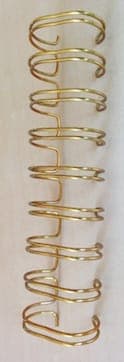
Q. Please inform me if a technology is available to online reel to reel Anodize wire in gold or other colors for making Book binding wires? Also, if we can coat aluminum on steel wire and then color Anodize? Is it expensive and practical?
Ismail Godhrawalawire - Mumbai, India
July 3, 2016
A. Hi Ismail. Continuous anodizing is not a problem per se. We appended your inquiry to a thread where we describe it's use for electrolytic capacitors, lithographic sheets, etc. What I predict as the larger potential problem is forming the wire after anodizing without ruining it because anodizing is a brittle ceramic-like coating. So I would suggest that you concentrate your efforts there -- by buying some anodized wire and making sure you can successfully and reliably form it and keep it formed right before committing to a continuous anodizing line which might not meet your needs. Aluminum craft wire is widely available and widely used. Good luck.
Aluminum cannot be electroplated out of a conventional aqueous plating bath. Although it is reportedly possible to anodize the plating after electrodeposition of aluminum from an organic plating bath, I think it would be too expensive & exotic for such an application. Good luck.
Regards,
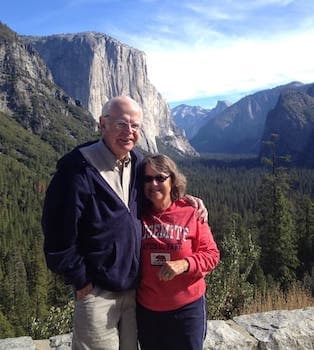
Ted Mooney, P.E. RET
Striving to live Aloha
(Ted can offer longterm or instant help)
finishing.com - Pine Beach, New Jersey
Q, A, or Comment on THIS thread -or- Start a NEW Thread