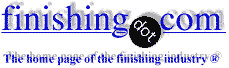
-----
Need opinions on surface preparation for good EN plating
I am a Manufacturing Engineer who has learned a lot about EN plating over the last two years thanks to this site, other articles and documents. Any opinions/suggestions would be greatly appreciated here.
The parts are composed of three materials: Silicon core iron (2.5% silicon) flanges, 304 SS shunt & silver alloy braze rings. The part is a bobbin with a blind hole .265 in dia by .650 deep. We have been experiencing many problems with Electroless Nickel (high phos) for quite some time (nodules, skipped plating, porosity, pitting ˜ apprx. 25% fall back). Through research I believe that I can minimize the problems by paying closer attention to the surface finish prior to plating. Surface finish is roughly 45Ra, substrate contains dings and pits when observed under microscope. Dings and pits are obviously still noticeable after plating, plated over. Also the plating itself contains severe pitting caused by rust, bare areas, pores, etc.
My plater tells me that the parts require a glass bead blast (US AH
170-325 sieve impact beads at 60 psi) to prepare the material for good adhesion. Which they have been doing for us for a long time now. Also, they must clean the glass bead out of the blind holes with a small wooden dowel because apparently the beads don't wash out well during pretreatment. I have sent some plated parts out for material testing to find out that nodules in the plating are caused by glass bead particles embedded in the material and also mixed in with the plating. I'm running out of ideas on how to solve these issues and I'm not sold on the fact that we have to use glass bead as a blast media.
My question is: Is there a more effective way to activate the material besides the glass bead blast? Do these parts require the bead blast? I may look into wheat starch as a media.
Thank you for taking the time to read and respond.
Aerospace - New Haven, Connecticut
2005
Hello, Larry. Just one person's opinion, and one way of looking at the problem but as an engineer I was taught the engineer's truism: "Get the chemistry right before you start the engineering". Applying that to a case like this means to me: you've done the chemistry, and glass bead blasting works well, so that's what you should use. Now you do the engineering of solving the problem of trapped media, and the first idea that would occur to me would be good ultrasonic cleaning.
I can't guarantee it will lead to a solution, but that's what I'd do.
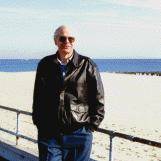
Ted Mooney, P.E.
Striving to live Aloha
(Ted can offer longterm or instant help)
finishing.com - Pine Beach, New Jersey
2005
Ted is right about using ultrasonic to clean after blasting. However, if you need an alternative surface improvement, normally mass finishing will give you better results. Type and size of media is important, but it without more info, I can not make a recommendation.

AF Kenton
retired business owner - Hatboro, Pennsylvania
2005
Thanks for your input guys, I really appreciate it. I can provide more info on this issue as it is a problem that we have been struggling with for a while. I should mention that we are using ultrasonics as a cleaning method, but it is not effective enough to rid the parts of glass bead. I think I will be experimenting with sodium bicarbonate.
My plater states that because we require plating on a part made of dissimilar materials, the parts need to be glass bead blasted. The problem is Nodules mixed in with the plating (which I sent out for evaluation and proven that it is glassbead mixed in with the plating, and beads that are embedded into the material also causing nodules). Our current plater removes glass beads from the blind holes of each part with a toothpick, which drives are costs up. I'm not sold on the fact that glass bead blast is the only way get good adhesion.
Aerospace - CT
2005
First getting back to glass beads. I am sure you are aware of different sizes of media that are available. Second, besides ultrasonic tanks there are probes and/or special fixtures for such problems. Third,I agree with your statement,"I'm not sold on the fact that glass bead blast is the only way get good adhesion.", but it does produce the greatest amount of surface area for contact. I am biased toward mass finishing systems.

AF Kenton
retired business owner - Hatboro, Pennsylvania
2005
Both the 304SS part and the silver alloy braze rings won't rust or corrode easily. Is it a must they need to be electroless plated. Could you just plate the silicon iron? This would eliminate the need to glass bead blast and replace it by a wet preplate process for this type of iron alloy. Al
Guillermo MarrufoMonterrey, NL, Mexico
2005
Q, A, or Comment on THIS thread -or- Start a NEW Thread