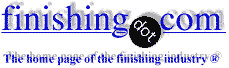
-----
How far should I test for salt spray (fog) testing according to ASTM B 117-90?
2005
Dear All,
Could anybody help me for this question ? How far / how long should I test Zinc coating for salt spay (fog) testing ? somebody said 8---12 hours is enough, somebody said over 100 hours is ok. which is right?
Many thanks !
Johnson Electric - Shanghai
Salt test to attain 150 hrs at what thickness of plating? I wanted to attain salt test at 150 hrs for yellow zinc (Cr6) on Cold rolled steel. How many micron do I need to plate ?
Harry ChuaManufacturing - Hong Kong
2005
Sandy,
The lab that is going to be doing the testing can probably give you a good idea of what kind of results you should expect, they'll also tell you that salt spray and salt fog are different test.
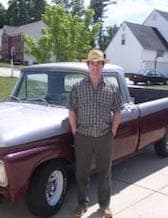
Sheldon Taylor
supply chain electronics
Wake Forest, North Carolina
2005
2005
Sheldon: thanks for noting that there are various accelerated corrosion tests; they include neutral salt spray, CASS, Corrodkote, and more. But I think that "salt spray" in this context is just a colloquialism that really means fog rather than literal spraying. Although it is possible, and might be a useful test to actually spray parts with salt water, I think that both 'salt spray' and 'salt fog' are meant to refer to neutral salt fog testing per ASTM B117.
Sandy: 8-12 hours is not much of a test, but 12 hours is the ASTM ASTM B201-80 expectation for minimum hours to white corrosion for traditional clear chromates, 96 hours for yellow, and 150 hours for olive drab. Due to RoHS and similar standards, however, traditional hexavalent chromates are rapidly disappearing anyway.
Harry: 150 hours to white rust is attainable with traditional olive drab chromates, and probably some of the new proprietary hex-free coating systems, rather irrespective of zinc thickness. But 25 microns is required for "very severe" conditions, 13 microns for "severe" conditions, and 8 microns for "moderate" conditions.
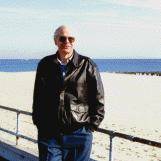
Ted Mooney, P.E.
Striving to live Aloha
(Ted can offer longterm or instant help)
finishing.com - Pine Beach, New Jersey
Q, A, or Comment on THIS thread -or- Start a NEW Thread