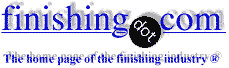
-----
Nickel Coating on Epoxy Glass 3-D Substrates
Q. Hello,
We are interested in a process for applying a nickel layer onto large
(~1'x4'x 0.040"thick ) 3-D epoxy glass substrates. The goal is to deposit 0.0005 to 0.001 inches of nickel; preferably an initial Ni coating could be a seed layer in the range of 0.00005" thickness for subsequent electroless nickel plating.
We would prefer to avoid using aggressive etching chemicals such as chromic acid and permanganate and solvents, both for environmental and surface finish reasons (we do not wish to expose the glass any more than necessary). Additionally, even if the parts are etched in the typical processes, we are skeptical about the ability of etching and a liquid catalyst to uniformly coat such large areas. We have tried a few experiments with plasma etching and ion beam assisted PVD, but have had experienced loss of adhesion--particularly after electroless plating over the deposited coating. We have had some success with some catalytic paints. Thanks in advance for your help.
- Raleigh, North Carolina
2005
A. From this distance your problem doesn't sound much different than electroless copper plating of printed wiring boards. So I think you could use a standard cycle up through electroless copper, then enough electrolytic copper that you could spark the substrate for deposition of electroless nickel.
Naturally, it would be easier and more straight-forward to just go with electroless nickel from the get-go and forget the copper; I only mention it because it is a proven technology for something that sounds very similar, and it's always nice to be confident that a workable technology exists.
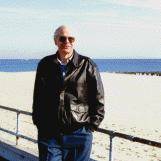
Ted Mooney, P.E.
Striving to live Aloha
(Ted can offer longterm or instant help)
finishing.com - Pine Beach, New Jersey
Q. Ted, Thanks for your response. We were trying to avoid the various etching and liquid catalysts because the parts are so large and relatively thin (0.03" layed-up epoxy glass). We feel it would be very difficult to put a uniform thickness of metal (nickel in the range of 0.0005-0.0001" thick (no copper)) on the parts with chemical etching and liquid catalysts. We are putting circuitry on these compound curved parts, and have seen issues with surface roughness, and metal entrapment in the fibers with aggressive etching. However, if a reader knows of someone with experience with metallizing epoxy-glass, we would consider it. Therefore, we have been investigating various catalytic paints and use of a vacuum-deposited seed layer. I was also interested in use of an intermediate base coat to improve adhesion and surface finish prior to nickel deposition of the seed layer. Thanks in advance for your input.
Charles Rudisill- Morrisville, North Carolina
Q, A, or Comment on THIS thread -or- Start a NEW Thread