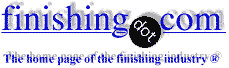
-----
Hexavalent chrome in surface of chromic acid anodized parts
Q. With the impending sunset date for the cessation of Hexavalent Chrome products, 21/09/2024 ... has anyone got the figures for the amount of Hexavalent Chrome content in the anodic layer?
There's mention in REACH of a one tonne limit related to the 0.1% wt/wt threshold?
If the amount of Cr3+ is > than 0.1% of the total weight of the part is it okay to continue with Chromic Anodise, as long as the weight is one tonne in total?
We're changing our Automated Chromic line to Sulphuric but it'll be interesting to know how everyone is interpreting the above?
Aerospace Special Process Engineer - Truro, Cornwall UK
March 21, 2024
Multiple threads merged: please forgive chronology errors and repetition 🙂
for Shops, Specifiers & Engineers
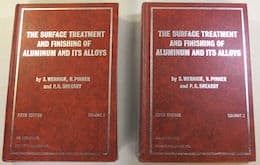
avail from eBay, AbeBooks, or Amazon
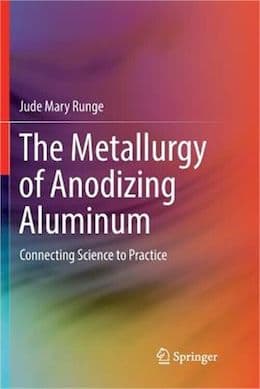
avail from eBay, AbeBooks, or Amazon
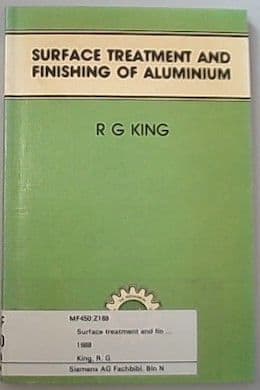
avail from eBay, AbeBooks, or Amazon
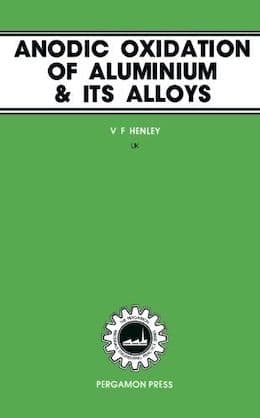
avail from eBay, AbeBooks, or Amazon
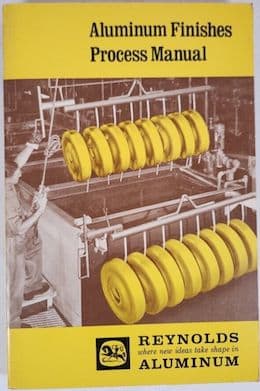
avail from eBay, AbeBooks or Amazon
(as an Amazon Associate & eBay Partner, we earn from qualifying purchases)
Q. Is there Hexavalent Chrome (Cr6+) left in the surface of anodized aluminum subject to the Chromic Acid Anodize process (Type
1)?
We have recently become concerned due to RoHS forcing us to look at alternative process' for surface treatment of our 7075-T6 aluminum parts. Since Hexavalent Chrome (Cr6+) is a carcinogen, left over bits on or in the surface of parts we handle without protection may be a definite concern. Has anyone studied this or have a source I can reference?
I have read text exerpts that state that: "Bengough and Sutton found
0.4-0.7 chromic acid in the coatings produced by anodizing in chromic acid, while Pullen and Scott, working with coatings sealed in water, found them to consist of almost entirely anhydrous Al2O3 with less than 0.1% of chromium". This statement obviously leaves questions as to how much, if any Cr6+ is left in the surface. The first part only says "chromic acid" while the second part says "chromium". Any help here would be appreciated.
Helical Products Co., Inc. - Santa Maria
2005
A. While you are investigating this, you may want to concurrently investigate Boeing's "boric-sulfuric" replacement technology.
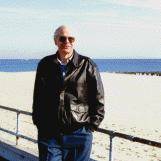
Ted Mooney, P.E.
Striving to live Aloha
(Ted can offer longterm or instant help)
finishing.com - Pine Beach, New Jersey
2005
Q. The Boric-Sulfuric anodize is not known to be as good or better at corrosion prevention so probably won't work for us. We also require a flexible surface that will not crack so any new process would have to be investigated and tested thoroughly. Our parts flex too much to leave it to chance. I appreciate the help but what I really want to know is how much hexavalent chrome is left in the surface. Health is my first concern, then comes complying with RoHS.
Michael H. Williams- Santa Maria, California, USA
2005
Q, A, or Comment on THIS thread -or- Start a NEW Thread