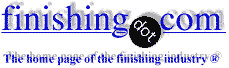
-----
White 'frostiness' of black passivated zinc plated components
2005
Does anyone have any ideas as to why I am getting a frosty appearance on our zinc plated shells which have a black hexavalent passivate. It only happens when the components go through a heat cycle. We have been zinc plating for years and this is a relatively new problem. After zinc plating the components go through an acid pre-dip to remove any brightener films before going into the passivate. After passivation they go through a post-dip fixer made with sodium thiosulphate
⇦ on
eBay
or
Amazon [affil link]
. When the parts have been blow-dried, they are kept for 3 days before any heat treatment to allow full drying.
It looks like when subjected to heat (125 C) something is leaching out onto the components?
We have in the last 2 years changed our zinc plating solutions from cyanide to non-cyanide based which deposits a heavy film, could this be anything?
Has anyone else had this problem?
Plating shop - East Sussex, England
First of two simultaneous responses --
No chromate conversion coating can withstand 125 °C. At that tempoerature the coating is dehydrated, the water steamed off, and the silver compound becomes molecular silver metal which is white in color.
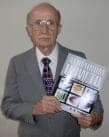
Robert H Probert
Robert H Probert Technical Services

Garner, North Carolina
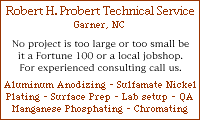
2005
Second of two simultaneous responses --
yes. I am also come across this problem with hexavalent yellow plated in alk.zinc when it is subjected to heat cycle.may be this is due to deposit characteristic from alk.bath or poor rinsing between plating and passivation.
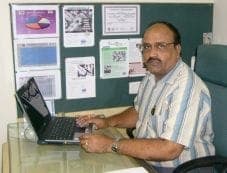
P. Gurumoorthi
electroplating process chemicals - Chennai, Tamilnadu, India
2005
What is the reason for doing a heat tretment of zinc plated parts with 125°C after three days ?
Marcus Hahn- Lucerne, Switzerland
2005
Just check if these parts have higher porosity than the parts that you were plating earlier. Also check the rinsewater in passivation is pure DM.
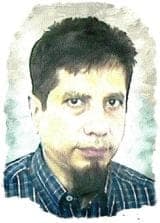
Khozem Vahaanwala
Saify Ind

Bengaluru, Karnataka, India
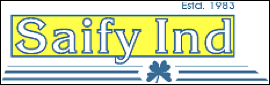
2005
2005
Chris
Non cyanide alkaline plating usually have more caustic content than cyanide bath.please look in to the pre dip prior to passivation. you may need to maitain the strenght periodically. Try to keep it at
>1%.This will prevent caustic entering in to the passivation soln.
As Robert and Gurumoorthi rightly said 125 degree heating seems to be more.
Also try the possibility of heat treatment prior to passivation
Good luck
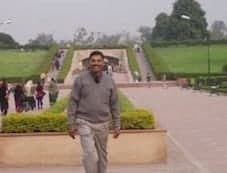
T.K. Mohan
plating process supplier - Mumbai, India
Q, A, or Comment on THIS thread -or- Start a NEW Thread